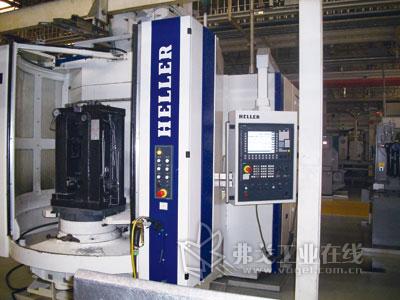
在发动机缸体、缸盖、框架、曲轴、凸轮轴和连杆等主要零件的加工过程中,刀具材料的合理选用在企业进行高质量、高效率和低成本的生产过程中扮演着重要角色,受到越来越多的企业关注。
越来越复杂的加工工艺,繁重的切削负荷和恶劣的工作条件,让人们对刀具材料提出了更高的要求。以发动机为例,人们希望刀具材料应具备以下性能:足够的硬度和耐磨性;足够的强度和韧性;较高的耐热性和传热性;较好的工艺性和经济性。然而,上述几项性能之间有些又是相互矛盾的,没有任何一种刀具材料能够兼备所有性能的最佳指标,如硬度高的刀具材料其强度和韧性较低,所以刀具材料的合理选用十分重要。
随着高速加工中心在生产中的普及,适合高速切削的CBN刀具在发动机零部件的制造中得到大量应用。尽管CBN刀具价格较贵,但其对于加工效率的提高和在投资成本上的节约,取得的经济效益却是非常显著的。
CBN刀具材料特点
CBN材料是由六方氮化硼在高温高压下加入催化剂转变而成的,硬度高达8 000HV~ 9 000HV,仅次于金刚石,但其耐热性却比金刚石好得多,在高于1 300℃时仍可切削。CBN材料化学惰性大,与铁索材料在高温1 200℃~1 300℃下也不易发生化学作用,导热性好,摩擦系数低,不易产生积屑瘤,工件表面质量好。因此,CBN材料作为一种新型超硬磨料和刀具材料用于加工硬的钢(HRC40~70)、铁和球墨铸铁(黑色金属),不适合加工HRC35以下的较软材料。
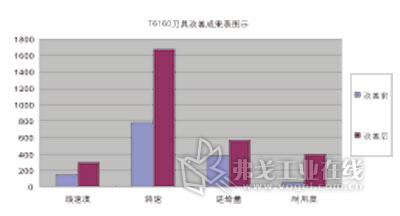
图1 T6160刀具的改善成果图示
CBN刀片是在高温高压下,使聚晶立方氮化硼和硬质合金基体形成一体的圆刀片,上面一层为厚0.5mm的聚晶立方氮化硼,下面一层为硬质合金基体。刀片总厚度有3.2mm和4.8mm两种。这种复合刀片具有CBN材料的硬度,又具有硬质合金的韧性。根据需要形状和尺寸,圆刀片可以切成45°、60°和90°的扇形或半圆形小刀片,焊在硬质合金或刀杆上用,也可以直接使用整体的复合CBN刀片作可转位刀片用。加工淬硬钢和铸铁时,耐磨性和刀具寿命比硬质合金刀片高30~50倍,比陶瓷刀片高10~20倍。加工淬硬钢和铸铁时,耐磨性和刀具寿命比硬质合金刀片高30~50倍,比陶瓷刀片高10~20倍。
同时,在应用CBN刀片时应注意下列几点:
1. 加工对象为HRC45以上淬火钢、铁和球墨铸铁等黑色金属或HRC35以上耐热合金和HRC35以下难加工的软铸铁。
2. 使用CBN刀具的机床必须刚性好,有足够的功率。
3. 安装CBN刀具,伸出的长度要尽量短,防止刀杆振动。
4. CBN刀具的刀刃必须磨出倒棱或小圆角。
5. 使用CBN刀具尽可能采用负前角和小于75°的主偏角。
6. 可以不用冷却液,要用就要充分。
7. 加工超耐热合金时、工件切入一端必须先倒角。
8. 确定刀具寿命的标志,必须在磨钝之前及时重磨(可刃磨两次)更换,不能等磨钝再换,这样易打刀。
9. 确定切削速度和进给量要综合考虑生产效率、刀具寿命和成本影响。
10. 切削时产生振动马上停止,及时换刀或装夹。
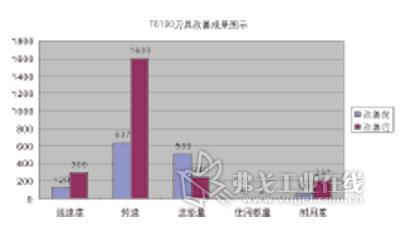
