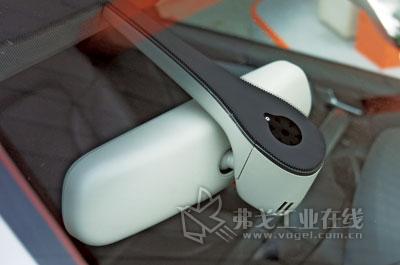
图1 一个用于前照灯和挡风玻璃雨刮器控制的组合传感器的安装示意图,它被集成到了安装在汽车挡风玻璃上的后视镜支架上
一种发动机汽车用的雨、光和湿度传感器外壳,仅在其直径只有33mm的上部,就容纳了7个红外线雨水探测器和2个用于检测周围光线水平的镜片。一个含有嵌入成型金属接触插件的连接插头是另一个被集成到该外壳中的组件。一台由威猛提供的注射形式超级紧凑的立式3组分注塑机被用于该部件的生产。
为提高安全性和舒适性,每一辆现代汽车都安装了大量的电子系统,传感器就是此类系统中的重要部件。作为汽车传感器多功能外壳部件的专业生产厂商,奥地利家族企业、位于奥地利马蒂希霍芬附近Schalchen的Promotech公司生产的一种外壳部件,被用于发动机汽车的雨、光和湿度传感器(如图1所示)上。该传感器的外壳包含了3种不同类型的聚碳酸酯(PC)(如图2所示):材料牌号1是水晶一般透明的聚碳酸酯,它被用于生产两个镜头,以用于检测周围光线(触发汽车照明)和照向迎面车辆的前照灯光线(控制自动变暗);材料牌号2是一种紫色聚碳酸酯,被用于生产安装在一个六角形部件角落的6个镜片以及一个额外的中央镜片,这些镜片为红外光束的接收和发射提供了支持。这些光束由一个位于一侧的LED灯发出,并被挡风玻璃的边界面反射到位于另一侧的接收器光敏二极管上。然而,只有干的挡风玻璃才能完全发射该红外光束。一旦挡风玻璃上有雨滴,对红外光的反射就会受到干扰,并且只有部分光线会到达接收器的二极管上。对照挡风玻璃干态时的光反射度,光反射强度的差异控制着挡风玻璃雨刮器的动作。这些镜片被嵌入成型到一个采用黑色聚碳酸酯制成的外壳中。另一个集成到外壳中的部件(总重量不到5g)是带有3个嵌入成型的凸起接触插件的连接器(如图2所示)。这些外壳还通过一个“flexband”被连接到一个湿度传感器上,该传感器可探测挡风玻璃内部的湿度并据此触发吹风机。
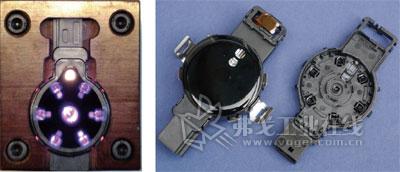
图2 该雨、光和湿度传感器是一个含4个组成部分的部件,包括:两个由水晶般透明聚碳酸酯制成的镜片;7个由紫色聚碳酸酯制成的镜片;由黑色聚碳酸酯制成的外壳;3个金属接触插件被放入模具中,然后通过嵌入成型而成为该部件的第四组成部分
微注射量与标准注射量的组合
比较3种聚碳酸酯组件的重量,可以清楚地发现,生产这种3组分的部件需要一种组合了微注射成型和标准注射成型的技术。每一个成型好的部件都包含有0.1g水晶般透明的聚碳酸酯、0.2g紫色聚碳酸酯和用于外壳的4.2g黑色聚碳酸酯。在这一要求4个型腔的生产中,分别为0.4g、0.8g和16.8g的总注射量依旧保持在标准注射成型技术的下限水平,尤其是在第一个双注射工位上。无浇口料的生产在此是可行的,因此也无需考虑回收利用的问题。因此,选择理想的注塑成型技术对于Promotech公司的项目团队而言是一个现实的挑战,特别是还必须将嵌件和3个嵌入成型到每个部件中的接触插件集成到注塑成型工艺中。Promotech公司的项目负责人Christoph Feichtenschlager介绍说:“多年来在生产金属/塑料混合部件中积累的经验,使我们决定选择一台立式注塑机概念。我们还想直接注射全部的3种材料组分,这就是说,要在每一种情况下使用一个热流道系统。虽然其中的一些注射量相当小,但我们还是希望最大程度地缩短材料在热流道分配器中的停留时间。因此,只有拥有尽可能最短的熔体通道和最小熔体容量的最紧凑的注塑成型系统才能够实现我们的目标。这一概念为我们的投标程序提供了基本原则。在对几个注塑成型系统进行比较后,我们最终发现,由注塑机制造商威猛巴顿菲尔提供的注塑概念是适合我们需求的最好方案。”
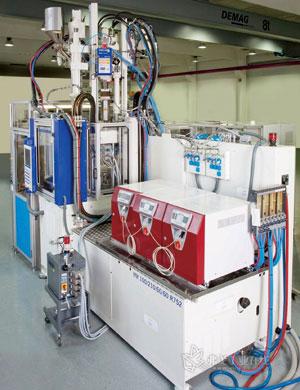
图3 包含了3种不同类型的聚碳酸酯和金属嵌件的雨/光传感器外壳在威猛巴顿菲尔的VM 100/210/60/60 R 752立式注塑机上被生产而出。该注塑机装配了带有752mm转盘的4拉杆100t立式锁模单元,以及3个小注射量的立式注射单元
