0 前言
随着消费者需求日益多元化以及造车新势力的发展,汽车市场更新换代的频率也与日俱增,价格比拼更是暗流涌动。对于汽车厂商而言,为消费者提供更多车型选择的同时,也需要开源节流,控制成本。厂房面积及设备的投资成本往往是各大主机厂降本增效的痛点,一味扩大厂房、复制线体明显与精益生产的大环境背道而驰,同时控制工厂工艺面积也是各大主机厂需要深入研究的重要课题。双层一拖四换模机构应运而生,该机构兼备占地面积及多车型切换优势,已逐渐成为各主机厂车身车间的首要选择。本文基于传统双层一拖四换模机构框架,提供一种更为精益的改进方案以进一步压缩占地面积及设备投资成本。
1 双层一拖四换模机构应用范围
在车身车间门盖生产区域,一般将不同车型前盖、四门及后盖或举门按照产品类别放在同一线体生产,例如前盖线、四门线(通常一种门一条线)和后盖线。对于 8 车型车间而言,会有 8 种前盖、32 种门以及 8 种后盖;若使用一拖八换模机构(由对称分布在压机两侧的两套双层一拖四换模机构组成),相应地至少会有 1 条前盖线、4 条门线以及 1 条后盖线,共计6条门盖生产线。
2 传统双层一拖四换模机构组成
