发动机生产线的规划设计是工厂设计的重要环节之一,是工艺投资成败的关键。本文以道依茨一汽(大连)柴油机有限公司二工厂缸体线为例,对发动机生产线的工艺规划、设备选型及组线方案等进行了全面分析。
道依茨一汽(大连)柴油机有限公司二工厂发动机生产线系全线引进德国道依茨公司BF1013和BF2012系列4/6缸发动机技术建设而成,极具前瞻性的设计赋予了工厂高度的灵活性。本文以该工厂缸体生产线为例,对柴油发动机生产线的工艺规划、生产方式、设备选型及组线方案等进行了全面分析。
规划工艺分析,选择生产方式
发动机箱体类零件加工的发展方向是高精、高效和高柔性。在设备选型确定之前,需要根据产品特点进行工艺分析。工艺规划不仅需依据生产纲领选择刚性生产线或柔性生产线,还需考虑很多其他因素,如产品特点、质量要求和发展规划,工艺安排、生产线布局(包括占地面积)、维护成本及被改造的方便性,企业工艺技术水平和对生产线总体技术要求等。
刚性生产线由专机及专机自动线组成,设备布局基本采用串联形式。柔性生产线由加工中心(或三坐标加工单元)组成,或由加工中心+部分专机及自动线组成,设备通常采用平行(并行)或平行和串联结合的方式,也可单独采用串联形式布局。
平行加工是同一工序采用多台加工中心,其特点是:单台加工中心出现故障或调试时,不会影响整条生产线的工作;根据市场销量需求,方便增加单台设备,适合生产线分期投入,经济性好;但同一工序有多台加工中心,零件追溯系统较串联加工复杂。图1所示平行加工布置中的OP30工件采用了3台加工中心,“Future”是指未来产量扩大时需增加的加工中心。
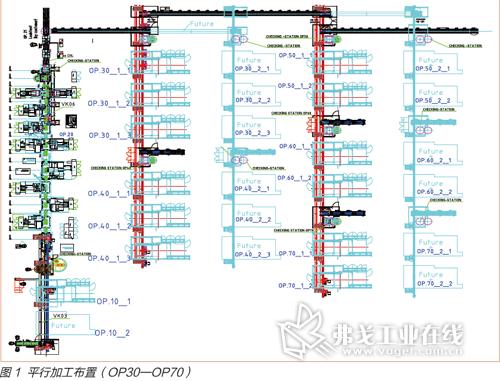
串联加工生产方式的特点是:单台设备出现故障或调试时,会影响部分工序的正常生产;因生产节拍长,加工中心利用率高;生产线工件流向简单,零件追溯系统简单。串联加工布局如图2所示。
通过对BF1013和BF2012系列发动机缸体的工艺分析,并考虑到公司年产10万台分布实施生产纲领规划要求以及后续产品规划发展要求,我们决定采用加工中心和部分专机相结合的柔性生产系统。因为BF1013和BF2012是两个完全不同平台的产品,且缸体加工工艺较其他机型复杂,如果采用刚性生产系统,无论是投资还是占地面积都将较大。
合理规划生产方式可以进一步提高生产系统的使用价值,提高生产效率,令生产工艺流程更加合理化,为企业节约投资成本和使用成本。柔性生产方式充分体现了高效和柔性的统一。缸体关键部位缸孔、主轴孔粗加工和精加工采用专机及专机自动线,各面一般孔加工采用加工中心;毛坯上线和成品下线采用定向吊,人工操作;专机自动线上下料和加工中心上下料采用桁架机械手;工序间工件输送采用机动辊道,实现自动化生产,提高生产效率。
该缸体生产线具有诸多优点:
1.充分发挥了加工中心柔性、工序集中的特点。缸体6个面上的孔较多,又是多品种在线生产,在生产节拍、机床刀库数量允许的条件下,不受孔距限制,可按最佳工艺进行加工。
2.通过加工中心的B轴和A轴,实现同一夹具缸体的多面加工,减少夹具数量和夹具费用。
3.产品变更时,生产线改造方便快捷。
4.在缸体主轴孔、缸孔粗加工和精加工中,充分发挥了专机高精、高效的特点。
生产线布局及设备选型
设备选型及投资和生产线布局以及产品加工质量紧密相关。柔性生产线上的加工中心通常采用高速加工中心,其特点是:高转速、高进给(含主轴快速移动速度)、高加(减)速度、微米级的加工精度、高的静(动)态刚度以及轻量化的移动部件。
在确定缸体线设备类型时,我们对欧美设备、日韩设备和国产设备进行了性价比的综合分析,日韩和国产加工中心整体技术水平较欧美低,在同一生产节拍条件下,需要的设备数量多,占地面积大。最终,我们确定了缸体线加工设备以欧美为主,线内辅助设备(清洗机、密封试验机和装配机)以国产为主的基本原则;缸体生产线年产10万台一次规划,分步实施;专机及专机自动线一次规划到位;加工中心分两步实施,一次规划5万台。
