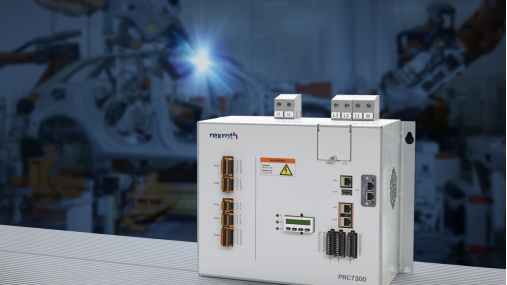
利用博世力士乐PRC7000焊接控制系统提供的新功能可以实现精密电阻点焊,从而提高生产率。(图片来源:博世力士乐)
车辆结构的趋势是日益轻便和安全。其中一个原因是:需要移动的重量越轻,所需能量便越少。然而,这绝不能以牺牲安全性为代价。与此同时,汽车的设计和样式也日益复杂。为满足当前在减重、能源效率、碰撞安全和设计方面的需求,组合材料的应用越来越广泛。这意味着对电阻点焊提出了全新的要求。博世力士乐PRC7000焊接控制系统所提供的解决方案可快速适应不同的材料混合情况,并建立更加牢固的连接。
减少二氧化碳排放和燃料消耗是汽车行业的一个关键目标。实现该目标的方法之一便是车辆减重,即采用更轻的材料,如铝、镁或纤维增强塑料。由于减重可使续航里程增加,再加上小型电池得以应用,电动汽车也在越来越多地采用轻型结构。
目标:实现不同材料和板材厚度的精密点焊
博世力士乐焊接销售和产品管理流程负责人Timm Bartmann解释道:“320个部件,80种不同类型的金属板材和厚度各异的涂层,导致的结果是需要对大约500种材料和厚度组合进行焊接,形成5000个焊点。这是当今白车身的典型状况。而且复杂程度还在不断上升。”
“在此过程中,各种金属、塑料或复合材料被组合在一起。采用新的材料组合可以减轻车身重量、改进设计、开发创新型产品,但也意味着电阻点焊必须达到非常高的标准。”
将不同材料焊接在一起,要求极高,因为材料的焊接性能各不相同。以越来越多地用于现代汽车的铝制车身部件为例,它们比钢轻,但焊接难度也更高,要确保连接点的安全性和稳定性须采用特殊的专业技能和技术。
Timm表示: “近年来,随着轻量化新设计的采用,带有防腐涂层的高强度钢材料在车辆制造中的使用量不断增加。采用高强度钢材,组件可以在机械性能不变的情况下设计得更轻薄,但这些材料在电阻点焊过程中通常更容易开裂。”
另一个难点在于对具有极端性能的铝和钢进行电阻点焊。钢的电阻高,铝的电阻低。博世力士乐的PRC7000焊接控制系统可同时应对这两种极端情况。变压器可精确转换焊接控制单元的输出功率,以适应焊接任务的要求。
解决方案:利用新一代焊接控制单元实现可靠连接
使用PRC7000,可以轻松焊接从钢到铝,板材厚度和材料类型各异的组合。为实现此目的,全新焊接控制单元采用了自适应控制器,并可灵活编程。它还使焊点具有可重复性。
一家领先的汽车制造商利用电阻点焊将大量铝部件与新车底盘相连接,这是有史以来第一次。在此情形下,主体由铝制成,并具有大约2000个不同铝板组合的焊点。
Timm Bartmann认为: “由于多种材料组合的采用,工艺窗口越来越小,即使有针对性地进行特定焊接任务参数化,传统电阻焊接系统也只能在有限范围内实现连接。而利用PRC7000,便有可能建立牢不可破的连接。利用PRC7000集成的“自适应位移调节”功能,可达到更加出色的焊接质量。过去无法可靠完成的焊接,现已可通过新功能来实现。”
作为全球领先的传动与控制技术供应商之一,博世力士乐致力于为各类机械和系统设备提供高效、强大、安全的智能运动解决方案。公司在行走机械应用、机械应用与工程及工厂自动化等领域拥有丰富的项目经验,并且凭借其智能元件、定制化解决方案及服务,为实现互联工业创造完美的应用环境。同时,博世力士乐还为客户提供各种液压、电子传动与控制、齿轮、线性传动及组装技术,软件及物联网的接口。公司业务遍及全球80多个国家与地区,拥有超过31,000名专业员工,2021年全球销售额近62亿欧元。
自1978年进入中国市场以来,博世力士乐已在北京、武进和西安建立了生产基地,截止至2021年12月,拥有约2,800名员工。
评论 0
正在获取数据......