某2.0L汽油发动机曲轴在400h全速全负荷耐久试验过程中发生断裂,为查找其具体断裂原因,对曲轴进行仿真模拟分析,研究表明,曲轴各主轴颈及连杆轴颈的安全因数及材料成份均满足要求,曲轴的滚压圆角存在的尖角缺陷是此次曲轴断裂的直接原因。
曲轴作为发动机关键零部件之一,其耐久可靠性对发动机的工作性能及使用寿命具有决定性的影响。影响曲轴耐久可靠性的主要因素为曲轴受到的扭转疲劳应力和弯曲轴疲劳应力。曲轴的疲劳强度通过疲劳安全因数来表示,在有限元分析中,由于网格和载荷的因素,一般要求曲轴疲劳安全因数应大于1.1。
对于汽油机而言,曲轴安全因数经验值一般大于1.2。
某2.0L汽油发动机在进行400h全速全负荷耐久试验过程中,发生曲轴断裂。曲轴材料采用QT800-2,断裂位置如图1所示,发生在第8曲柄臂、连杆轴颈过渡圆角处。
针对此问题,本文首先通过使用Excite-PU为计算平台,结合AVL软件ShaftModeler和AutoShaft模块,校核曲轴的疲劳安全因数;然后从曲轴材料、曲轴圆角工艺状态校核曲轴的工作性能,最终判断出曲轴断裂的真正原因。
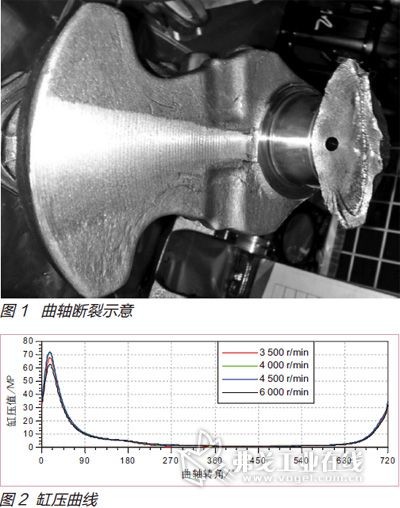
曲轴断裂模式
根据曲轴所受到的扭转疲劳应力和弯曲疲劳应力,曲轴断裂模式主要分为扭转疲劳断裂和弯曲疲劳断裂。而曲轴轴系通过曲轴皮带轮的减振,扭转应力一般都小于曲轴的扭转疲劳强度,曲轴很少因为扭转疲劳强度不足而断裂。曲轴断裂的分析统计表明,80%的曲轴疲劳破坏由弯曲疲劳强度不足导致,而曲轴弯曲应力产生的破坏主要表现在曲轴的轴颈圆角部位断裂,因为曲轴的应力集中出现在连杆颈下侧与主轴颈上侧过渡圆角处,实际这些部位也较容易出现疲劳失效。
某汽油发动机在全速全负荷试验过程中发生曲轴断裂,断裂部位发生在曲轴第8曲柄臂与连杆轴颈过渡圆角处。断裂裂纹呈波纹状。该曲轴断裂形式属于典型曲轴圆角处的弯曲疲劳断裂。
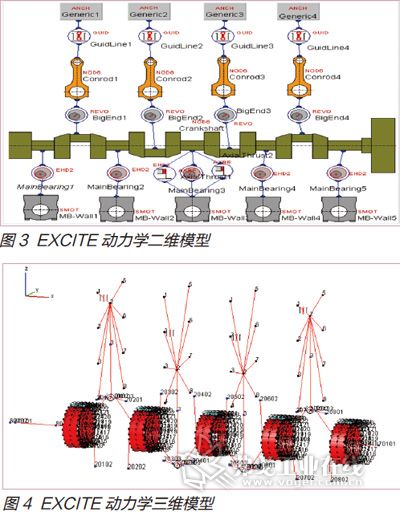
曲轴动力学仿真分析
由于此次曲轴断裂为典型的曲轴圆角处的弯曲轴疲劳断裂,因此首先对曲轴断裂进行曲轴动力学仿真分析,校核曲轴设计安全因数是否满足要求。
计算中所采用的缸压曲线如图2 所示,考虑到发动机爆振的影响,各缸爆压曲线放大因数取1.1。
通过Excite Power Unit平台建立曲轴系动力学模型,如图3、4所示。输入发动机主要结构参数与各转速全负荷缸压曲线,由软件自动生成作用于曲轴系各质量段(曲柄销、主轴颈等)的受力情况。使用AVL 软件ShaftModeler和AutoShaft模块,以3D CAD模型数据(STL 格式)为基础,分割曲轴系各质量段,生成曲轴等效模型,计算得出各质量段对旋转轴线的质量惯量与刚度,如图5所示。
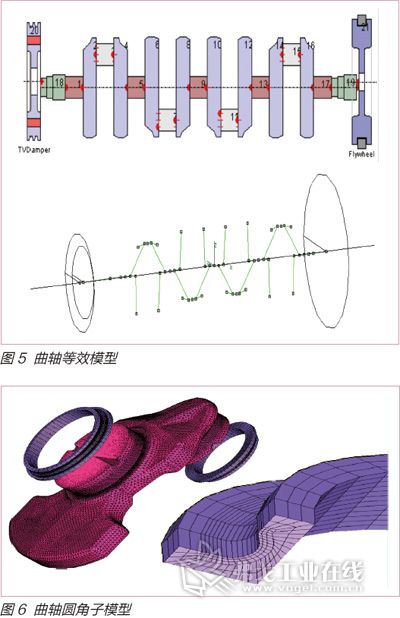