传统双层一拖四换模机构的主要组成部分如图1所示,包括:模具放置层,单侧上下布置2个放置层能够存放 4 个车型模具;模具垫板用于承载模具;推拉机构用于驱动模具在换模机构内的横移以及模具在换模机构与所属压机之间纵向移动;升降机构用于模具的升降移动。
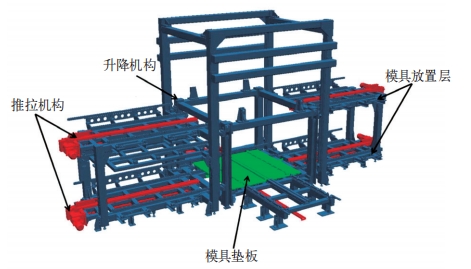
图1 传统双层一拖四换模机构主要组成部分
3 传统双层一拖四换模机构的限制
市场上现存的传统双层一拖四换模机构普遍采用两个电动机驱动推拉机构进行模具横移,对于车间设备日常维护及故障维修而言,需要在换模机构两端各布置一个电动机维修平台,如图 2 所示。这不仅增加了场地面积与设备投资,还加大了后期车间设备的维护保养压力。
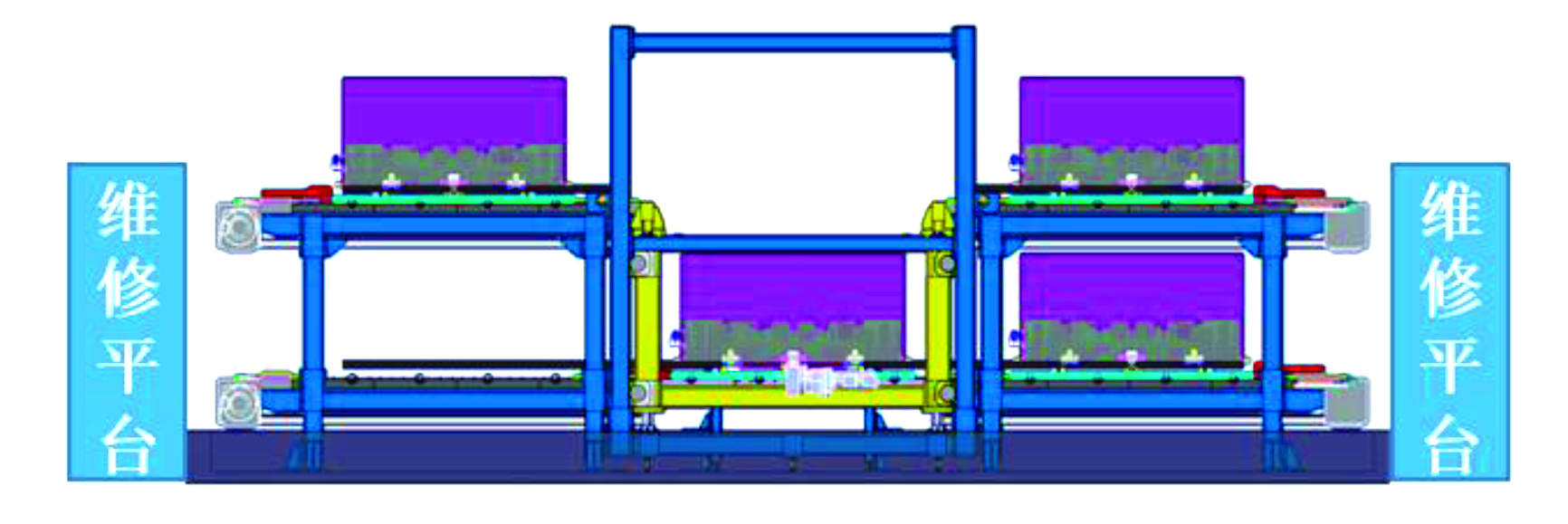
图2 电动机维修平台
此外,对于高节拍工厂的门盖压机区域,往往设备量大且布局紧凑,压机折边工位前后通常需要布置多车型的搬运抓手存放架、七轴机器人、涂胶设备、合拼台、预滚边及 Plasma 焊机等设备。如果需要对现有线体进行多车型扩展改造,还需要考虑压机单元附近的设备布局情况,这就对线体面积及工艺规划提出了较高的要求和限制。因此,需要在车型拓展时最大化利用预留工艺面积,减少现有设备的移位。
