本文论述了曲轴、连杆间隙存在的重要性,以及对其间隙测量的必要性。通过剖析目前常见的两种曲轴、连杆间隙测量方式,针对性地构思出一款具备较高柔性度的曲轴、连杆间隙测量设备。该设备可以有效提升试装过程中针对曲轴、连杆的间隙测量精度,保证发动机的装配质量和装配速度。
发动机的曲轴和连杆具备一定的间隙是其正常运转的必要条件,因为曲轴在工作时,会因为温度的上升而发生膨胀,有一定的轴向移动,预留的间隙是为保证其膨胀后仍能正常运转。但该间隙又不能预留过大,如果预留间隙过大,在发动机工作时,曲轴和连杆会产生不正常的轴向窜动,导致活塞偏缸、连杆弯曲等故障发生。所以在发动机装配过程中,曲轴、连杆的装配间隙作为装配过程中的一项重要指标,要受到严格的监控。无论是手动装配或者是流水线生产,都会采取必要的措施对曲轴、连杆间隙进行测量,对间隙不合格的产品进行故障排除,确保间隙合格后才可继续进行下一步的生产。
在大多数汽车生产企业中,间隙测量设备一般仅在流水生产线中使用。对于发动机研发和试装过程中的曲轴、连杆间隙测量,则仅依靠塞尺等原始工具进行手工测量,测试精度往往无法满足试验机型的需求,导致问题发动机无法被正确测量,从而影响相关的试验数据,并导致试验失败。
针对此项情况,本文首先从曲轴、连杆的测量必要性入手进行分析,根据常见的流水线测量设备,提出了相应的试装过程测量设备的设计思路和设计方案。
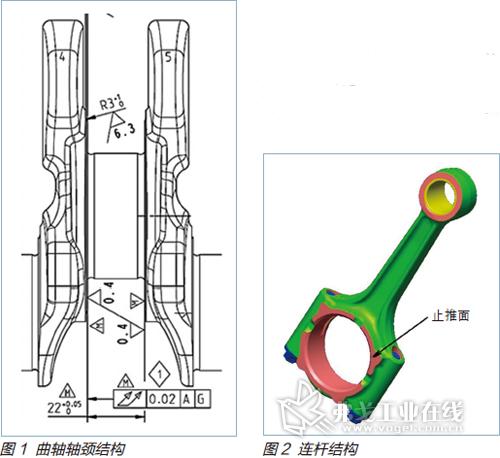
曲轴、连杆间隙分析
在常见的发动机结构中,曲轴的轴向间隙和连杆的轴向间隙是通过不同的方式来实现的。其中,曲轴的轴向间隙控制一般是通过在曲轴的前部、中部或者后部安装止推轴承来实现的,也有采用独立的止推片实现对曲轴的限位。目前大部分的汽油发动机中,均是采用止推垫片的限位形式实现。止推垫片又分为整体式和分体式。整体式是与曲轴轴瓦结合为一体,安装较为方便;也有单独止推片结构的,安装较整体式的略有复杂,但是可以通过安装不同厚度的止推片,实现对曲轴轴向间隙的微调,在发动机的研发试制过程中,优点较为明显。一般的曲轴轴向窜动间隙在0.10~0.30mm之间。
由图1可以得知,在一般的曲轴加工时,起止推作用的轴颈面尺寸会相应加大,从而起到分散作用力的功能,延长曲轴的寿命。而连杆间隙因需要与曲轴配合进行,且连杆曲轴的接触面较小,在近几年设计的汽油发动机结构中,一般不采用安装止推片或者止推轴承的方式,而是直接通过连杆和曲轴本身的接触而实现。如图2、图3所示,连杆侧面和曲轴侧面都已经进行过精度较高的加工,可以有效地保证连杆、曲轴的相对间隙。
在图2中,连杆大头止推面上有3个缺口,其主要作用是方便润滑油的流动,保证连杆与曲轴结合面的润滑良好。
常见曲轴、连杆间隙测量
对于曲轴、连杆轴向间隙的检测方式,分为手动和自动两类。其中自动检测设备大多运用在自动化的发动机装配生产线中,可以有效地同步检测曲轴、连杆的轴向间隙以及曲轴回转力矩等数据,测量结果直观可见,并依据测量结果进行合格判定,不合格产品将自动进入返修线由工人进行人工返修。一般的生产线设备已经将曲轴回转力矩测量和曲轴、连杆间隙测量整合到一起,可进行同步测量。目前国内已经有厂家可生产该类型设备,如图6所示,其测量精度已经达到或者超过国外同类产品水准。
