转向节是汽车转向桥中的重要零件之一,能够使汽车稳定行驶并灵敏传递行驶方向。转向节的作用是传递并承受汽车前部载荷,支撑并带动前轮绕主销转动而使汽车转向,汽车在行驶状态下,转向节承受着多变的冲击载荷,因此要求其具有很高的性能。而轿车的质量要求更是毋庸置疑,对转向节提出了更高标准的要求。
一汽锻造公司承担的此款转向节为重点研发产品,其结构较为复杂,安全性能要求较高。毛坯前期策划为铸造工艺,经过工艺分析与仿真模拟测算,为了更好的保证产品功能性及使用性,最终确定了该产品的铸改锻方案。承接此产品后,相关技术人员与整车研发人员共同探讨,协同开发,从锻造工艺的角度确定产品分模面、加工余量及外形,使其既能保证产品工艺成形,又能实现装配要求、功能性和使用性。经过调试锻打,首批合格锻件已提供,性能检测无问题,并已经加工出合格产品,进行后续试验工作。
锻造工艺分析
根据转向节产品三维,经过增加加工余量、出模角及叉口防变形等锻造工艺后,完成了相对易于锻件成形且不易造成锻件变形的三维设计。成形后的转向节锻件复杂系数S4,该复杂系数的超重锻件在乘用车转向节制造中实属罕见。
经过锻造成形力学分析,根据锻件投影面积初步计算所需锻打力在4500t左右。计算出所需锻打吨位并根据已有转向节生产经验,结合我司现有设备资源,确定了合适的设备,选择符合其工艺特性的1600t电动螺旋(摩擦压力机)做预锻,配合2500t电动螺旋做终锻。
具体工艺路线为:下料→加热→镦粗→预锻→终锻→切边→校正→热处理→硬度检验→表面清理→探伤→终检。
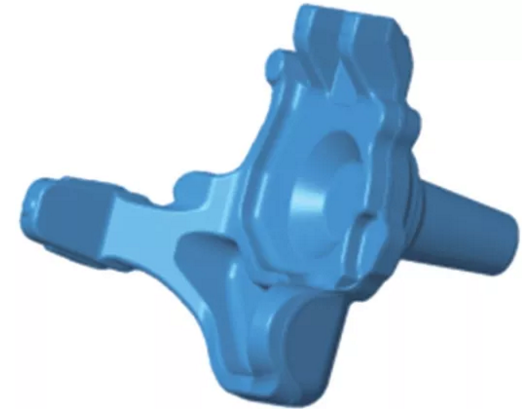
图1 转向节锻件
工艺技术难点分析及预防措施
⑴完成锻件设计后考虑其成形工艺,通过截面计算方法找到相对适合坯料分料的角度面,尤其要考虑的是支臂和杆部的分料。支臂长度约160mm,完全延展到锻件外侧,此处成形极其困难,锻打过程极易出现折叠和充不满等缺陷。根据已有生产经验,必须保证预锻在此处有足够多的存料,在终锻时采用排料原则,将有折纹趋势的坯料排放到飞边位置,避免缺陷产生。杆部长度超过120mm,为了保证其流线组织及机械性能,需通过挤压成形,如分料不均或杆部坯料不足,锻件易出现严重缺陷,无形中增加了预锻的难度。综合以上问题,选取了多个锻件截面进行计算,找到了与锻件成30°角(如图2所示)为坯料均衡摆放方向,坯料中心距离锻件杆部中心偏出20mm,截面计算后所需最粗坯料在φ130mm以内,且可以满足所有截面需求。
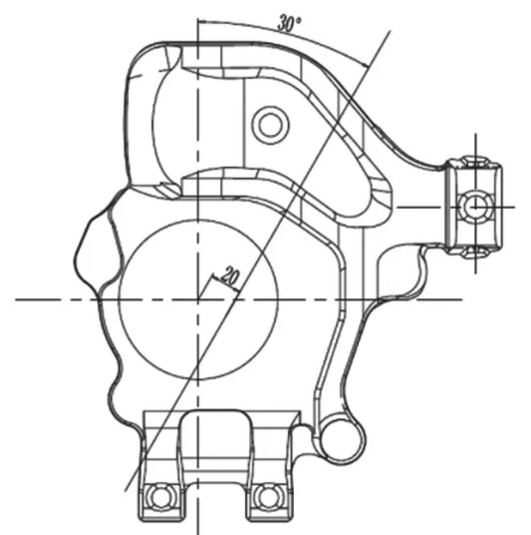
图2 锻件分料中心位置示意图
⑵锻件内部平面最薄尺寸为17mm,出现在环形筋部内窝槽位置,此处既容易造成成形折叠,又容易出现热处理淬裂,在前期设计过程中,充分考虑其潜在风险。为了避免锻件失效,通过圆角补偿和利用厚度公差上限进行调整,并且在预锻工步做好坯料的分配,在易出现折纹趋势位置做好坯料填充。