我公司某车身车间多车型引入现有线体,门盖生产线压机区域需新增 1 套双层一拖四换模机构,放置于如图 3 所示的换模机构预留区域。
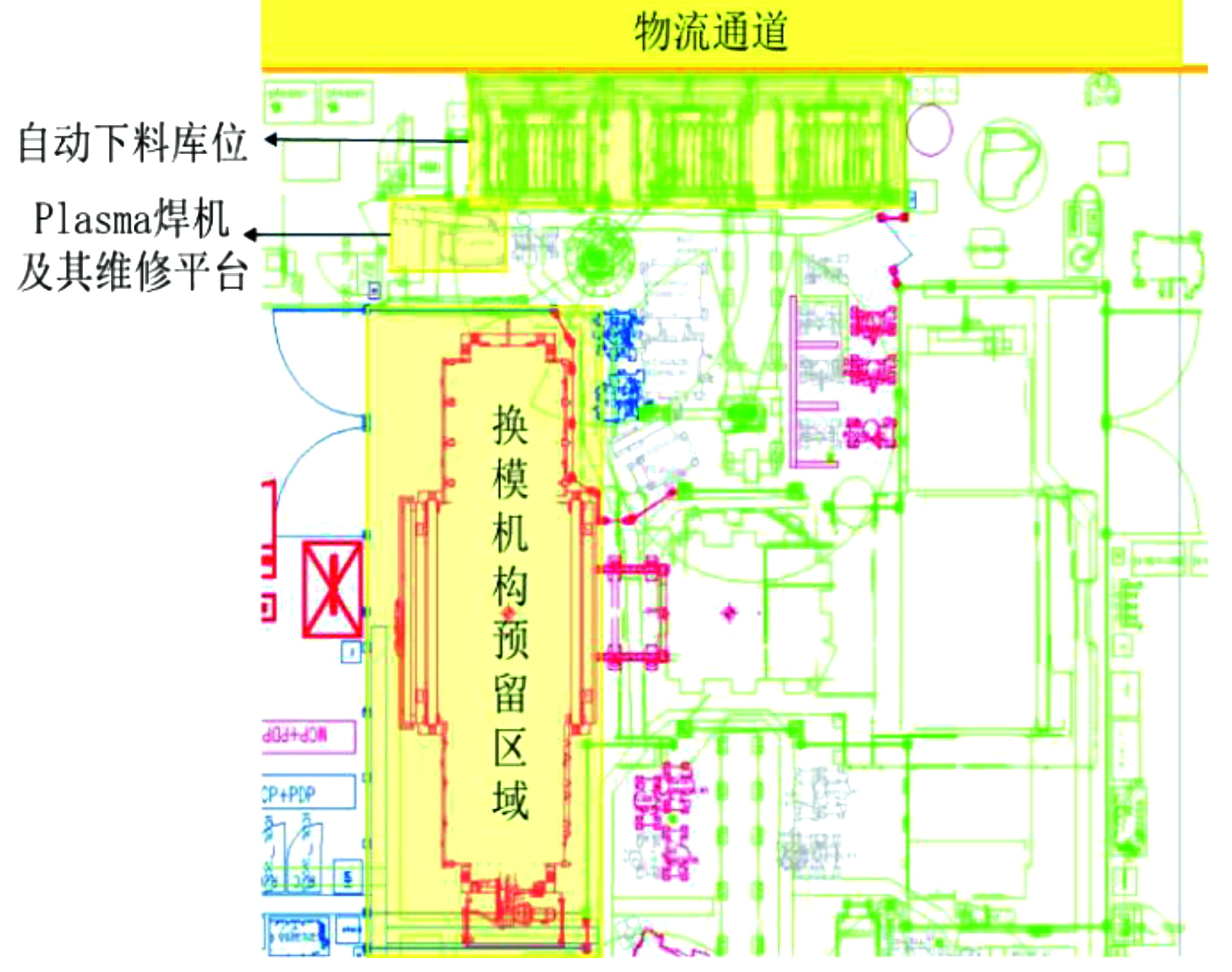
图3 换模机构预留区域示意
如 果 采 用 传 统 双 层 一 拖 四 换 模 机 构, 则 靠 近Plasma 焊机侧需布置一个电动机维修平台。如图 4所示,经仿真模拟后发现,新增电动机维修平台与现有焊机维修平台干涉,且受限于现有设备布局情况,Plasma 焊机已无移动空间,只能将其附近自动下料库位及机器人进行搬迁,由此引发搬运抓手存放架、合拼台的搬迁以及机器人轨迹的调试。粗略估算单条线体改造费用约 76 万余元,改造条目见表 1。对于四条侧门生产线而言,整体改造费用高达 300 余万元。此外,线体改造还需额外的停产窗口,造成工厂不必要的产能损失。因此,对于此新增双层一拖四换模机构,需要其结构更为紧凑,以满足现场使用需求。
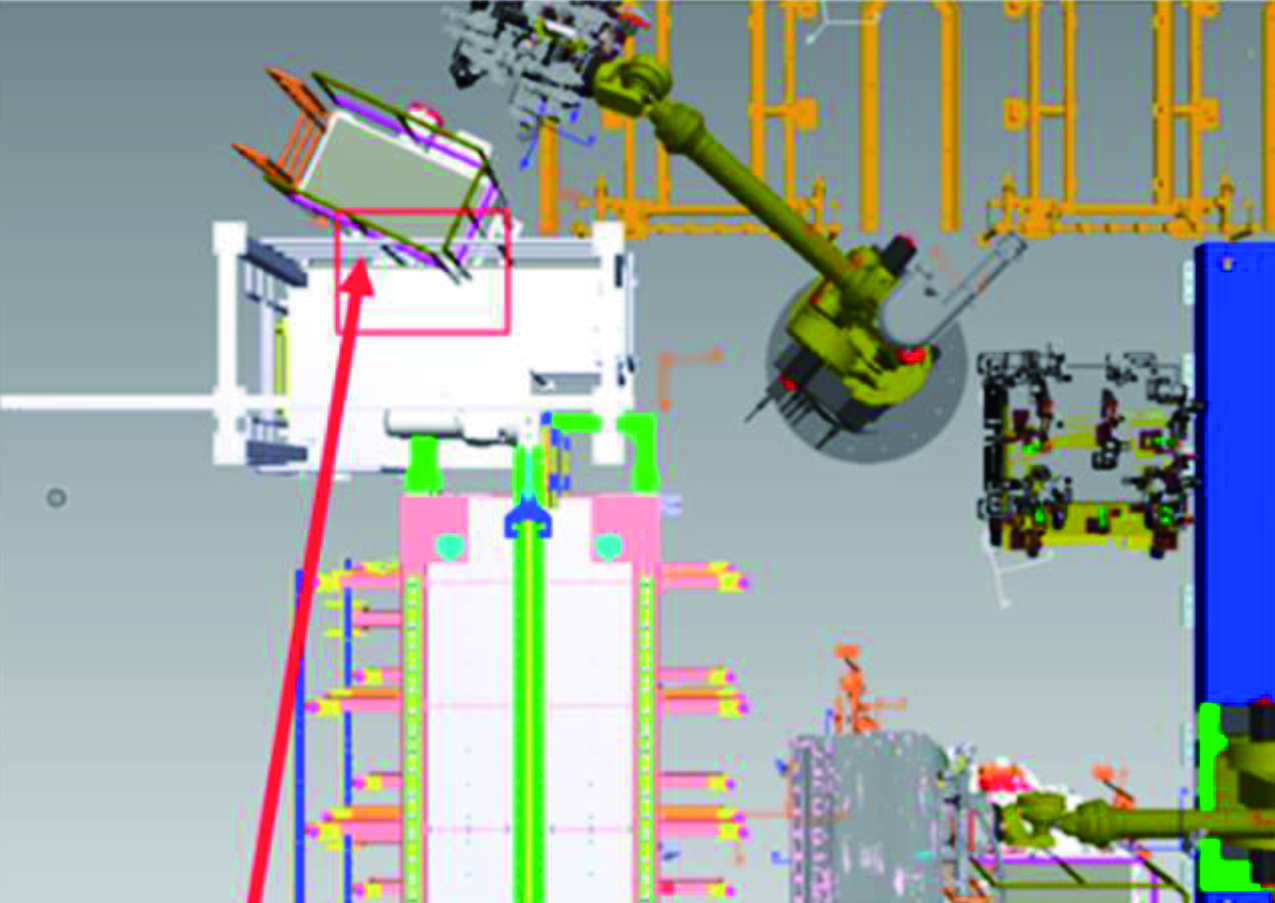
图 4 仿真模拟示意
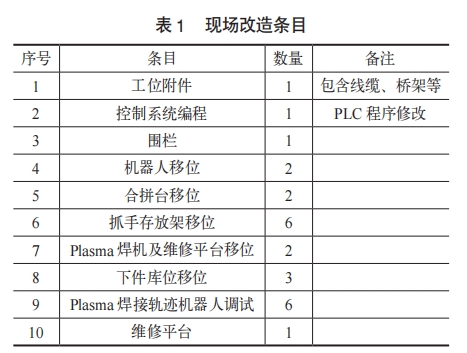
4 紧凑型单侧双层一拖四换模机构原理
