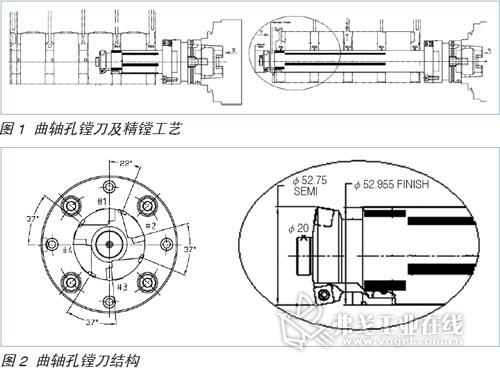
发动机缸体中的曲轴孔的加工质量对发动机的工作性能具有重要影响,如何保证曲轴孔的直径、圆度、位置度等参数满足产品的性能要求非常重要。本文介绍了曲轴孔精加工工艺的原理,并结合实际生产进一步探讨如何对铸铁发动机缸体曲轴孔的精加工工艺进行优化改善,使加工质量和效率得到有效提升。
缸体是发动机的重要基础件,其主要功用是使各机构、各系统组成一体,而发动机最主要的运动部件——曲轴、活塞和连杆,都与缸体有着非常密切的关系。
目前,我们常见的汽油发动机最高转速达6000r/min以上,曲轴在发动机缸体的曲轴孔中高速运转,这就对曲轴孔的直径、圆度和位置度提出了严格的工艺要求。
由于曲轴孔的加工质量对发动机的工作性能具有极大的影响,所以我们对发动机曲轴孔工艺的要求非常严格,包括直径、各档曲轴孔位置度、同轴度、圆度及表面粗糙度等。为了满足这些要求苛刻的工艺指标,精加工一般采用精镗、珩磨的加工工艺。对精镗工艺来讲,可在加工中心或专机上进行加工。但考虑到经济性和柔性化的加工需求和技术发展趋势,毫无疑问,加工中心比专机更有优势,因此,得到了越来越多的应用。不过加工中心也存在着曲轴孔位置度稳定性较专机略有差距的不足,并且还带来了一系列如直径、圆度不稳定的问题,因此,如何在加工中心的加工过程中,保证曲轴孔的各项参数满足产品的性能要求是我们重点研究的课题。
加工中心精镗加工刀具的选用
1. 曲轴孔精镗原理
加工中心精镗曲轴孔工艺的初期投入成本较低。因考虑到特殊的工艺要求,目前我们采用的精镗方案是两把精镗刀组合——第一把短精镗刀进行引导镗1、2档曲轴孔,第二把长精镗刀在1、2档曲轴孔的支撑下精镗剩余的各档曲轴孔(见图1)。由于曲轴孔各档之间需要保持较高的位置度和同轴度,所以精加工时必须在机床的同一个方向进刀加工。需要说明的是,若仅用一把长镗刀,在加工第1、2档曲轴孔会出现因缺少支撑而使得位置度不稳定的情况,必须选用短镗刀精加工完第1、2档曲轴孔后,再使用长镗刀在第1、2档曲轴孔的导向支撑下完成剩余曲轴孔的加工。
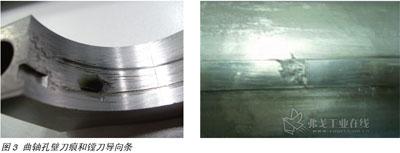
2. 曲轴孔精镗刀的刀体结构设计
采用上述加工工艺,所选用刀具的结构和材质也非常重要。目前,我公司采用国际知名刀具厂家Mapal公司提供的进口刀具,刀体上带4根导向条(见图2),刀体材质为硬质合金,装有4组半精镗刀片和4组精镗刀片。在加工过程中,先是半精镗刀片切削掉大部分余量,约0.3~0.4mm厚度的余量,随后是精镗刀片进行切削。对于加工余量,在我们的实际加工中,一般情况下,前者比后者低约0.2mm,也就是说,精镗刀片再加工掉剩余的0.2mm的余量。
3. 曲轴孔精镗工艺的加工参数设置
目前,业内精镗曲轴孔的镗刀一般采用硬质合金或CBN材质(含氮化硼)的刀片。我们采用的是硬质合金刀片,主要是基于刀片成本较低且加工寿命较长的考虑。我们目前所设定的刀具加工寿命通常为200件,转速为500r/min,进给量设定为5000mm/min,实践表明,能够满足大批量生产的要求。
4. 曲轴孔精镗加工过程中的问题分析
在曲轴孔的实际加工过程中,我们发现,曲轴孔精镗后的表面时不时地会出现严重的划伤发黑刀痕(见图3),导致珩磨余量不足。经过调查分析发现,导致这一现象的根本原因在于加工曲轴孔的镗刀刀体上的导向条破损严重,在高速运转过程中,刀体导向条失去了原有的支撑作用并与工件表面产生了碰撞挤压导致划伤工件,实际查看刀体的破坏情况也证明了这一点。
经分析,导向条易损坏产生划痕是因为导向条与曲轴孔壁间隙太小导致。理论上,曲轴孔加工后的直径尺寸为(52.955±0.015)mm,而导向条的直径为52.939~52.944 mm,无倒锥,随着刀片的磨损曲轴孔径变小,导向条与曲轴孔壁的间隙越来越小,直至产生挤压,最终就会使导向条损坏(见图4),导向条损坏便失去了原有的导向作用而导致镗刀加工时跳动变大,位置度、圆度等参数也无法得到有效保证,严重影响加工质量。
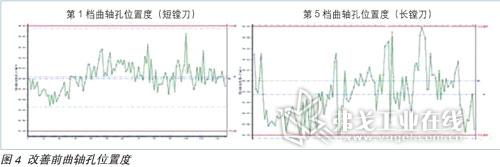
5. 曲轴孔精镗刀调整前后效果对比
