我国汽车制造业经过多年的发展,四大工艺生 产线的自动化水平已经达到了较高的水平,目前正 在积极发展数字化工厂的智能生产模式。
我们研发的总装车间数字化工厂管理系统中, 包括了工业大数据平台技术、高柔性全自动化中控 系统和基于大规模个性化定制生产的信息化与中控 系统的深度融合技术,对汽车总装车间生产模式的 转型升级起到了巨大的促进作用。
通过对智能化、数字化、网络化以及信息化技 术的融合应用,我们积累了一定的经验,更好地助 力“中国制造 2025”。
项目目标和主要技术指标
针对汽车总装车间,我们制定了研制出一款可 满足多种不同车型的在线智能识别、在线检测的数 字化总装车间的数字化管理系统的任务,要求实现 以下多项目标:
1. 实现多种车型的在线智能识别与生产,最 高年产能达到 10 万辆。
2. 基于智能 MES 系统,实现包含订单排程下的 车型智能导入等车间数字化生产和数字化管理,实 现数字化和个性化定制生产的功能。
3. 实现汽车总装系统的远程诊断管理功能。
4. 利用数字化工厂仿真技术,实现装备系统 全线虚拟仿真技术,在虚拟三维环境下实现产品设 计、制造工程和生产运行的有效衔接。
5. 需要达到的主要技术指标 ①实现多种车型的在线智能识别;②最高年产 能达到 10 万辆;③功能尺寸合格率≥ 95% ;④全尺寸合格率≥ 90%。
实施方案
1. 总体技术路线
(1)建立数字化模型
根据车型产品的特征和要 求,进行工程同步分析,建立总 装工厂总体设计、工艺流程及布 局的数字化模型。为达到计划、 调度、质量、设备、生产及能效 的全过程闭环管理,实现供应链、 物流和成本等企业经营管理的优 化,建立总装车间制造执行系统 (MES)。为了使设计、工艺、制造、 检验和物流等各环节之间,以及 与制造执行系统(MES)和企业 资源计划系统(ERP)的高效协 同与集成,实现建立全生命周期 产品信息统一平台和研发、设计、 生产及运维的全生命周期管理, 构建工业大数据服务平台,并打 造供应链网络协同制造系统。网 络架构开发工作流程如图 1 所 示。
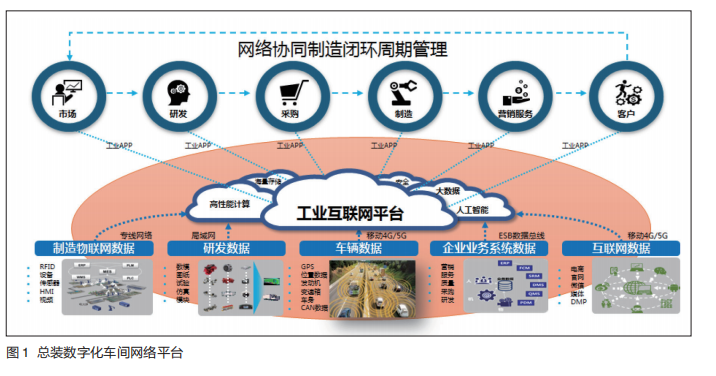
同时对于设备层面,车间所 有的关键技术装备能够在生产网 络中实现互联互通与高度集成, 要规划车间的工艺装备,并规划 智能传感与控制装备、智能检测 与装配装备、智能物流与仓储装 备等数字化装备。
(2)规划总装车间数字化网络架构
通过光纤将 Scalance 光纤 交换机组成环网,各 PLC 设备 的 CP343 连接至交换机,中控 WinCC 从各设备采集、下发数 据,通过工控机的另一网卡与工 厂网络连接,单独与 MES 通信, 各 PLC 不接入工厂内部网络且 不直接与 MES 通信。WinCC 服 务器由两台组成,互为冗余架构。 总装数字化车间网络架构如图 2 所示。
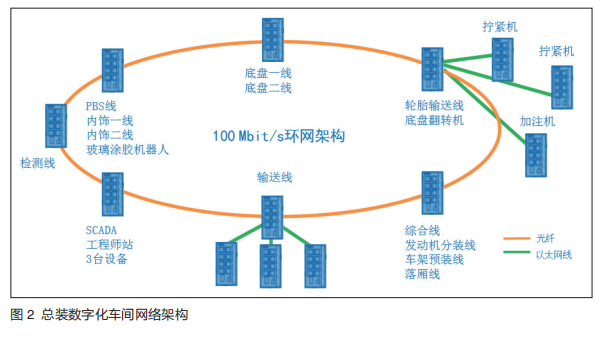
(3)模拟仿真验证
针对研发的各项关键数值装 备,进行多次模拟仿真验证,制定各关键技术详细的技术路线以 及研发计划及试制、试验计划。 模拟仿真如图 3 所示。
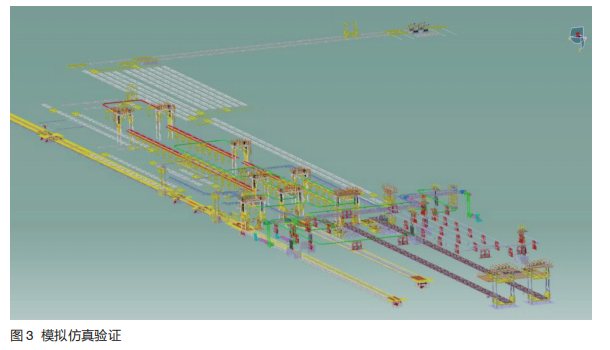
2. 数字化网络控制系统设计
