目前在国内,汽车螺旋锥齿轮的加工中,广泛使用的五刀法湿切效率并不高,且需在切削油冷却情况下进行切削加工,刀具和辅料的成本高居不下。相比之下,螺旋锥齿轮三轴切削干切技术,具有很多的优点。本文结合实例介绍了干切方法在螺旋锥齿轮加工中的应用。
一直以来,车桥公司的汽车螺旋锥齿轮都是采用收缩齿铣削法,齿轮的加工采用传统五刀法湿切加工,刀具采用普通高速钢盘铣刀,在切削油的冷却下进行切削加工。其工艺流程如图1所示。五刀法加工的不足之处在于:分粗精切齿加工,生产效率低;刀具寿命低;切削油污染环境;综合制造成本高。
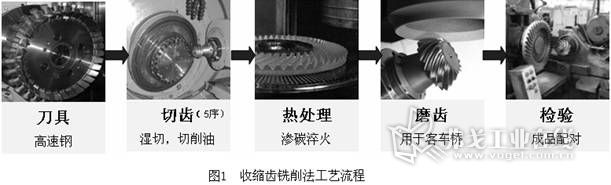
相对于传统的切削方式,螺旋锥齿轮三轴切削干切技术可削减70%的切削时间,提升切削零件的表面粗糙度,提高零件的加工精度。其工艺流程如图2所示。该技术在北美和欧洲已得到广泛应用。同时,干切技术作为一项绿色制造工艺,省去了切削液及处理费用,降低了齿轮生产成本。
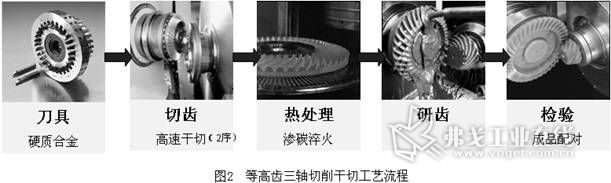
为提高齿轮产品的质量和市场竞争力,我公司于2010年起实施螺旋锥齿轮三轴切削干切项目,建成两条螺旋锥齿轮干切生产线,并系统开发了螺旋锥齿轮三轴切削工艺,应用于重型主从动锥齿轮产品。该工艺的应用在加工效率、零件质量和加工成本等方面取得了很好的效果。
三轴切削原理和接触特性
端面铣削法及端面滚削法是螺旋锥齿轮和准双曲面齿轮的两个主要加工工艺,传统的五刀法加工采用端面铣削工艺,三轴切削干切采用端面滚削工艺。端面铣削工艺中,齿向曲线是一个圆弧,齿轮加工是间歇分度;端面滚削工艺中,齿向曲线是一个延伸外摆线,是由刀具和工件以一定的关系连续分度运动产生。端面滚削比端面铣削更复杂,因为它是两个独立的运动,分度和滚动展成叠加而成的。
1.连续分度
端面滚削(三轴切削)齿轮啮合的从动轮和主动轮可被认为各自与产形轮滚动展成。我们可以认为4个齿面同时啮合,即主动轮和从动轮的齿面,以及与主动轮和从动轮各自相配的产形轮。产形轮可被认为是一个节锥角为90°的锥齿轮。产形轮的概念是当展成时,主动轮和从动轮的啮合齿面是完全共轭的。实际上为了使啮合齿面失配,主动轮和从动轮的产形轮并不相同。图3所示为三轴切削连续分度示意图。
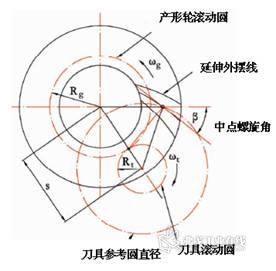
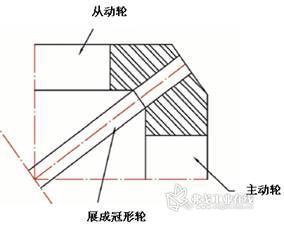
图3 三轴切削连续分度示意图
端面滚削过程中,刀具与产形轮以下面的关系进行滚动运动:
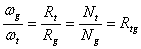
此相关的运动形成了连续的分度,端面滚削工艺一次装夹工件,同时切出齿槽的凹面和凸面,它可以被视为一个全工序的工艺。
2.刀具