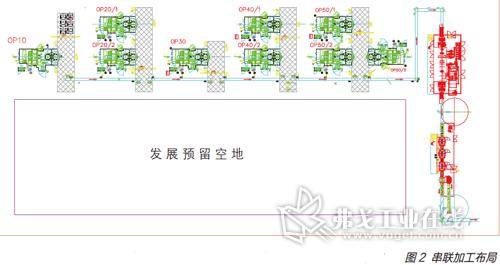
1.生产线布局
缸体线专机及专机自动线采用串联方式,加工中心采用平行(串联和并行相结合)布局。
基本工艺安排:毛坯上线—基准加工—粗加工—清洗—密封试验—各面孔加工—清洗—安装主轴承盖—三轴孔加工—缸孔单体泵孔挺柱孔加工—自动去毛刺—清洗—安装油泵拉杆支架、缸套、堵盖、钢球及螺堵—密封试验—成品检查—下线。
2.刀具选择
高速切削加工与常规的切削加工相比具有如下优点:生产效率提高3~10倍;切削力降低30%以上,尤其是径向切削分力大幅度减少,有利于提高薄壁件、细长件等刚性差的零件的加工精度;切削热95%被切屑带走,适合加工容易热变形的零件;高速切削时,机床的激振频率远离工艺系统的固有频率,工作平稳,振动较小,适合加工精密零件。
在目前机床所能达到的高速范围内,速度越高,刀具的磨损越快。因此,高速切削对刀具材料提出了更高的要求,除了具备普通刀具材料的一些基本性能之外,还要求高速切削刀具具备高的耐热性、抗热冲击性、良好的高温力学性能及高可靠性。
在缸体加工工艺设计中,我们大量采用高速加工技术,在缸体线的平面铣削和精镗孔中广泛采用陶瓷和CBN刀具,在孔加工中使用硬质合金涂层刀具和PCD刀具。缸体平面铣削陶瓷刀具切削速度达到1000m/min;镗缸孔CBN刀具线速度600m/min;孔加工线速度达到120~150m/min。另外,为提高生产效率,我们还采用大量复合刀具,如钻镗复合、钻铰复合。
3.冷却排屑方式
缸体采用合金铸铁类材料,加工采用湿式加工。传统的缸体、缸盖生产线冷却系统都采用空中供液、地沟排屑方式,厂房污染较严重,并且地沟排屑维护工作量较大。为此,我们在缸体线上采用了上供上排冷却系统,切削液和铁屑通过空中管道输送,系统运行安全可靠,对厂房无污染。
4.在线检测
为保证产品质量水平的符合性和一致性,在缸体生产线工序安排时需要考虑工序间零件加工精度检测工位的设置。每个加工工序结束后,都设置一个检测工位,配备气动或电子量仪、线性检具以及检测台,对本工序加工内容进行抽检。对缸体主轴孔、凸轮轴孔和前后端面定位安装孔,设置在线自动检测工位;对缸孔和缸孔止口加工,设置自动测量和自动补偿工位。另外,为对生产过程实施有效控制和监控,在关键工序还设置了SPC统计分析。
5.生产线物流
在生产线布局时应考量三项内容:物(原材料、零件和在制品等)的物流距离短;人(操作者)的动作/作业应顺畅;物品的放置方法/置放方式应容易了解。另外,还需考虑消防通道和维修通道。
6.辅助设备规划
从保证产品质量、提高生产效率和降低劳动强度等方面,着手对缸体线辅助设备进行规划。
(1)缸体中间密封试验机 根据国产毛坯质量状况,在缸体粗加工后设置密封试验机,对缸体主油道和燃油道进行密封检验;
(2)缸体中间清洗机1 为保证缸体中间密封试验机工作可靠性,在密封试验机之前对工件进行清洗;
(3)缸体中间清洗机2 在缸体主轴承盖装配之前,对缸体进行清洗;
(4)缸体主轴承盖装配机 采用双轴自动拧紧机,按转角法自动拧紧主轴承盖螺栓;
(5)自动去毛刺机 去除缸体表面、三轴孔等毛刺;
(6)缸体最终清洗机 主油道清洗采用高压清洗技术,有效去除加工毛刺;
(7)缸体油泵拉杆支架、缸套、堵盖、钢球、螺堵装配机;
(8)缸体最终密封试验机 对缸体水套、油道、钢球装配进行气密检查。
结语
发动机生产线的规划是一项系统工程,设计建设具有适度的前瞻性和良好技术经济性的发动机生产线,需要综合考虑很多因素,如:生产线布局,设备选型、生产方式及工艺安排,投资分析,生产线检测要求,生产线物流,生产线是否能够满足发展需要。
我公司二工厂缸体线已投产运行6年了,生产线系统稳定性和缸体加工质量均达到规划要求,产品能够满足欧III、欧IV排放法规要求。
评论 0
正在获取数据......