汽车(尤其是乘用车)在正常使用过程中,车身的外覆盖件不可避免地会受到外载荷的作用(包含人为触摸按压静载荷和行驶过程中产生的振动、碎石撞击等动载荷),经常使得外覆盖件形状发生凹陷挠曲甚至产生局部永久凹痕。制件在受到外部载荷作用下,通常变形特征表现为弹性变形和塑性变形两类。在汽车制造行业,一般把外覆盖件承受外部载荷作用,抵抗凹陷挠曲及局部凹痕变形、保持形状的能力称为抗凹性,其中包括抗凹刚度、抗凹稳定性及局部凹痕抗力三个方面:
1)制件抵抗凹陷挠曲的弹性变形能力称为抗凹刚度。
2)对有一定曲率的扁壳外覆盖件,外部载荷作用达到一定程度时,抵抗弹性变形的能力就会突然丧失,发生失稳变形,覆盖件抵抗失稳的能力称为抗凹稳定性。
3)塑性变形则为外载荷作用下发生凹陷,载荷去除后,试件表面局部残留永久凹痕,而试件或覆盖件抵抗局部凹痕变形的能力称为局部凹痕抗力。
本文主要从冲压件总成和冲压单件两个方面入手,探讨产品结构设计对外覆盖件抗凹性能影响。
冲压件总成抗凹性影响因素分析
1.冲压件总成抗凹模型建立
目前,一般汽车企业在产品开发设计阶段,需采用有限元分析对整车外覆盖件的抗凹性能进行分析,主要是根据总成数模建立抗凹有限元分析模型,分析使用的软件一般有ANSA、ABAQUS和HYPERVIEW,钣金件采用SHELL单元离散,然后输入分析所有的边界约束条件。
以前门总成为例,在进行抗凹性分析时,约束前门铰链及锁扣处所有方向的自由度,然后约束缓冲块平动自由度,如图1所示。根据经验在前门上选择9个分析点,如图2所示,通过刚性压头,对分析点垂直于表面施加一定力的载荷(400 N),并考察分析点的最大变形、残余变形、塑性应变及不稳定区域是否达到目标值。我司现行标准如表1所示。
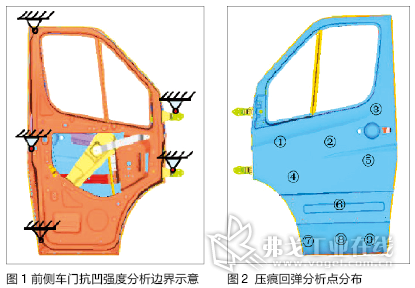

2.冲压件总成抗凹性影响因素分析
在产品设计开发阶段,通过对整车外覆盖件的抗凹性能分析并确认刚度较弱区域后,设计人员需在该区域进行结构优化设计,提升整车外覆盖件的抗凹性能。具体可以通过以下几个方面进行改善。
(1)内外板支撑间隙
当外覆盖件抗凹性不足时,一般会在薄弱区域进行内板支撑设计,如车门外板、翼子板等在造型平坦、曲率大且区域大的部位均会设计支撑件(图3)。一般外覆盖件的支撑结构如图4所示。设计支撑时要求内板的支撑臂与外覆盖件不能为刚性接触或直接连接,即内外板的间隙L1、L2>0,同时内外板需通过填充胶粘合。支撑条件设计是否有效,对车身外覆盖件抗凹性的改善程度起关键决定作用。
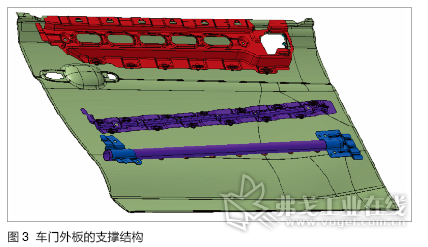
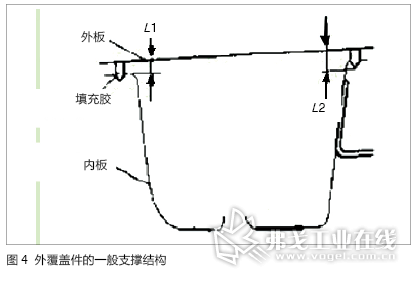
(2)内外板支撑密度
在外覆盖件抗凹性不足的区域进行内板支撑设计时,支撑密度也是影响支撑条件的重要因素之一,设计人员需在综合考虑整车轻量化、安全性等性能的基础上,适当地增加支撑密度来提升外覆盖件整体抗凹性能。
(3)无支撑条件下的刚度补强
消声片的选择使用,是最为简单、最为直接有效的提升外覆盖件抗凹性能、减振降噪的手段。一般在整车试制阶段外覆盖件抗凹性能不足的情况下使用,是对设计不足进行的快速弥补措施,使用成本较高。
(4)其他方面
通过合理设计内外板支撑间隙的大小,以及选择恰当的填充胶型号等方式,均可以提升外覆盖件的抗凹性能。
冲压单件抗凹性影响因素分析
1.冲压件抗凹模型建立
车辆在设计阶段为了降低风阻、提高整车动力性,车身外形一般采用流线形双曲扁壳造型,如乘用车顶盖、车门、翼子板、车头发动机舱盖和车尾行李箱盖。因此,外覆盖件的抗凹性问题研究,可以转化为双曲扁壳受横向集中载荷的变形及稳定性问题研究。外覆盖件的抗凹刚度可分为基本刚度和大位移凹陷刚度。
(1)基本刚度定量评估
双曲壳外覆盖件基本刚度参数K的理论计算公式为: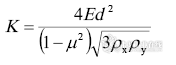
(2)大位移抗凹刚度评估检测准则