端面滚削刀盘是由成组的刀条集合而成。每一组刀条是由一片内切刀和一片外切刀组成,相应切削一个齿的凸面和凹面。两个刀片角向和径向的位置直接决定了齿厚。刀片沿着刀盘圆周方向呈一定角度等距分布。
除了对刀片位置的要求,刀片的切削刃也需精确定义。这是由于刀具切削刃形成了齿面,刀片的几何形状取决于刀条刃磨工艺。切削刃的几何形状由三部分组成:刀尖圆角、凸角和切削刃轮廓。
3.齿面接触特性
通常,端面滚削(三轴切削)螺旋锥齿轮和准双曲面齿轮副产生一个稳定的接触迹线,对壳体和轴的变形或装配误差相对不敏感,这是由于延伸外摆线的本质和适当的齿面鼓形修形的结果。稳定的接触迹线模式有利于研齿工艺,同时也提供了更高的接触比。结果,端面滚削齿轮副可以达到降低噪声的目的。啮合迹线和铣削纹路方向如图4所示。
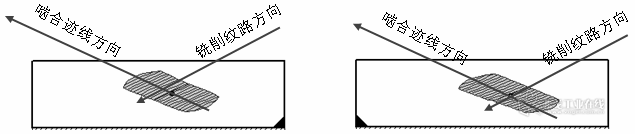
图4 啮合迹线和铣削纹路方向
三轴切削工艺应用
1. 材料
齿轮材料20CrMnTi,淬透性较高,经渗碳淬火后具有硬而耐磨的表面与坚韧的芯部,具有较高的低温冲击韧性,正火后可切削性良好。除化学成分外,其他技术标准执行东风德纳车桥公司齿轮材料标准(DDACL-002-2010)。

材料选用要求如下:
(1) 钢的化学成分符合表1的要求;
(2) 成品钢材氧含量不大于0.0020%,后桥主、从动齿轮用钢氧含量不大于0.0015%;
(3) 按GB/T 6394规定检验奥氏体晶粒度;
(4) 钢材的横截面低倍组织不得有肉眼可见的缩孔、气泡、裂纹、夹杂、分层及白点;
(5) 按GB/T 13299检验轧材的带状组织,带状组织级别应≤3级。
2.毛坯锻造及正火
针对首轮试制结果刀具寿命不理想的状况,对材料和毛坯锻造和等温正火做了如下改进和要求:
(1)规定S含量的下限要求(在前面材料化学成分中已体现);
(2)毛坯锻造始锻温度1150±50℃,终锻温度1000±50℃;
(3)等温正火加热温度950℃,保温2h,速冷210s,等温温度580℃,时间2h;
(4)正火硬度要求HB 170~180。
材料、毛坯锻造及热处理改善后,每次刃磨后加工齿轮件数由80件提高到115件,刀具寿命提高了大约33%。
3. 刀具及切削加工
刀具为两面刃磨的Tri-ac硬质合金刀条,材料为Co含量8%的硬质合金材料,ISO牌号K30。
切削加工时发现内外切削刃的磨损程度存在显著的差异,内切削刃的磨损显著大于外切削刃。由于刀具的几何尺寸决定了齿面的参数,修改刀具的几何尺寸已无可能。通过修改Z轴进给角度并多次验证,解决了内外切削刃磨损差异的问题。
4. 热处理工艺
产品的热处理技术条件:有效硬化层深1.5~1.8mm;表面硬度HRC 58 ~63;芯部硬度HRC 30 ~ 40;残余奥氏体级别≤4级,马氏体级别≤4级;碳化物级别≤4级。
从动轮热处理渗碳淬火,淬火方式压淬,油温控制在60℃±10 ℃左右。