(1)供应链网络协同制造实 现供应、物料的数字信息化 数字化总装车间供应链网络 协同的总体框架指引思想要求工 业互联网平台做到数据安全、网 络安全、平台安全和应用安全的 基础上,采集车辆运行数据、工 厂物联网数据、业务系统数据及 客户数据四类数据,形成企业与 产品的互联、工厂内部互联、企 业运营管理系统互联、企业与客 户互联的四种互联,数据通过工 业互联网平台的数据流动、模型 算法、人工智能、高性能计算加 工和智能工厂、智能管理及智能 汽车的三大智能应用服务,助力 工业生产过程优化、企业运营管 理决策优化。数字化总装车间协 同制造的架构设计如图 4 所示。
(2)工业大数据服务平台实 现研发、设计、生产和运维的全 生命周期管理
工业大数据服务平台以HANA (高性能分析设备)+Hadoop(大 量数据分布式处理软件)为基础, 采用分层架构设计,进行数据模 型的规划、设计、维度的建立及 各报表和服务的开发。系统整体架构支持万兆网络,具有统一调 度资源、快速布署、分布式计算、 存储和动态扩展等特点。
(3)高柔性自动化中控系统 实现数字化和信息采集
高柔性自动中控系统主要是 采用现场总线的通信协议,对于 不同协议现场总线的设备可以采 取基于 OPC(工业标准过程控 制)技术的通信来完成现场设备 与上位机的通信。
(4)基于物联网的汽车总装 装备远程诊断管理系统,实现从 工厂到设备层的数字化运维
本系统主要基于传感器技 术、智能分析技术、大数据处理 技术、故障诊断预测技术、物联 网技术及视频识别技术等基础技 术,采用标准比对、文献查阅和 实地调研等研究方法,厂房到设 备、从生产到工艺的完全考虑, 完成基于物联网的远程诊断管理, 实现数字化的运维管理。在智能 工厂运转的过程中,会产生设计、 工艺、制造、仓储、物流、质量 和人员等业务数据,这些数据可能分别来自 ERP、MES、WMS(仓 库管理系统)和 QIS 等应用系统。
3. 实施步骤
(1)在项目实施之前,根据 本项目的内容和程序以及研发产 品的特点,进行项目的总体策划 工作,以提高项目的管理水平, 促进项目管理的科学化、规范化, 保证项目目标的实现。
(2)本项目中采用 6 种软件 及装备。
1)设计工艺仿真软件
①机械设计软件(CATIA);
②机械设计软件(CAXA);
③机 器人仿真软件(Simpro);
④电 气图纸设计软件(EPLAN);
⑤ 离线编程与仿真软件(PDPS)。
2)工业控制软件
关键特性在线管理系统:可 编程逻辑控制系统(PLC)。 3)业务管理软件 机器人生产管理系统(MES)。
4)工业互联网系统和设备
①基于 TCP/IP 技术的工业 互联网系统,实现数据采集、数 据交换管理;②融合 Profinet、EtherCAT 和 PowerLink 等多种 工业数据总线技术的工业以太网 OPC/UA ;③工业互联网安全系 统与设备,提供信息安全保障。
5)本项目建设过程中,将使 用涵盖 3 个类别的 10 种智能制造 核心技术装备。主要采用的核心 智能制造装备有智能传感与控制 装备(2 种):①机运检测传感系统; ②上位机中控系统等。
效果验证及效益评价
1. 效果验证
基于大规模个性化定制生 产的信息化与中控系统的深度 融合技术和基于物联网的远程诊 断管理系统的研发应用,可以 改善产能过剩、产品积压、供 货周期长、设备维护保养困难、 维修不及时和效率不高等售后问 题。
2. 效益评价
该数字化管理系统有效连接 了客户、销售商和生产商之间定 制、下单及生产同步推进,对商 用车行业中传统的销售和生产模 式的转型升级起到了巨大的促进作用。
结束语
数字化生产模式已成为总装 车间转型升级的基础,伴随着数 字化的普及、生产效率的提升、 生产模式的创新以及新兴产业的 发展,具备感知、分析、推理、 决策和控制功能的数字化装备与 技术已逐步推广,将会应用到各 行各业。
评论 0
正在获取数据......