整车装配自动化发展探索和实践
孙淑均 王涛
AI《汽车制造业》
2022-02-22
自动化的探索和实践是汽车行业发展进步的必经之路。本文梳理了总装工程自动化所面临的问题,结合创新的实践经验,达到降低人力成本、减少劳动力匮乏的目的,进而提高品质,运行数据信息化,迎接智能制造。
纵观国内外汽车行业,一般汽车企业总装工程的自动化率在10%左右,甚至低于10%,而冲压、焊接及涂装等工程的自动化率都达到70%以上。推进总装自动化是整车制造走向智能制造的必经之路。
第一,自动化设备难以完全取代人工作业。在多数情况下,自动化设备控制和检测精度无法达到人手和眼的灵活程度,无法确保生产和品质的稳定,对应现场的复杂情况,尤其在多品种、柔性化及高节拍的生产线上,实现自动化的难度很高。
第二,为导入自动化设备,现有生产线改造难度大。因为控制精度目前难以匹配零件的运动状态,现有的自动化生产线大多只能在停止状态进行作业,这样需要增加停止位,占用更多的主线工位(图1),改造费用较高,改造周期较长,对现有生产影响大。
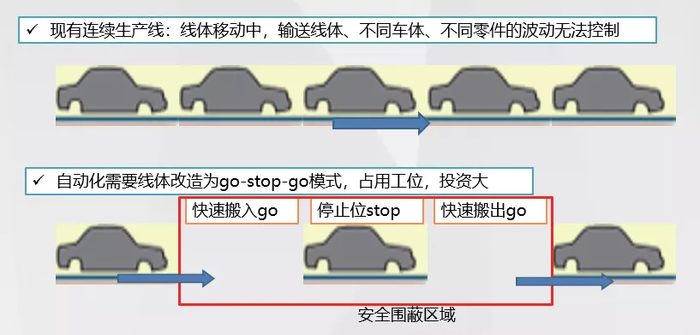
第三,自动化设备的维护要求高。导入自动化设备后,需配备良好的日常维护保养,出现品质问题时需要快速对应。如果没有相应的技术人才储备,就容易出现因故障率高导致生产效率反而下降的情况。
第四,自动化项目投资大,收益难。每个企业投入自动化,都会考虑投入、产出、成本和收益。自动化设备投入比较高,缺乏管理会导致运行成本增加。
要突破上述自动化的技术和收益等方面的课题,我们分别拟定了如下突破方向。
(1)优先导入可行性高、收益高的自动化项目。对总装车间多处作业系统分析,按可行性和收益性制定自动化推进MAP图。先从大件自动移载、制动盘面振自动化检测和拧紧等简单、效益高的项目做起,然后积累经验,挑战更难的项目。
(2)通过提高机器人利用率,减少其数量,降低自动化的投资。结合现场编程调整、完善布局,确保空间布局方便机器人动作灵活,实现机器人的价值最大化。
(3)应用工站式自动化,减少工位浪费。有效利用自动化停止工位,开发工站式自动化。通过调整作业编程,促使不同零件总成在一个工站内实现自动化。例如,通过机器人的立体布局,仪表板&全景天窗装配自动化集成。
(1)3D相机、激光等视觉技术多方位应用,突破定位和检测精度难题。为了解决设备定位和检测精度问题,需要在视觉技术的应用上开始进行更多的尝试。对比3D相机视觉系统和激光视觉系统后,我们发现3D相机的成像灵活,但是受外界干扰较大;而激光视觉系统成像精准,但是灵活性欠缺。结合两者的优点,在不同的自动化项目中,根据现场需求独立或组合配备视觉系统,让自动化设备从单纯的PLC控制定位,到机器人动作编程配合3D相机和激光视觉的集成应用,给机器人装上了“眼睛”,解决定位和检测精度问题。