工业检验水平为当F<100N、位移≤10 mm时双曲扁壳覆盖件抗凹刚度的定量检验准则公式为:
(3)静态局部凹痕抗力定量评估指标
双曲扁壳覆盖件局部凹痕抗力的定量评估指标(10 N·mm)的计算公式为: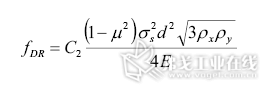
3个公式中,ρx、ρy为双曲扁壳主曲率半径;d为板材厚度;E为弹性模量;m为泊松比。研究表明,双曲扁壳外覆盖件基本刚度、大位移抗凹刚度及静态局部凹痕抗力的定量评估指标,三者综合反映了各种影响参数之间的定量关系,经试验验证具有良好的可靠性。因而,可用于指导轿车外覆盖件的造型设计、板料的选材以及工艺参数的优化。
2.冲压单件抗凹性影响因素分析
冲压件单件的抗凹性影响因素可以从统筹宏观、微观两个层面考虑。
(1)宏观层面分析
从宏观层面上来说,冲压件单件抗凹性主要影响因素为单件的几何形状及其断面形状惯性矩的大小。具体包含有外覆盖件的截面形状、曲面曲率、大曲率曲面面积大小及曲率面的边界条件等。
某翼子板上不同位置的曲率半径及形状如图5所示。
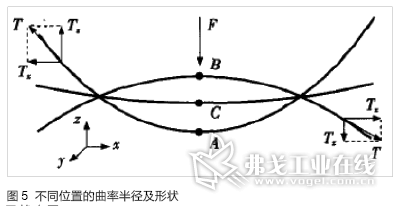
其中,A、B、C为抗凹性实验分析点;TX为水平方向的分解拉力;TY为垂直方向的分解拉力;F为载荷;T为拉力。
根据CAE抗凹性能分析研究发现,A点的抗凹性能大于C点和B点。分析原因为:①双曲扁壳制件在受到集中载荷作用发生弯曲的时候,其膜应力和弯曲应力承担横向载荷,随着壳体的曲率半径减小,膜应力在总应力中占的比重会随之增大,壳体的承载能力也随之增加,因而曲率半径越小,制件局部抗凹能力越强。故A点的抗凹能力大于C点。②A点和B点的曲率半径一致,A点处于凹陷区域,B点处于凸起区域。当压头对作用点施加载荷时,A点周边的质点在载荷作用下垂直方向的分力与作用载荷相反,对A质点产生反拉力,壳体的承载能力也随之增加,制件局部抗凹能力加强;B点刚好相反,B点周边的质点在载荷作用下垂直方向的分力与作用载荷一致,对B质点产生正拉力,壳体的承载能力也随之降低,制件局部抗凹能力减弱。
综上所述,在载荷加载初期,制件局部抗凹能力主要取决于分析点的曲率半径,曲率半径越小,抗凹能力越强;当载荷超过一定数值时,即分析点周边的质点在载荷作用下垂直方向的分力作用超过曲率半径的影响时,其处于凹陷区域比处于凸起区域制件的局部抗凹能力强。
因此,在进行外覆盖件设计时尽量避免大而平的造型,应增加棱线特征、减小外观面的曲率、缩小单一大曲率外观面面积或改善单一大曲率外观面的边界条件。
(2)微观层面分析
从微观层面,冲压件单件抗凹性主要影响因素为材料的物理性能、料厚、材料的减薄率以及变形是否充分等。对于产品结构设计来讲,主要影响为选择材料的物理性能,即选择何种材料以及选材的料厚。
根据双曲壳覆盖件基本刚度参数K的计算公式可知,材料的弹性模量E和板材的厚度d与制件的基本刚度存在强相关关系。材料的弹性模量值E越大,制件的刚度K值越大,覆盖件的刚度就越强;板材的厚度d与刚度K的二次方成正比,即板材的厚度d越大,制件的刚度K值就越大,覆盖件的刚度就越强。
刚度问题基本上是制件弹性变形范围内的现象,与其屈服强度和强度极限似乎没有直接的关系。但实际材料的屈服强度和强度极限越高,其在冲压成形过程中越难产生塑性变形,同时产生塑性变形后的弹复量也越大,小曲率覆盖件的形状冻结能力随之降低。实验证明,在产生相同挠度的情况下,弹复量大的制件比弹复量小的制件所需载荷降低,即弹复量大的制件的刚度差。因此,材料的屈服强度和强度极限越低,覆盖件的刚度越高。在进行外覆盖件设计选材时,在保证车身安全性能和满足轻量化的前提下,应尽量选择屈服强度和强度极限小、弹性模量和料厚大的材料。
总结
本文通过对覆盖件的总成及单件抗凹模型的建立,分别从冲压件总成结构设计及冲压单件设计两方面研究了产品设计对冲压件抗凹性的影响,对指导新车型研发设计具有重要参考意义。
评论 0
正在获取数据......