0 前言
在汽车涂装生产过程中,由于喷涂环境等因素的影响,涂层可能会产生颗粒等缺陷,目前主要靠工作人员目视识别。由于人员作业过程中,存在视觉疲劳等不可控因素,缺陷容易流入下道工序,造成不合格品流出。采用视觉技术自动检测漆膜缺陷的技术,可以替代人员对漆膜外观缺陷进行识别,降低不可控因素的发生概率,降低不合格品的流出率。本文通过分析缺陷检测设备的工作原理,对自动识别技术及缺陷识别率影响因素进行讨论及分析,为生产线规划及设备选型时提供一定的依据。
1 视觉技术的应用现状
随着人工智能的发展,视觉技术已成为实现工业自动化和智能化的关键核心技术,在手机摄像头、3D人脸识别、三维场景重建、车载激光雷达及无人机等方面均有应用。
根据汽车行业的应用场景,视觉检测技术主要具备测量、引导、检测以及识别四大功能(图1)。其中,焊装车间的在线测量、质保间的蓝光检测等,主要采用结构光视觉实现测量功能;冲压车间的自动装箱、焊装车间的视觉抓件、涂装车间的车身定位以及总装车间的风窗玻璃自动安装等,主要采用多目视觉实现引导功能;焊装车间的涂胶、焊缝检测以及涂装车间的漆面检测主要实现视觉的检测功能;物流领域读码作业、焊装钢印识别等主要实现视觉的识别功能等。目前,视觉检测技术已经在汽车行业各专业有广泛应用,其中,涂装车间的漆面检测作为代替人眼识别漆面缺陷的技术,在国内已有多个案例,可以有效代替人眼作业,减少因人员视觉疲劳因素引起的缺陷流出。
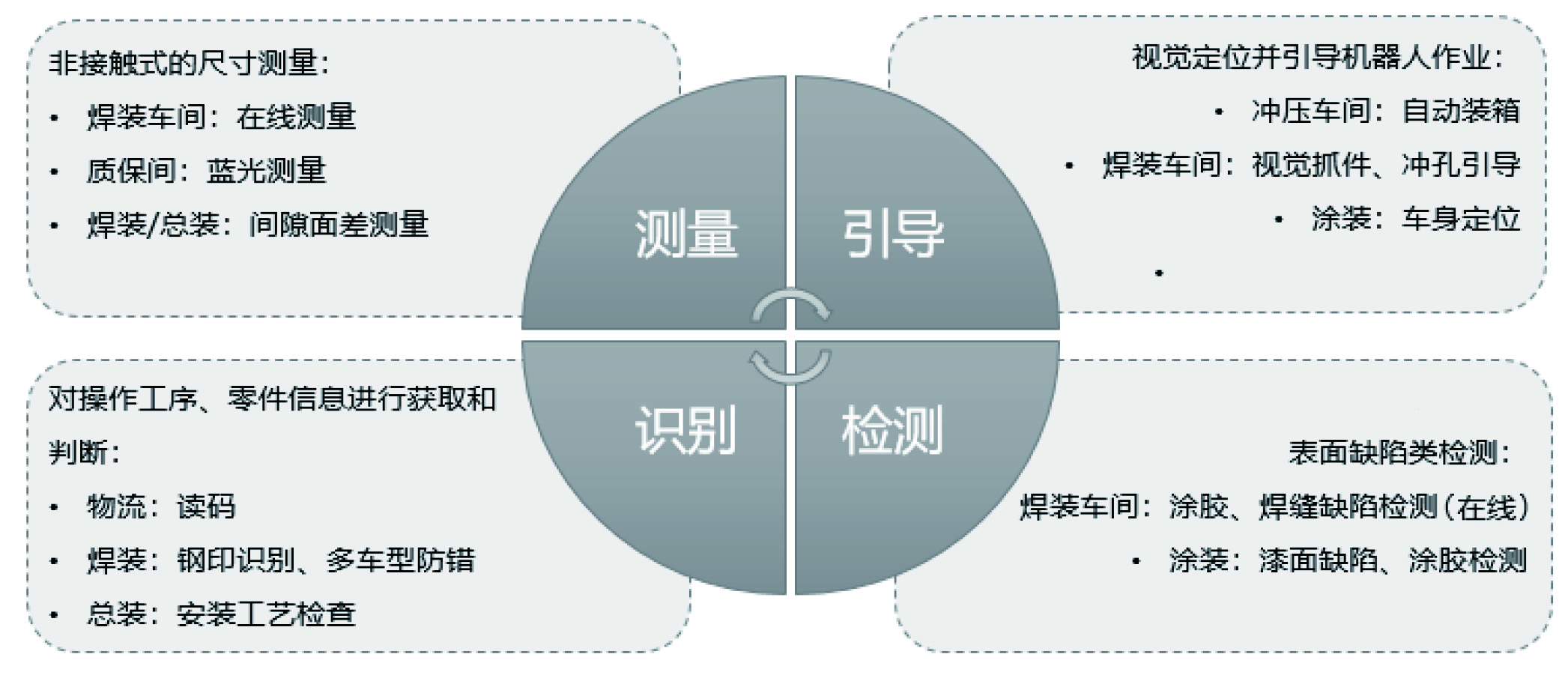
图1 视觉检测技术的四大功能
2 视觉技术检测缺陷的原理