曲轴所受的载荷是循环载荷,其破坏一般由疲劳失效造成,因此要对曲轴进行疲劳计算。首先对前面确定的最危险圆角所在曲柄臂(见图6)加载12个自由度方向的单位载荷并进行有限元计算,然后提取相应转速下的载荷,曲轴疲劳计算的流程如图7所示,使用NSOFT软件计算疲劳强度,从而计算曲轴各连杆轴颈及主轴颈的安全因数。
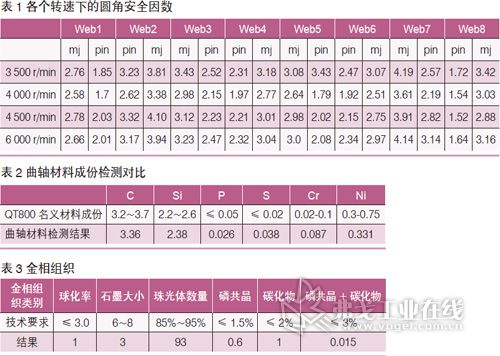
本文分别提取了转速分别为3500r/min、4000r/min、4500r/min和6000r/min的圆角边界条件,计算各个圆角的最小安全因数,具体如表1所示。
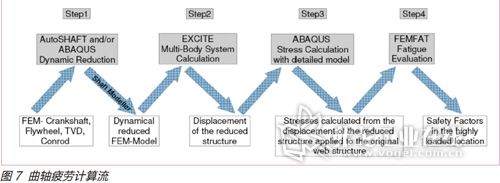
图8显示的是转速4500r/min时的Web8曲柄销圆角、主轴颈圆角的最小安全因数,在计算转速的圆角安全因数时,转速4500r/min时、第八曲柄臂、曲柄销圆角的最小安全因数最小,为1.52。
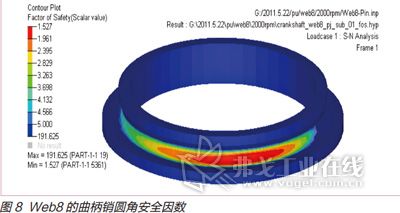
结果分析
对于汽油发动机,曲轴最小安全因数为1.2,从上面动力学分析得到,曲轴各个圆角处安全因数均大于1.2,满足要求。因此分别对曲轴材料成份及曲轴圆角工艺进行分析。
首先对材料进行检测分析,得到材料成份如表2所示。检测得到曲轴材料成份均在名义成分范围内,因此,曲轴材料成分满足要求。对断口进行金相组织检测分析,得到的金相组织如下表3所示。各金相组织成分均在技术要求范围内,因此,曲轴材料金相组织满足要求。
对曲轴各轴颈圆角进行检测分析,采用投影测量仪测量曲轴断口位置圆角,测得的曲轴圆角投影显示,曲轴圆角过渡处存在明显尖角,属于圆角滚压不合格。曲轴圆角滚压工艺能大幅提高曲轴疲劳寿命,其原因在于:金属表层在滚轮压力作用下,当应力超过材料的屈服极限时,产生塑性变形,发生冷作硬化,使硬度得以提高,从金属表层直到某一深度出现残余压缩应力,在深层产生低值的补偿拉应力。去除滚轮压力后,表层塑性变形略有恢复,然后达到稳定。压缩应力由于永久变形的存在,残留下来。表层的残余压缩应力,抵消了部分工作拉伸应力,而拉伸应力是金属疲劳破坏的主要原因,这样就使零件疲劳强度大大提高。而当曲轴产生滚压缺陷时,表层残余的压缩应力不能抵消部分工作拉伸压力,并且还产生拉伸应力集中,在曲轴进行疲劳试验时,应力会被放大,放大的应力在长时间的疲劳试验过程中,会产生产生裂口并逐渐放大并导致曲轴断裂。
因此,根据曲轴圆角投影的结果可以判定:曲轴圆角滚压缺陷是导致此次曲轴断裂的主要原因。通过通知曲轴厂家整改曲轴工艺,加强曲轴出厂投影检查验并重新提供样件,进行400h全速全负荷试验,曲轴未再发生断裂现象。
结语
分析曲轴断裂一般从初始仿真分析、材料的成分和性能、曲轴的加工工艺等方面进行。本文利用曲轴仿真学对曲轴进行分析,得到曲轴各主轴颈及连杆轴颈安全因数均能满足要求;然后针对曲轴的材料成分、金相组织进行判断,得到曲轴的材料同样满足要求;最后对影响曲轴性能较大圆角进行投影检测,得到曲轴滚压圆角存在严重的小角缺陷,是导致曲轴断裂的主要原因。
评论 0
正在获取数据......