超紧凑的立式注塑成型机
威猛巴顿菲尔的解决方案是一台具有复杂名称的注塑机型号VM 100/210/60/60 R 752(如图3所示),该名称代表了这台机器拥有一个立式、全液压和4拉杆的100t锁模单元,以及一个直径752mm的3工位转盘和3个同样是立式的注射单元(尺寸分别为60、60和210)。前两个带有14mm螺杆的注射单元是拥有标准螺杆的最小型注射集料筒,第三个注射集料筒则装有一个30mm的螺杆。
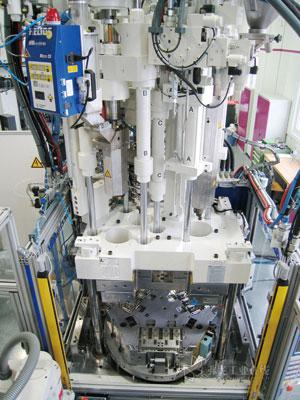
图4 3个布置尽可能靠近的注射集料筒(A尺寸为210,带有一个30mm的螺杆;B和C尺寸为60,各带有14mm的螺杆),连同为最小熔体容量而设计的热流道一起,被安装到752mm的3工位转盘上
威猛巴顿菲尔的项目协调员Wolfgang Glawatsch介绍说:“虽然我们可以尽可能地从我们的标准系列中获取模块,但这个系统的设计根本就不是一个标准任务。正如前面已经提到的,材料流通路径以及材料在热流道系统中流量的最小化,是在机器结构设计中首要考虑的因素,以确保聚碳酸酯的停留时间以及因此而对材料带来的潜在危害能低于临界水平。”
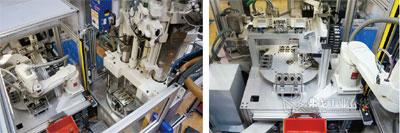
图5 一台水平关节式机器人将注塑机与检测站联系起来。检测后,部件通过一个传送包装工作站被码放到输送托盘中
因此,所有参与该项目的合作伙伴必须从最一开始就要围绕“最大程度的紧凑性”而开展工作。在这些合作伙伴中,除威猛巴顿菲尔外,还包括热流道系统制造商Mold Masters、模具制造商KTW以及自动化设备制造商MKE。该项目的实施要求在多个方面打破陈规,例如,需要将生产这种多组分注塑成型部件(嵌入金属插件、注射3种不同的材料以及取出最终制品)的5个原始生产步骤整合到仅有的3个工位上,这种集成是将3×4(腔)的模具系统装到752 mm转盘上的唯一方法。
相当紧凑的小量注射成型包
将两个微型注射单元集成到3工位转盘上的一个工位上,使得仅使用一个热流道系统同时在两个水平上通过针阀闭合喷嘴导入两种材料成为可能,每个针阀喷嘴对应每个型腔的5个注射点。为此,该机器的设计师将两个彼此尽可能靠近的集料筒(如图4所示,被命名为“B”和“C”)放到了机器的定模板上。尽管采取了所有这些机器和模具技术上的措施,但是还必须额外采取一种工艺技巧,以确保材料在热流道中有一个安全的停留时间。也就是说,连同每个部件一起只形成一个小量的料盘,在每次生产循环结束后,部件取出系统会将该料盘转送到回收处理单元。
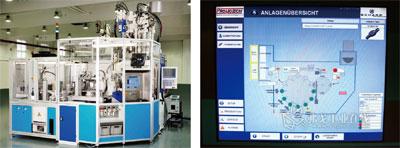
图6 威猛巴顿菲尔的注塑机是一个综合性生产单元的一部分。该生产单元不仅可生产用于接触插头的冲孔部件,还可对最终的注塑成型件进行检测(插头功能、完整性和尺寸)。这些插头随后被码放到输送托盘中
在下一步生产过程中,利用标准料筒(A)、采用嵌入成型方式生产出周围装有这些独特光学部件的外壳。在转盘的第三工位上,一个操作装置同时完成最终部件的取出工作。随后,立即将金属接触插件放入型腔中,这可在冷却期间,通过一个高精密的机械手臂来完成。所有这些都在21 s的生产循环周期中实现。
生产单元中的立式注塑成型系统
威猛巴顿菲尔的注射成型系统只是一个复杂生产单元中的一部分。除注塑机外,该生产单元还包含两个旋转循环系统,最终的注塑成型部件可在其中得到检测(插头功能、最终部件的完整性及其尺寸等)。接着,这些部件被码放到输送托盘上。注塑机与用于检测和包装的周边设备之间的工作连接是由几台水平关节式机器人来完成的(如图5、图6所示)。与此同时,对用在连接插头上的金属接触插件进行冲孔和精密弯曲,以准备好由抓取系统将其转送走。所有这些由设备完成的工作都被包容在同一个生产单元中。“尽管如此复杂,但我们的日常生产实践证明了采用我们概念的正确性,这在很大程度上要归功于威猛巴顿菲尔在纳米级和微型注塑成型技术方面积累的经验。” Promotech公司总经理 Günter Benninger在他的现状总结报告中作了如此评价。
评论 0
正在获取数据......