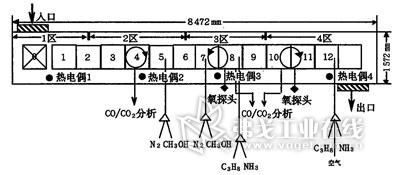
图1 连续推杆式热处理炉的平面布置
齿轮零件的表面热处理强化工艺在工业化生产中主要包括渗碳淬火、碳氮共渗和离子氮化等,本文主要介绍了对业内普遍采用的连续推杆式热处理炉在齿轮类零件的碳氮共渗淬火热处理生产中出现的表层晶间氧化严重、非马氏体组织超标问题的分析和解决方法。
连续推杆式热处理炉结合碳氮共渗淬火热处理工艺在齿轮类零件的工业化生产中应用广泛。由于化学热处理无法在宏观上直接分辨生产质量的好坏,需要借助金相分析等手段来验证,这就决定了我们在热处理工艺方法上需要先采用理论分析加试验的手段,然后再用金相检验来验证的方法去攻克生产中的质量难题。本文主要介绍了碳氮共渗淬火热处理生产中出现的表层晶间氧化严重的原因,以及试验分析方法。
碳氮共渗淬火的工艺及实现方法
碳氮共渗淬火是指在一定的温度下将C、N原子渗入零件表面的奥氏体,并向零件内部扩散,以渗碳为主,经过淬火后获得一定硬化层深的热处理工艺。
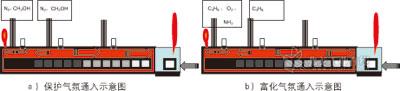
图2 炉内气体的循环方式
1. 连续推杆式热处理炉的构造
图1所示为连续推杆式热处理炉的构造简图,炉子分四个区,一区为加热区,二区、三区为渗碳区,四区为扩散和降温区。淬火油为分级淬火油,油温160℃。
温度控制采用炉顶单点热电偶控温,4个区单独控制温度,温度表采用PID调节的控温方式;渗碳气氛为还原性保护气氛,采用从二区、三区通入N2和CH3OH,N2和CH3OH裂解气氛的比例为2 : 8左右,N2采用膜分离制氮机生产,纯度大于99.5%。富化气氛为C3H8和NH3,三区、四区通入C3H8作为渗碳的富化气氛,在四区通入NH3作为渗氮的富化气氛。碳势控制采用两种计算方式进行比对和控制:
1.COC+ 1/2O2
使用在线气体分析仪测量CO的百分含量,使用氧探头测量O2的百分含量,并将读取当时的炉子温度T(℃)。将以上三个参数经过碳控表计算出炉子的实际显示碳势,然后和设定碳势比较,并通过PID的参数分别调节C3H8和空气管路进入炉子的气体量来实现碳势的控制。
2.COC+ CO2
使用在线气体分析仪测量CO的百分含量和CO2的百分含量,并读取当时的炉子温度T(℃)。将以上三个参数经过碳控表计算出炉子的实际显示碳势,然后和设定碳势比较,并通过PID的参数分别调节C3H8和空气管路进入炉子的气体量来实现碳势的控制。
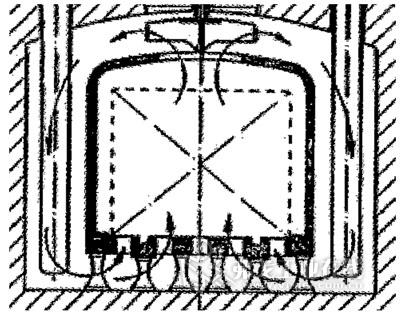
图3 保证整盘的零件吸碳均匀
由于氧探头反应速度灵敏且准确度高,在实际生产中一般采用第一种碳势控制方式来进行碳势控制,第二种计算方法用来和第一种计算方法进行比对。当两种计算方法差距超过设定范围就发出报警,提醒碳势控制异常,并且可以在氧探头损坏时,方便地切换到第二种控制方式保证生产的正常进行。
N2和CH3OH裂解气氛作为保护气氛可以将基础碳势调整到0.7~0.8,炉压调整到0.03~0.09MPa,这种气氛保护方式使炉子生产更安全,炉子发生故障后可以实现N2的自动吹扫,能够给排除故障提供更多的时间。
2. 炉内气体的循环方式
图2为炉内气体循环方式。在炉子每个区的顶部固定安装了一台风扇,对炉内的气氛进行搅拌,有利于气体和温度的均匀性。在炉子后部的两个区通入N2和CH3OH,CH3OH进入炉子内部后,在高温下分解成CO和H2,然后和N2一起构成了炉子内部整体的还原性吸热气氛,该气氛可以把基础碳势调整到0.70左右,然后通入C3H8和NH3作为富化气氛,在扩散和降温区通入空气作为碳势调节气氛。
从炉子后部通入的气体扩散到炉子前部,从废气排气口排出,炉子整体的气体流动趋势就是从后向前,部分废气经过淬火槽从后废气口排出。炉内的气体产生的压力比大气压力高0.03MPa以上,保证炉子相对外界的正压,防止空气进入产生爆炸危险。
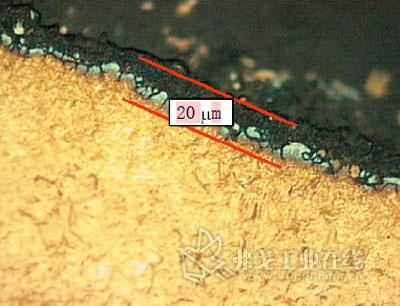
