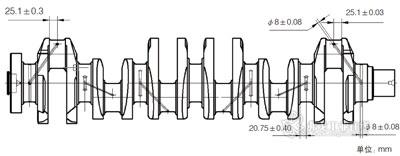
图1 曲轴油孔加工工艺
传统的曲轴油孔加工工艺一般采用摇臂钻配专用工装钻模的方式进行加工,工人劳动强度大、生产效率低下,成为曲轴加工企业的生产瓶颈。沈阳机床成套设备有限责任公司的SUC8119、SUC8149系列曲轴油孔加工数控机床的研制成功,很好地解决了这些问题。
汽车发动机曲轴油孔加工属于深孔加工,其中斜油孔加工的深度一般为直径的20~30倍。传统的曲轴油孔加工工艺一般采用摇臂钻配专用工装钻模的方式,工人劳动强度大、生产效率低下,成为曲轴加工企业的生产瓶颈,需要投入大量的设备和人力来弥补。沈阳机床成套设备有限责任公司的SUC8119、SUC8149系列曲轴油孔加工数控机床的研制成功,很好地解决了这一瓶颈问题。其中SUC8119系列采用枪钻工艺完成曲轴的油孔加工,具有加工的油孔直线度和表面粗糙度好、无毛刺等特点。
同时由于该机床具有很好的柔性,可以满足大部分四缸和六缸汽车发动机曲轴的油孔加工,大量节省了曲轴生产企业的设备、人力和工装等投入,并为其创造了可观的经济效益。本文对能够很好满足各种曲轴油孔加工的枪钻钻模系统进行了介绍。
工艺方案分析
如图1所示,曲轴油孔的加工均是在曲轴的主轴颈和连杆颈的外圆表面上,因此油孔的加工只能是通过先加工引导孔或钻模导向直接加工完成。若采用先加工引导孔的方式,则属于多刀切削,这样将会增加机床的成本。因此,目前国际上采用枪钻加工曲轴油孔的数控机床大多采用钻模导向的方式。由于曲轴的主轴颈和连杆颈的直径以及直斜油孔角度均有差异,因此采用枪钻加工曲轴不同部位和形式的油孔时需要与之对应的钻模为导向进行加工,正是基于这种工艺方案的研究与分析开发了具有四工位自动切换的高精度枪钻钻模导向系统。
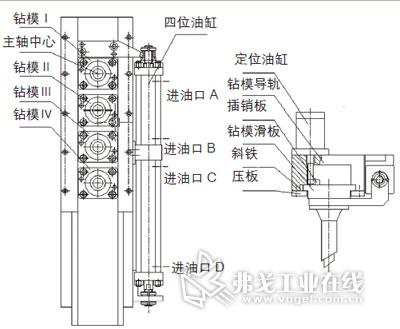
图2 曲轴油孔枪钻钻模系统结构
钻模系统结构
该钻模导向系统结构如图2所示,主要由四位油缸、钻模滑板、定位机构以及钻模四部分组成。四位油缸是该钻模导向系统自动切换的驱动部分,该油缸采用两个油缸背对背串联的形式,其中下油缸的行程为上油缸的2倍。上、下两个油缸有4个进油口,分别为进油口A、B和C、D。四位油缸下端的活塞杆为固定形式,上端的活塞杆与钻模滑板相连。在钻模滑板上安装有4个用于加工时为枪钻导向的钻模Ⅰ、Ⅱ、Ⅲ和Ⅳ。钻模滑板通过压板和斜铁安装在钻模导轨上,在钻模滑板和钻模导轨的背面分别安装有插销板和定位油缸。该钻模系统的自动切换动作详见图3:当A、D口同时进油时,上、下油缸活塞杆均缩回,钻模Ⅰ切换到主轴中心的位置;B、D口同时进油时,上油缸活塞杆伸出,下油缸活塞杆缩回,钻模Ⅱ切换到主轴中心的位置;A、C口同时进油时,上油缸活塞杆缩回,下油缸活塞杆伸出,钻模Ⅲ切换到主轴中心的位置;B、C口同时进油时,上、下油缸活塞杆均伸出,钻模Ⅳ切换到主轴中心的位置。当各钻模切换到加工需要位置时,定位油缸的活塞杆伸出,插入插销板的定位槽中,实现钻模与刀具主轴同轴的精确定位。当钻模完成切换和定位后,机床便可以进行切削加工。
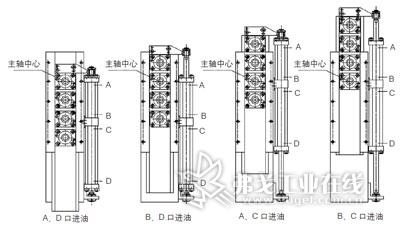
图3 四位油缸工作示意
结语
由于该钻模导向系统在设计之初对于曲轴油孔加工的工艺特点、枪钻的加工要求以及具体的结构方案设计进行了充分的研究和考虑,因此该钻模系统在实际使用过程中具有很好的柔性、可靠性以及使用精度,为曲轴油孔枪钻加工数控机床的开发提供了成功基础,也为实现液压驱动的多点精确定位积累了技术经验。
评论
加载更多