(2)人机协作机器人应用开发,扩大自动化实施范围。当总装作业太复杂,难以完全用机器人代替时,可考虑人机协作机器人的应用。对于精度要求较高的部分由人完成,把机器人从“安全围栏笼子里”解放出来,人和机器人和谐共处,让人和机器人发挥各自的优势进行作业。人机协作机器人将在涂胶、拧紧、压紧和移载等方面有更多的应用潜力(图2)。

(1)进行系统性分析和要因保证,确保自动化可靠性精度
提升自动化的可靠性,在项目企划阶段,先做好可行性分析,充分考虑涉及的人、工艺、车体、零件、工作环境以及设备的精度波动,优先采用极差法,对影响因素进行精度分析,要求所有精度公差之和控制在标准范围内,则理论计算装配合格率为100%。如果极差法难以达到产品配合精度要求,则采用均方差法,所有精度公差平方相加后开根号,所得累计公差在允许范围内,理论计算装配合格率为99.73%,以此判断自动化精度以及项目的成立性。
在项目实施过程中,要监控各要因的精度变化,确保在其管控范围内。如果各要因在要求的范围内,而结果整体精度仍未达标,就要考虑是否有遗漏的要因,确保要因系的完整性,并在验证阶段进行反复、充分的验证,才能确保结果系的达成。在项目投入后,各项要因系的时效管理标准化,作为后续日常管理的基准。
(2)构建和完善自动化导入流程,确保问题点早期显现
自动化导入调试流程可分为六个阶段:定点静态调试、动态稳定性测试(视觉调试的关键)、小批量验证、大批量验证、试运行以及初流导入。各阶段设置不同的目标(图3),要求完成阶段调试报告,逐步推进验证过程。问题越早发现、越早对应,生产就越稳定。
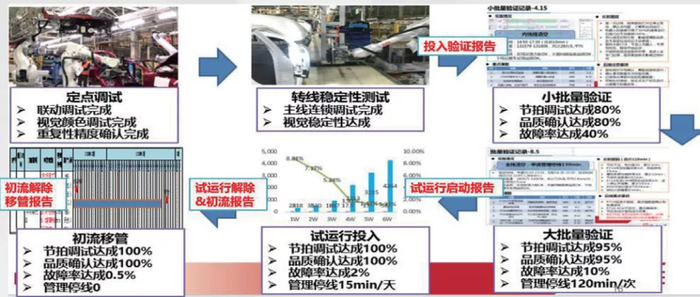
我公司把自动化划分为四类(图4),分别是:物流自动化、搬送自动化、装配自动化和品质检查自动化。在2016~2019年的3年中,我们进行了各项自动化的突破。
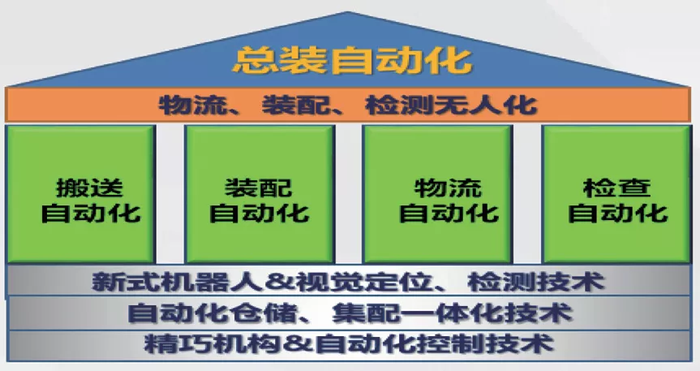
(1)在物流自动化方面,除了延续100%KIT中小物料自动上线外,我们扩展了AGV的应用(图5),破解了室外定位、交通管理以及环境多样复杂(下雨、大风天气运行)等问题,极大地提升了AGV的应用场景。
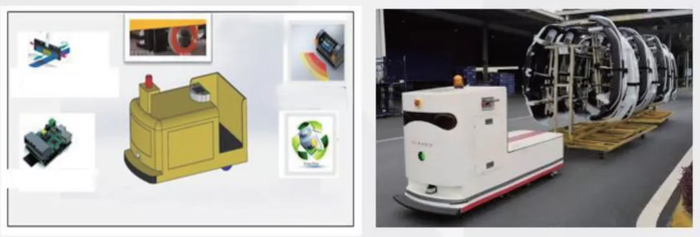
(2)搬送自动化,是指体积大的零件或总成的自动上线、投放。在这方面,导入顶棚输送线、后座椅自动化投入、天窗和后背门自动化移载等项目(图6),逐步实现大件上线和投入的全面低成本应用,降低了工人的作业负荷。
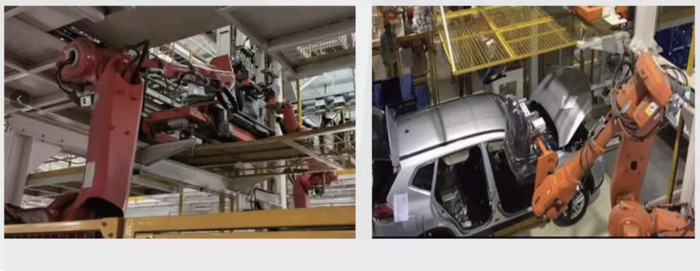