⑶叉口位置在锻造过程中易出现变形,根据以往类似件生产经验,切边后叉口易向内侧收缩,尤其在后续处理过程中叉口易造成磕碰挤压等变形。综合考虑以上因素,在叉口中间连接位置增加连皮,并且连皮通过后续机加工方式去除,这样一来,可以有效防止锻造过程中产生缺陷,保证生产出合格锻件。
仿真模拟及调试问题解决
将设计完成的初始模具及坯料转化到Forge有限元仿真模拟软件中进行预模拟,初步验证设计可行性,并通过模拟查看成形过程中是否出现折叠、充不满等潜在缺陷。根据初始坯料中心摆放位置,在预锻下模做好定位凹槽,如图3为经过镦粗后的坯料摆放位置,由于预锻下模有凹槽,极好地限制了坯料的滚动,减小了操作者的劳动强度,并且降低了操作风险,从而实现预锻毛坯一致性。
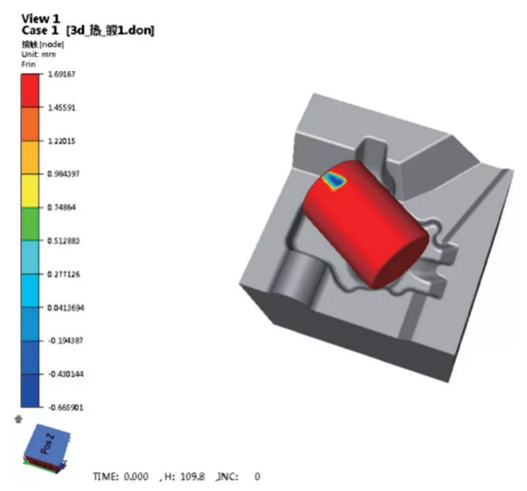
图3 坯料摆放示意图
解决了预锻模具的坯料定位问题后,终锻工序通过型腔即可达到定位要求,无需额外增加定位。从仿真模拟分析(图4、图5)结果来看,锻件在两道工序中无折叠、充不满等缺陷,锻件最难解决的长臂问题,通过成角度摆放及模具设计得以解决,对长臂位置检查,无任何缺陷。杆部位置通过可变圆角设计,使坯料快速向杆部型腔充填,杆部充满无问题,而且不至于造成杆部流线断裂,极大的提高了锻件性能。
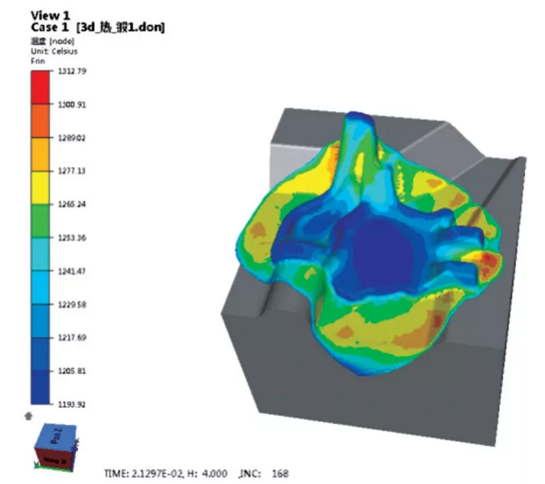
图4 预锻工序仿真模拟分析
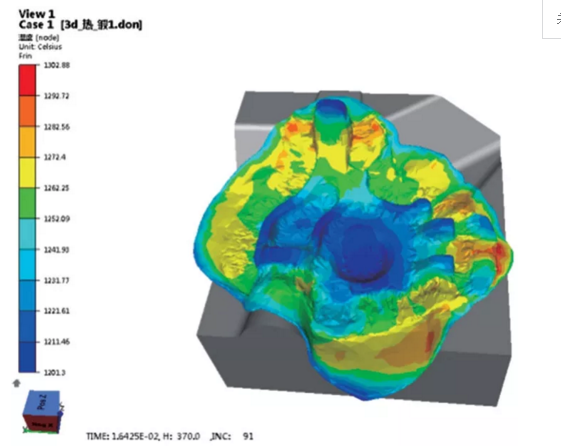
图5 终锻工序仿真模拟分析
在实际调试生产过程中,通过在预锻和终锻模具上增加锁扣来控制锻件错差,锁扣间隙设置为0.5mm,为保证合模时不产生碰撞,锁扣设计出7°斜度。锁扣不仅控制了锻件的错差,而且抵消了锻件曲面分模产生的错移力,保证生产出合格的锻件。设备的下死点依靠模具贴合后保证,根据锻件所需的锻打力调整输出力,并设计有合适的承击面,以此保证锻件的厚度,并保证在公差范围内。
效果验证
经过以上措施的实施,我公司完成了对铸改锻转向节的成功设计及调试,顺利保证了样件的提交。经过实验检测,拉伸和冲击性能均达标,锻件流线符合工艺要求(如图6)。目前由新工艺加工出的锻件成品,经检验后完全达标,现已在整车上安装。
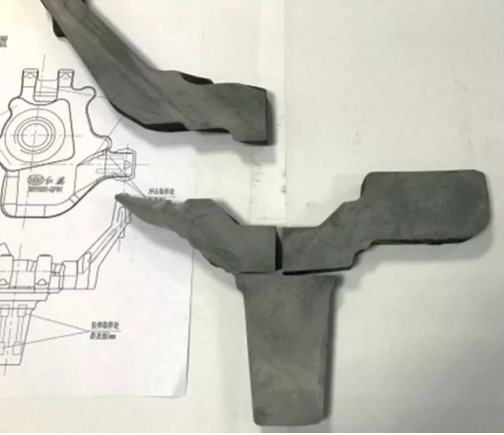
图6 转向节流线分析示意
结束语
此款转向节的成功研制,实现了我司首次转向节铸改锻的工艺改动,填补了我司在大型乘用车转向节开发与研制方面的空白。此件的成功研制大力提升了我司在转向节制造上的研发能力,同时极大增加了我司在转向节市场的竞争力。
评论 0
正在获取数据......