图4 500倍放大镜显示,表层的非马氏体厚度达到20umm以上
热处理碳氮共渗推盘炉的生产都是批量加工,每个托盘的零件在几十件到二百多件,整个托盘的零件叠放在一起同时进行碳氮共渗淬火,所以保证每盘热处理零件的热处理质量均匀性是工艺中的难点和重点。炉子的气氛循环上采用离心风扇和风道的设计,可以使炉子气氛从托盘底部向上的循环,保证每个零件在气氛接触上尽可能的均匀,从而保证整盘的零件吸碳均匀(见图4)。
零件表层晶间氧化的产生机理和工艺调整
1.晶间氧化现象
如图5所示,表层的非马氏体厚度达到20mm以上,晶间氧化的深度大于25mm,均超出了产品要求的范围,对产品的使用质量影响很大。齿轮表层的非马氏体硬度相对较低,而且有晶间的氧化层,这样齿轮零件表面在工作过程中容易产生剥落或发生打齿等现象。
2.晶界氧化托氏体层的产生机理
渗碳介质中的氧向钢中扩散,在晶界上形成Cr、Mn等元素的氧化物,致使该处的合金元素贫化、淬透性降低,在淬火时,冷却形成了片间距很小的片状珠光体——托氏体。
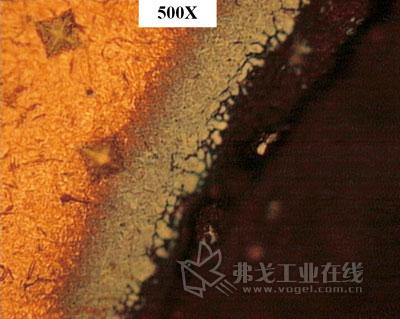
图5 500倍放大镜显示,托氏体层和氧化层仍然很厚
由于我们采用的渗碳介质有CH3OH,其醇裂解后的产物有CO和CO2,CO和CO2的化学反应在生成活性C原子的过程中必然产生O2,所以在类似的碳氮共渗淬火或者渗碳淬火的工业生产中不可避免地会产生零件表层很薄的氧化层,但是在工艺上采取措施可将氧化层控制在一个允许的范围内。
3.晶间氧化严重的工艺调整
对于晶间氧化严重,首先,我们怀疑可能是炉内气氛的含氧量偏高,导致的因素包括N2纯度低、碳势调节出现问题导致空气的加入量偏高。经过对制氮机的校对和N2纯度的检查,发现N2的纯度没有发生异常,在合格范围内。
然后,我们就把主要原因集中在碳势系统的调节问题上。碳势的调节主要通过控制仪表来实现,它的调节方式采用的是PID 的调节模式。当显示值超出设定值一定的比例时间后,就通入空气,以降低碳势;当显示值低于设定值一定的比例时间后,就通入C3H8以提高碳势。当PID参数未设定合适时,就可能产生空气频繁通入炉内的情况。通过观察空气流量计的通断频率来反应空气的通入量。经过PID参数的调整后,空气的通入频率已经很低,但是生产出来的零件经检验后发现,托氏体层和氧化层仍然很厚,如图5所示。
最后我们把原因分析的重点放到了炉子气氛的N2和CH3OH的裂解气体的配比上。CH3OH的裂解方程为:
CH3OH→ CO + 2H2
在已经成熟的热处理碳氮共渗工艺中,N2-CH3OH裂解气的配比一般可选择
4 : 6、3 : 7和2 : 8。理论上比例越小,CH3OH裂解气的含量越大,越有利于防止表面氧化。
出现表面氧化层深时,氮气和甲醇的进气工艺流量分别为:4m3/h,5L/h。每升CH3OH裂解为1.66Nm3的N2和CO。N2-CH3OH裂解气的比例约为1 : 2,N2的含量相对偏大,由于N2纯度为99.5%,这样炉内气体的氧含量就可能导致零件表面的晶间氧化严重。
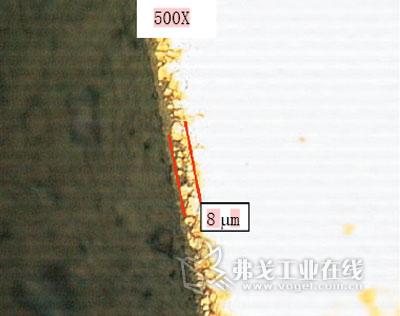
图6 500倍放大镜显示,非马氏体的厚度8umm
经过分析后,我们把CH3OH的工艺流量调整为8L/h,N2流量不变。N2-CH3OH裂解气的比例调整约为2 : 8。然后对生产的零件进行氧化层的金相检验,非马氏体的厚度8mm(见图6),氧化层的深度12mm,完全满足了产品的质量要求。
结语
在采用保护气氛的传统碳氮共渗淬火热处理的工艺应用中,表层的氧化是一个无法避免的缺陷。随着现代热处理设备和辅料技术的进步,对表层晶间氧化的问题有了很多的改进技术,如真空热处理渗碳淬火、等离子渗氮替代碳氮共渗或等离子深层深碳氮共渗等,使用球墨铸铁材料采用高频淬火的热处理工艺生产的机械零件替代渗碳淬火件,使用激光加热分段淬火等技术。为了提高产品质量,我们需要不断学习并积极采用新技术。
评论 0
没有更多评论了