根据图像处理系统的不同以及光源的不同等,汽车行业应用的视觉技术主要有图像融合技术、相位偏折技术以及深度检测技术。在汽车涂装漆膜缺陷检测领域,主要应用的技术为图像融合技术以及相位偏折技术。本文重点以相位偏折技术为例阐述其原理。
相位偏折技术是将光源投射到待测面上,利用反射图像相位在待测面微小变化敏感特点,根据相位解析及重建算法实现三维形貌及缺陷检测,如图2所示。
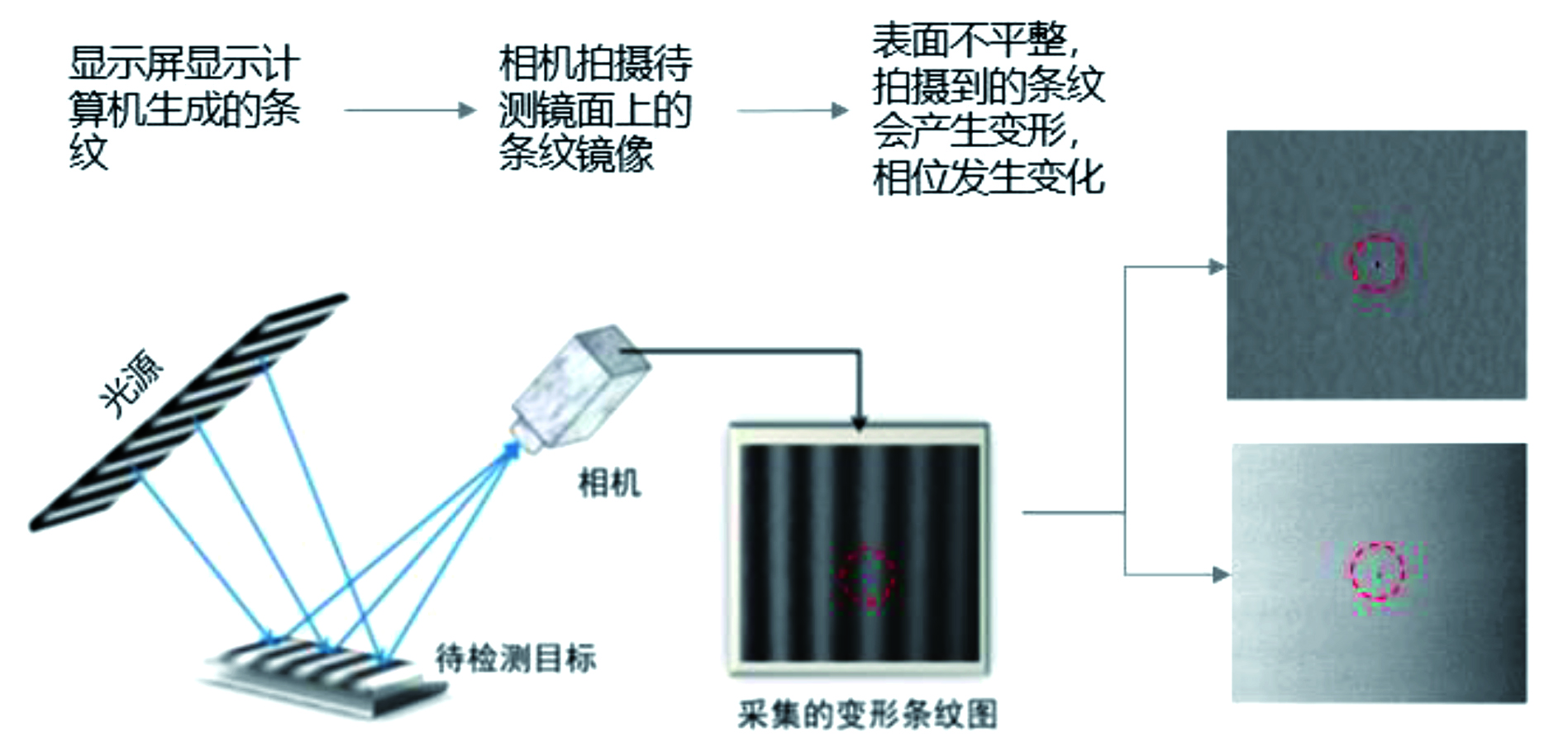
图2 相位偏折技术
由于此技术需要根据光的折射来采集图片信息,因此,只适用于镜面或类镜面。对于汽车涂装各涂层,电泳涂层及中涂层光泽度低,不适用于此方法检测缺陷;面漆层高光泽度及其镜面效果,适用于此法对缺陷进行检测及筛查。
与电磁波、光波和声波信号一样,相位解析法是将图片当作一种信号处理。经过傅里叶变换成正弦波曲线后,通过识别相位的变换,进而识别曲线的变化,以实现缺陷的有效识别。此转换过程涉及模拟量信号以及数字量信号的相互转换,此为视觉检测技术中,算法工程师的主要工作。
图3为图片转换为数字量信号的示意,从左到右分别为:某图片、该图片转换成信号示意图、该信号经傅里叶分布后的正弦图之一及该正弦图转换为数字量信号。

图3 图片转换为数字量信号
3 缺陷识别率的影响因素识别及筛选
无论哪种形式的缺陷检测,均由三大部分组成:①光学系统(含传感器),如相机、透镜及光源等;②图像处理系统,含图像处理库等;③软件及人机界面。其中,硬件部分保证了缺陷的获取,软件及算法对图像进行重建,以确保缺陷的有效识别。