5.研齿工艺
三轴切削等高齿的接触区一般为内对角接触,有利于研齿并降低啮合噪声。
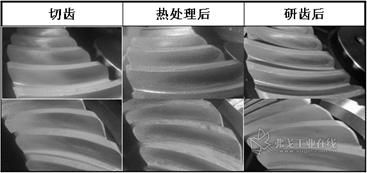
图5 切齿及研齿前后接触印迹对比
在600HTL数控研齿机上进行研齿,从热前及热后接触区印迹看(见图5),热处理后正车面接触区由小端向大端偏移,反车面接触区由大端向小端偏移。在设计TCA时,应当考虑热处理变形的偏移量。热处理后采用研齿工艺可优化接触区形态,降低啮合噪声约3~4dB。
6.刀具涂层技术
三轴切削干切采用了两面刃Tri-AC®刀条,刀条前刀面已涂层,重磨不必涂层。正式生产后,加工模数11mm左右、直径300mm的齿轮,刀具重磨后主动轮大约可加工100件,从动轮大约可加工80件。为提高刀具重磨后加工零件的数量,我们与苏尔寿-美科涂层中心合作,采用氮铝化钛涂层,硬质合金刀条重磨后涂层,表面硬度可达到HV3100,具有高热硬性、耐磨性,适合三轴切削干切条件。涂层后,刀具加工主动轮零件的数量由100件左右提高到300件,加工从动轮零件的数量由80件提高到270件,大约是未涂层刀具加工数量的3倍,且不增加切削成本。
应用效果
1.齿轮精度
检测结果显示,主动轮周节累计误差和齿距极限偏差达到GB/T10095.1-2001标准5级;从动轮周节累计误差和齿距极限偏差达到4级。三轴切削齿轮切齿精度与五刀法齿轮相比提高了两个等级。
2.啮合噪声
测试条件:600HTT数控锥齿轮检验机,主动轮转速分别为1500r/min和2000r/min。
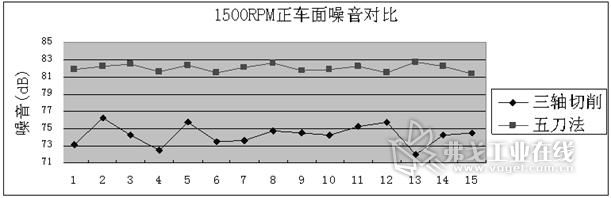
图7 三轴切削和五刀法切削噪声比较
从图7的啮合噪音数据对比可知,我公司采用三轴切削干切的轮减桥齿轮与五刀法加工的齿轮相比,1500r/min情况下的啮合噪声下降约7dB。
3.生产效率及成本对比
对动轮三轴切削干切和五刀法湿切加工的生产效率、刀具消耗和电能消耗进行对比,如图8、图9所示。
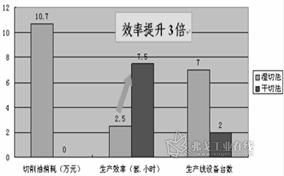
图8 生产效率对比
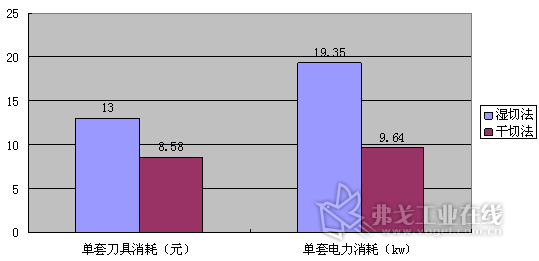
图9 刀具消耗和电能消耗对比
总体分析,三轴切削在人力成本、物流成本、刀具成本以及电能消耗等方面综合成本降低8.81元/件。
结语
由于数控技术的快速发展,汽车螺旋锥齿轮三轴切削干切技术将是未来的发展趋势。三轴切削干切具有零件表面粗糙度高、精度等级高、齿轮啮合噪声低、加工效率高以及清洁无污染等特点,随着对齿轮材料、热处理工艺、刀具及涂层技术的深入研究,三轴切削干切技术将会在国内的齿轮加工中得到更广泛的应用。
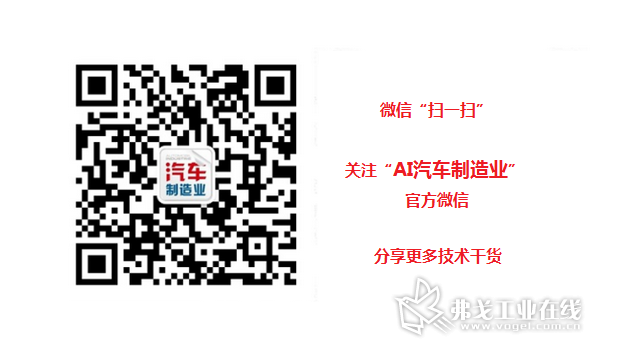
评论
加载更多