经过实验,我们将导向条的最大直径做成低于加工要求尺寸下偏差5 mm,直径设置范围52.930~52.935mm,倒锥
8~10mm。调整之后进行加工发现,刀片使用寿命得到了较大的提升,加工寿命的前后变化如表所示。调整后曲轴孔的圆度和位置度都在合格范围内,并且当曲轴孔加工直径趋于下偏差52.940mm时,导向条也没有出现因摩擦造成的发亮和擦伤现象,工件表面也没有出现划伤和发黑的情况,对加工质量没有任何影响,同时还大大降低了制造成本,说明我们的调整方案是比较合理有效的。
加工中心精镗刀的跳动控制
1. 曲轴孔位置度数据收集
离加工中心主轴最近的第1档与最远的第5档的曲轴孔的加工分别是由短镗刀和长镗刀完成的,日常生产抽检频次为1/100。经日常数据统计,曲轴孔的位置度波动较大,且第5档(长镗刀加工)明显比第1档(短镗刀加工)在上下方向上尺寸波动大(见图4),这与长、短镗刀重心不同有很大关系。
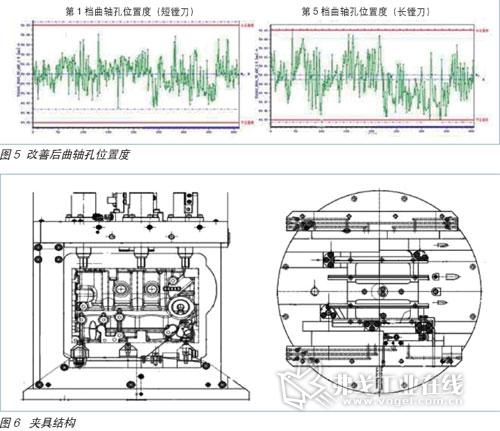
2. 曲轴孔镗刀跳动值分析及效果
由于加工第3、4和5档曲轴孔的长镗刀长度达到412.5mm,直径约52mm,刀具非常重,刀具重心离主轴刀夹约200mm,而1~5档曲轴孔位置度要求是φ0.1mm。在这种情况下,对如何控制好刀具在主轴上的跳动提出了严峻的挑战。
通过检查刀具跳动值,我们发现,短镗刀的跳动明显好于长镗刀,短镗刀和长镗刀跳动最大值分别达到5mm和15mm。由于短镗刀加工出来的第1、2档曲轴孔对长镗刀加工后续3档曲轴孔起到了一定的支撑导向作用,因此,短镗刀的跳动同样至关重要。目前,对于每台加工中心,我们都采用固定地使用长、短镗刀各两把的方式,并且定期对其进行刀具跳动检测。经调整,在曲轴孔的实际加工中,测量数据表明,长、短镗刀跳动值均控制在3 mm以下。曲轴孔的位置度稳定性较之前有明显的改善(见图5)。
加工中心精镗加工装夹方式分析
1. 装夹原理
曲轴孔加工采用卧式加工的方式,一个平面两个定位销进行定位,并靠顶部三个液压缸直杆进行工件夹紧(见图6)。在日常加工中,曲轴孔的位置度往往会受夹具定位块或定位销等的影响而发生变化。
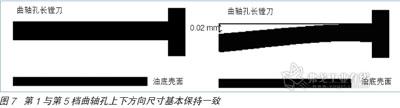
2. 夹具装夹原理及问题分析
缸体油底壳面落在三个定位块上并靠两个销孔定位在两个定位销上,其中一个为圆销,另一个为菱形销。理论上,当三个定位块在一个理想的水平面上时,加工曲轴孔的长镗刀与油底壳面保持平行,但由于长镗刀的自重问题,刀头会向下产生微观偏离(肉眼无法观测),导致上、下方向上短刀加工出来的第1档曲轴孔处于水平方向,长镗刀加工出来的第5档曲轴孔则在水平方向以下,约0.01~0.02 mm的尺寸距离。此时,可通过调整三个定位块的高度,将靠近第1档曲轴孔的夹具定位块调高0.01~
0.02 mm的距离,这样实际加工出来的第1与第5档曲轴孔上下方向尺寸会基本上保持一致(见图7)。
实际使用的过程中,由于定位销与孔壁的接触面积不同,菱形销要比圆销更容易发生磨损,而且由于国内目前使用的原材料无论在硬度和刚性上都比国外的差一些,因此,定位销的使用寿命还比较低。当菱形销产生磨损后,首先表现出来的加工结果是第1档曲轴孔在水平方向上产生偏离,导致的结果是第1档曲轴孔的位置度稳定性变得非常差。

3. 夹具维护
为保持实际加工的稳定性,夹具的预防性维修检查非常重要,定期维护能够提前做到预防超差问题的出现,而不是等每次测量发现尺寸超差后才去调查原因、检查夹具。
结论
发动机缸体曲轴孔的加工质量对发动机工作性能影响很大,为保证曲轴孔的直径、圆度及位置度等参数达到产品性能要求,我们采用的是能够满足柔性化加工需求的加工中心精镗曲轴孔的工艺方案,并且是两把精镗刀组合——第一把短精镗刀进行引导镗1、2档曲轴孔,第二把长精镗刀在1、2档曲轴孔的支撑下精镗剩余的各档曲轴孔。此外,加工曲轴孔的长、短镗刀导向条的保养及检查跳动工作也必不可少,同时,夹具维护也须定期进行,以更好地保障和提升加工质量。只要各项工作做到位,缸体曲轴孔的各项参数才能保持稳定,使得缸体的加工质量和效率在加工中心得到有效提升。
评论 0
正在获取数据......