发动机的缸盖和机体在产品完成设计后通常都要先经过试制验证,再投入批量生产。本文就某汽油发动机缸盖和机体的试制进行了探讨,取得了很好的经济效益。
我公司某款发动机为小型高性能四缸汽油发动机,缸盖为铸造铝合金材质,机体为灰铸铁材质。此发动机的开发基于我公司某一发动机平台,尺寸与某在产发动机相当,但结构有较大差别。该在产发动机试制后遗留下大量的试制工装,大部分处于闲置状态,为了避免浪费同时最大限度地降低新产品试制的投资,我们决定尽量采用现在装备,制定出一套精益化的试制加工方案。
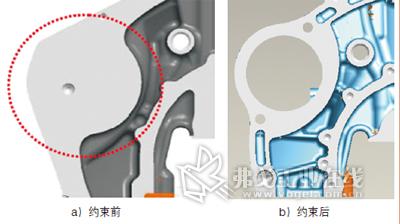
机体一处结构工艺性约束前后对比
精益化手段
为了实现缸盖和机体样件的精益化试制加工,我们对试制过程进行了全方位的分析,采取了一系列的精益化手段。
1.在产品设计阶段提出工艺性约束条件,使产品的工艺性得到有效保证,进而降低试制成本。
产品工艺性的优劣直接影响产品的制造成本,为此在产品设计阶段工艺人员便开始介入,针对概念模型、设计数模等与产品设计人员进行沟通,并提出了工艺性约束条件,这样在不影响产品性能的前提下产品的工艺性得到了保证,同时也避免了后期产品出现大的设计变更导致的变更费用。
我们从毛坯的铸造工艺性、加工工艺性等各方面来开展工作,讨论确定了毛坯铸造分模、结构壁厚、加工基准、加工余量和夹紧点等,共提出工艺性约束条件百余项,促使产品的工艺性达到最优化。机体一处结构工艺性约束前后对比如图所示。
2.充分挖掘闲置试制工装价值,变“废”为“宝”。
此款发动机和我公司某在产发动机在尺寸上较为接近,因此试制工装的尺寸也较为接近。如何利用闲置工装,是我们实现精益化投资需要思考的一个问题。
夹具方面,我们主要采取了以下两种方式对闲置工装进行利用,即:整体利用,改造零部件;整体拆分,利用零部件。对于手动夹具,我们采取了在夹具底板上重新布置或者更换定位夹紧元件的方式;而对于含有内部油路的液压夹具,我们则将其拆分,利用其液压缸、油管和压板等元器件。最终,我们共改造了7副夹具,拆分了2副夹具,利用其中的液压元器件。
此外,我们还与刀具供应商展开合作,对闲置的刀具进行梳理,整理出可利用的刀具以及可利用的刀柄等附件清单,共利用现有刀具20多支、刀柄60多支,充分发掘了闲置刀具的潜在价值。
3. 全方位开展标准化工作,最大限度减少非标设计和非标件。
非标设计和非标件往往周期长、成本高,与精益投资相违悖。为此,我们从产品设计入手,对产品的特性进行标准化审查,如安装孔配合公差、螺纹种类等;工装尽可能采购标准刀具、标准检具,调试加工过程中,使用标准刀具配合合理的编程路径来实现非标刀具的功能等。
4.集众家之所长,开展精益化采购。
在新购刀具方面,我们也采取了一些和以往不同的做法。例如,放弃以往的刀具外包,依据各刀具供应商不同刀具品类的性价比差异对刀具进行分类采购,使各子类刀具分别由性价比最高的供应商来进行供应,降低了总体投资。通过这项措施我们比以往节省了约5%的投资。
结语
通过采取以上各项措施,我们成功制定出一套精益化的试制加工方案,试制总投资比以往节约了20%以上。该精益化试制加工方案让公司的闲置资产得以重复利用,杜绝了浪费,实现了较好的经济效益。
评论 0
正在获取数据......