如图 5a 所示,传统双层一拖四换模机构在模具放置层两侧均需布置驱动电动机控制推拉机构实现模具垫板的左右移动,上、下层合计 4 个驱动电动机;如图5b 所示,紧凑型双层一拖四换模机构仅需在模具放置层一侧布置驱动电动机,上、下层合计 2 个驱动电动机。
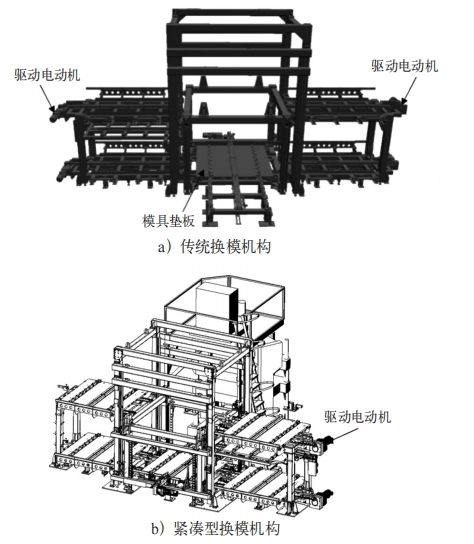
图5 驱动电动机布局对比示意
实现单电动机驱动功能的首要原因在于模具垫板的设计优化。如图 6a 所示,传统模具垫板两端有两个固定挂钩,用于与两侧推拉机构上的挂 / 脱钩机构配合,实现模具移动前后与推拉机构的连接和脱开。如图 6b所示,紧凑型单侧双层一拖四换模机构所用模具垫板仅一侧有一个固定挂钩,另一侧由挂 / 脱钩机构取代。
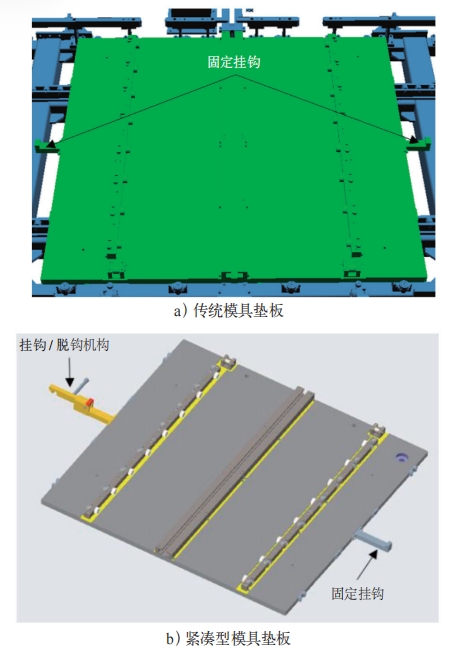
图6 模具垫板对比示意图
5 紧凑型单侧双层一拖四换模机构换模流程
图 7 所示为紧凑型单侧双层一拖四换模机构四车型模具布局,模具 A 在压机内的工作位中,此时换模机构内 4 个库位只有 3 套模具,可以利用 1 个空库位完成备模的工作。