(3)在装配自动化方面,完成了3个行业首创项目量产(图7):分别是工站式仪表板&全景天窗总成自动化、风窗与三角窗集成自动化以及发动机和变速器对接自动化。通过结合现场编程调整,做好大总成上线配合,工站式系统性布局,解决了工位占用和布局调整困难的难题;通过视觉系统的导入,解决机器人定位控制精度等难题,现在项目已投入双班满负荷生产,生产指标达成。
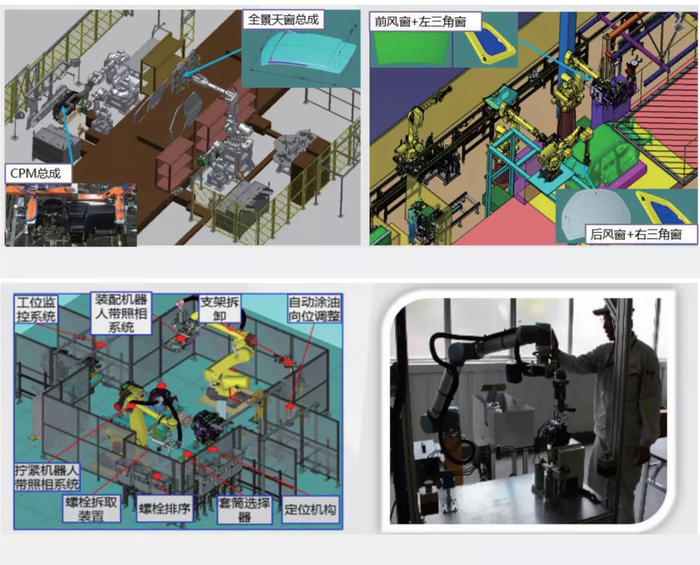
(4)在检查自动化方面,导入车体、零部件匹配精度检测、胶型检测及底盘检测等项目(图8),正在企划装配前车身在线精度检测,希望通过3D相机技术和激光技术在品质检测中的应用,实现检测自动化、解析智能化。
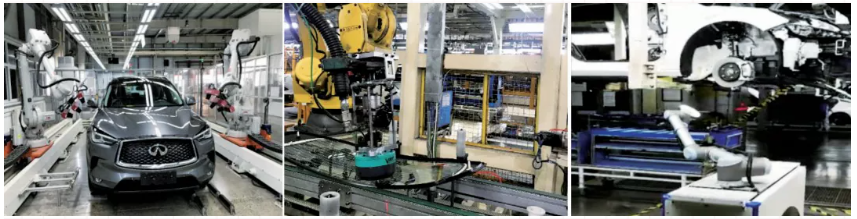
图 8 车体、零部件匹配精度检测、胶型自动检测、底盘自动检测
实施自动化MAP图以来,总装工程自动化率提升3%,大连工厂自动化率达到16.3%。结合相关作业编程优化,每年可节约人力成本2640万元。同时,自动化的投入极大改善了人机工程和品质,消除了24个红牌岗位和14个品质点位。
标准化也是工作总结的重要财富,我们根据实践经验编制了三类自动化相关的标准文件。
一类是品质管控基准,如《仪表板&全景天窗自动化品质管控基准》《风窗自动化品质管控基准》《发动机变速器自动化品质管控基准》,规范了相应自动化设备导入初期以及后续在始业点检、定期检查校正等方面各项品质参数的管理基准,确保设备的稳定性,保证设备安装的品质。
另一类是技术设计标准《总装自动化设备式样设计方法》,初步形成了自动化设备式样设计基础要求,明确了企划的布局图、精度图和节拍图的方案设计三要素。
还有一类是实施标准《总装大型主线自动化导入调试流程》,将现工厂的主线自动化项目导入细化为6个阶段,明确各个阶段的达成目标,以最大化地减少自动化设备调试投入对现生产的影响。
在物流自动化方面,重点放在通过一二次物流一体化,减少占地空间和转运的浪费;通过集配机器人的开发,减少集配的低附加值作业。
装配自动化方面,重点放在随行自动化和人机协助机器人的推广应用上。随行自动化要突破高速视觉,或者是输送设备的控制精度,人机协助机器人要突破机器人的载荷和安全保护。目前,随行自动化已实现备胎投放随行自动化,座椅投入随行自动化在导入中,轮胎随行自动化企划中,而人机协助ABS自动拧紧项目正在实施中。
总装整体自动化率的未来目标是20%,并且要将自动化和信息化有效结合,进行数据管理。数字模拟不仅可以用在导入前动作的虚拟模拟,还可以用在品质预测、设备故障预测中。未来长期目标是建立智能制造工厂,人和设备高效协同作业,自动化取代所有低附加值、重体力等岗位,人更多地投入到人机协同、数据管理决策等业务中。
AI《汽车制造业》
龚淑娟
李峥
评论 0
没有更多评论了