手动检测方式一般是通过手或工具移动曲轴或连杆,通过塞尺或者百分表等量具对曲轴、连杆的移动距离进行测量。其中,塞尺多用于测量连杆的间隙,而百分表常用于测量曲轴的轴向间隙。由于手工施加的力道不均匀或施加的力道方向偏差,以及测量工具本身的精度过低,这种测量方式一般精度不高,多适用于无法采用自动化生产的场所,比如研发试制、试装机构,或者机种更换较为频繁,需要极高柔性的发动机生产线等场合。
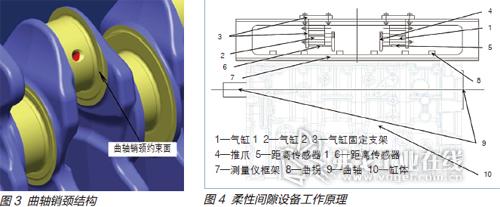
新式柔性间隙测量装置
某研发机构目前采用手动测量方式对曲轴、连杆间隙进行测量,测量过程繁琐、精度较低,且受制于员工的个人专业素质,经常出现同一台发动机测量结果不一致的现象。为解决这个问题,参考目前试制车间的工作方式,我们有针对性地设计了一款具有较高柔性、可适用于绝大多数发动机曲轴间隙测量的设备。
该设备主要有设备支架、测量头、控制回路及数据显示机构构成,其中,设备之间采用铝合金结构,可有效减轻重量,降低员工的劳动强度。测量头采用气缸驱动方式,将高精度距离传感器与气缸进行刚性连接固定,由空气驱动气缸带动曲轴、连杆进行移动,避免了因为手动方式而出现的测量不一致性。高精度测量头的测量精度在0.001mm左右,可以完全满足曲轴连杆间隙的测量需求,同时,可将测量结果以数字的形式直接显示在数据显示屏上,直观明了,方便员工对测量结果进行管控。
由于设备的结构简单,控制回路也相应较为简单,只有一套气动控制系统,视采购成本的不同,可以分别设计为手动控制回路或自动控制回路。
1.工作原理
如图4所示,将设备通过定位销固定在缸体的下表面以后,调节3气缸固定支架上的螺栓,使气缸1和气缸2的位置刚好位于曲轴的几个曲拐处,使得4推爪和曲拐的间距保持在5mm左右即可,推爪的高度以低于曲拐最上缘10mm左右为宜。调整完成后,打开设备的电源和气源,准备测量。
2.测量动作
(1)气缸1通气,推爪前移,推动曲轴整体向左移动至极限位置;然后气缸2通气,气缸1接通大气,气缸2推爪推动曲轴向右移动至极限位置;将以上两个动作自动循环3~5次,以确保曲轴可正常移动。
(2)气缸1通气,推爪前移,推动曲轴整体向左移动至极限位置,距离传感器1启动,记录目前位置为零点(一);然后气缸2通气,气缸1接通大气,气缸2推爪推动曲轴向右移动至极限位置,距离传感器1记录后退距离,距离传感器2启动,记录目前位置为零点(二);然后循环上述动作两个动作10次以上,记录移动数据各20次,其中后退数据10次,前进数据10次。
将传感器1的数据与传感器2的数据进行比较,剔除波动较大的数值,对剩余数值进行分析,即可得出曲轴或连杆的活动间隙。
结语
曲轴和连杆间隙作为必须存在的一种要素,在发动机制造和装配过程中具有非常重要的地位,目前国内的各大汽车生产厂家均已具备高精度的测量能力。而因为大部分合资汽车厂商在国内并没有相应的研发机构,故适用于研发机构的间隙自动测量设备目前还没有合适的相关产品。在研发过程中,曲轴和连杆间隙又需要得到较为精确的测量和判定才能保证发动机的设计性能得到实现,所以,后续有关间隙测量的设备仍需要投入较大的经费进行研发才能满足要求。
评论 0
正在获取数据......