以 B 车型为待切换车型为例,将图 7 中右下角的库位定义为 A 库位,左下角的库位定义为 B 库位,A、B 库位之间定义为过渡位置,模具横移单个电动机驱动过程如下:
(1)垫板临时存储区(图 7 中 Z 所示)驱动电动机将 A 模具垫板推到升降机内,此时升降机内气缸(图8)应该为顶起状态,模具垫板上挂 / 脱钩机构顶杆与气缸接触后被顶起,处于打开状态,随升降机下降到一层。
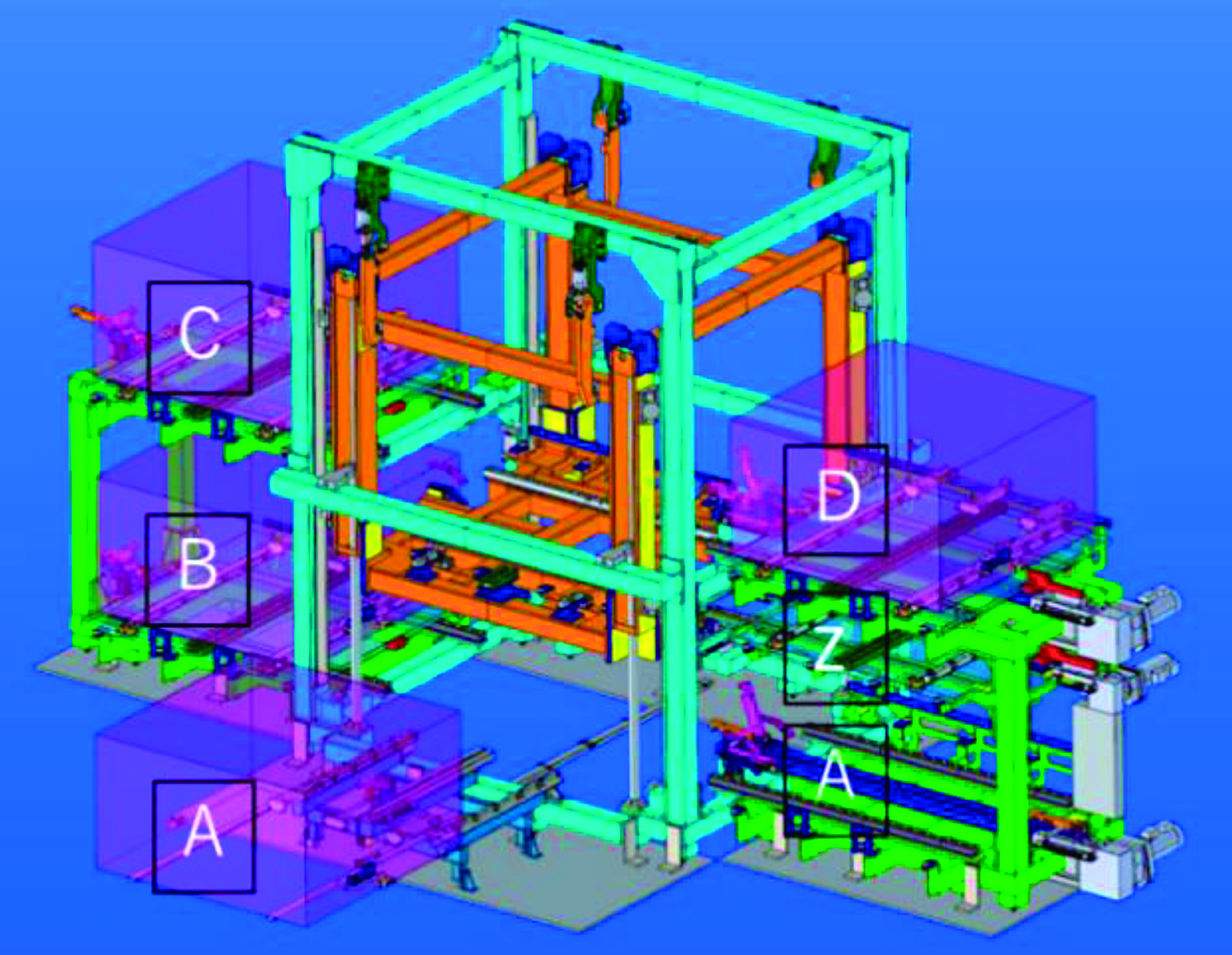
图7 紧凑型单侧双层一拖四换模机构四车型模具布局示意
(2)升降机内气缸下降,挂 / 脱钩机构在自重作用下随气缸下降并与 B 库位内模具垫板固定挂钩连接。
(3)纵向电动机驱动推拉机构将模具 A 从压机内拉到升降机内的 A 模具垫板上。
(4)一层横向电动机驱动推拉机构将升降机内的模具 A 及其垫板拉至 A 库位,同时将 B 库位的模具 B及其垫板运送到升降机内。
(5)纵向电动机驱动推拉机构将 B 模具脱离垫板并送至压机内。上层模具与下层模具之间的切换过程同理,此处不再赘述。
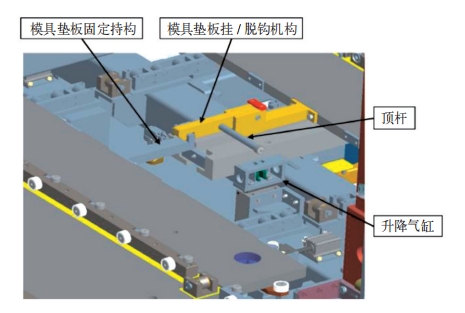
图8 升降气缸作用原理示意
6 两种换模机构特性对比