图2 T6190刀具改善成果图示
CBN刀具加工发动机零件
立方氮化硼(CBN)刀片在发动机零件中的应用体现了加工过程中的高质量、高效率和低成本的基本要求。它在金属切削加工过程中可以实现以镗代替磨削工艺,从而使产品的零件尺寸精度高、尺寸一致性好,形状误差小,可减少零件的检测项目,生产效率提高;同时刀具的挤压作用,被加工零件的表面受压应力,有利于提高零件的表面疲劳强度。加上CBN材料刀具的高耐磨性,其使用寿命远远高于硬质合金刀具,且加工的速度远高于硬质合金刀具,被加工零件尺寸稳定;生产现场刀具管理费用大大减低,加工零件工序能力指数高且稳定,可大大减少零件的抽检频次,设备的使用费、电费、工费和管理费也会下降。
1. 加工四缸发动机缸体
(1)改善前现象描述:加工四缸发动机缸体的缸体线OP10工序T6160刀具。该刀具加工缸体曲轴孔粗加工,自项目验收后一直使用进口硬质合金刀片,一次性使用数量12片;由于毛坯余量大,刀片的耐用度只有50件/刃,连正常的一个生产班次都满足不了。此道工序的生产节拍已成为这条生产线的瓶颈工序。
(2)过程分析:运用8D原则对现场的加工过程一一进行分析。由于每次更换的硬质合金刀片磨损状况比较严重,于是对刀具的工艺参数、更换涂层方式、刀片槽型以及刀具的材料等方面进行分析试用,根据刀具材料的硬度、耐磨性、导热性、传热性和工艺性等基本特性的对比,最终确定选用CNB材料的刀片进行加工。
(3)改善后现象描述:OP10工序T6160刀具选用CBN刀片后,不但解决了此条生产线的瓶颈工序问题,提高了生产节拍,而且大大降低了发动机单台制造成本,节约刀具成本费用3.3元/台。T6160刀具优化的相关参数和寿命如图1所示。
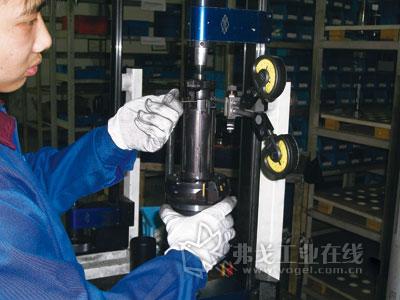
2. 以精镗代替珩磨
(1)改善前现象描述:为了保证发动机缸体曲轴孔加工的工艺质量精度的高要求,通常最后一道加工采用珩磨方式,而我公司四缸发动机缸体的缸体线OP120工序以T6190刀具取代了传统的珩磨加工。此条生产线自机床厂家交钥匙时采用的是非常有经验的国际著名厂家的硬质合金刀片进行精镗加工,代替最后的珩磨加工方式,但该加工方式反映的效果并不十分理想,刀具的调整时间长、耐用度低、制造成本高及出现工件表面粗糙度不稳定等质量问题。
(2)过程分析:考虑到CBN材料一般用于精加工的工艺特性,我们分别采用进口和国产CBN刀片,经过多次的试用,最终不但满足了生产加工的需要,而且在原有的基础上得到很大的提高。
(3)改善后现象描述:选用CBN刀片后,因刀片数量减少,刀具的调整时间缩短了50%以上;生产效率提高的同时,加工工件的表面粗糙度很稳定控制在Ra1.6以下,尤其在刀片进行国产化后,刀具的加工单台成本降低特别大,每台发动机缸体加工节约成本费用为22.5元/台。T6190刀具优化的相关参数和寿命如图2所示。
结语
高速高效切削、高质量是一个系统工程,受机床、刀具、被加工材料、冷却润滑和切削参数等多种因素影响。只有通过大量的试验和实践,充分采集数据,认真总结分析,不断摸索规律,将各种因素最佳组合,才能获得预期的加工效果,才能满足高质量、高效率和低成本的生产要求,提高企业市场竞争力。
评论 0
正在获取数据......