根据换模机构的使用特性,在不考虑模具垫板临时放置层的情况下,从占地面积、驱动方式、电动机选型、电动机数量及推拉机构数量等多个维度,对传统单侧双层一拖四换模机构与紧凑型单侧双层一拖四换模机构进行对比(节选自某现有品牌设备),见表 2。 可以看出,相对传统单侧双层一拖四换模机构,紧凑型单侧双层一拖四换模机构在占地面积与零部件数量等方面占据一定优势。
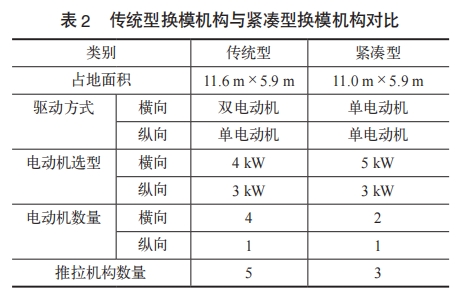
7 结论
与传统换模机构相比,紧凑型换模机构最大的优势在于节省了占地面积以及减少了零部件数量 , 达到了节省场地与设备等投资,同时减轻设备维护压力的目的。同时,必须认识到此种新型模具垫板结构相对复杂,模具在换模机构内移动时,需借用另一模具垫板进行过渡,中间环节较多,控制逻辑更为复杂,中间过程风险也会同步增加。
参考文献
[1] 阮宜进 . 双层一拖八换模机构在车身车间的应用 [J].AI 汽车制造业 ,2021(3) :37-39.
本文为“AI汽车制造业”首发,未经授权不得转载。版权所有,转载请联系小编授权(VOGEL100)。本文作者:姚舜文,单位:上汽通用汽车有限公司。责任编辑龚淑娟,责任较对何发。本文转载请注明来源:AI汽车制造业
评论 0
正在获取数据......