通过对相位偏折法(PDM)原理的分析及了解,结合系统的组成,可以看出,影响汽车涂层缺陷识别效果的因素主要有几下几点:
(1)涂层及缺陷的种类。根据相位偏折法的原理可以看出,非镜面或类镜面的涂层上的缺陷无法检出。可以检出的缺陷是需要引起光线形变的缺陷,因此,涂装的橘皮、打磨抛光痕等无法检出。
(2)光源的选择。根据相位偏折法,显示屏需对漆面进行条纹类光线的投影,采用散射光源,由于其具有多个方向的入射角,可让传感器捕捉到多角度反射光,用于相位偏折的分析及计算依据。一般地,主要采用LED屏或LCD屏,或两者相结合。无法采用激光等单一光源。
(3)产品造型的影响。相位偏折法适用于平面的缺陷检测,对于汽车车身,由于其棱线部位无法构成平面效果,因此,一般地,如果颗粒等缺陷刚好在车身棱线部分,则其检出概率较低。
(4)算法。算法在视觉技术系统的作用类似于人类的大脑,因此,缺陷检测效果的识别率和算法强相关。逻辑完善的算法,可以确保检出率>95%,漏检率<2%,同时具备良好的缺陷分类能力,分类准确率>90%。
(5)相机与光源的相对位置。由于系统需要捕捉光源投射到被测面上的影响,根据光的折射以及散射原理可知,光源与相机的相对位置及角度影响合理设计的情况下,可以有效捕捉到相关反射光线,积累样本量。因此,图像重建流程中,需要对光源及相机的位置关系进行确定及标定,保证相机对于光源的有效捕捉,如图4所示。
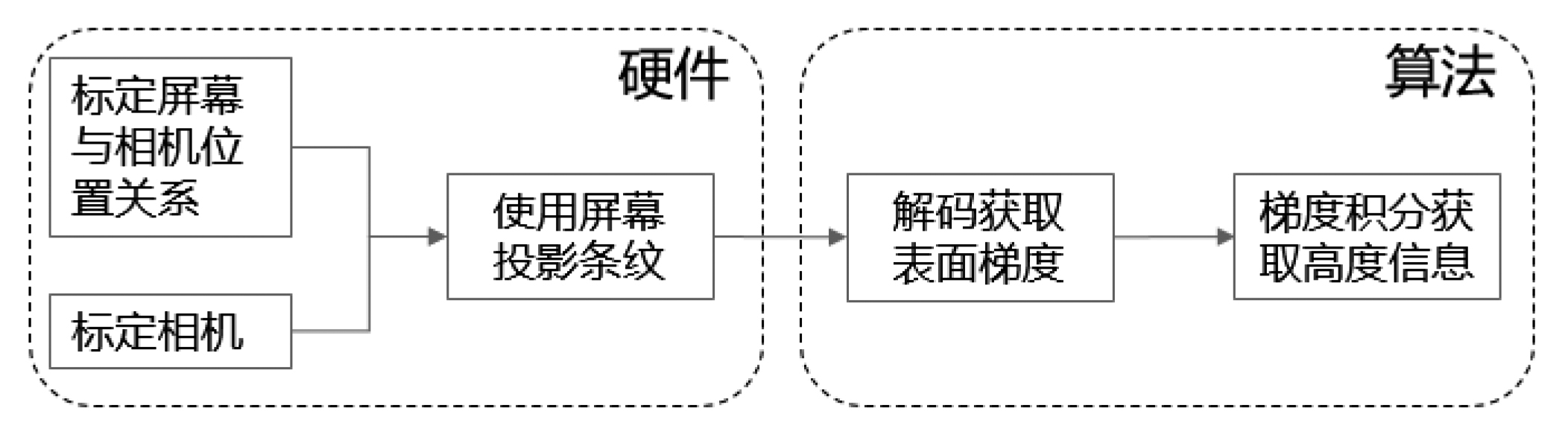
图4 相机与光源的相对位置
4 涂装缺陷检测应用形式及未来展望
目前,在汽车/保险杠行业应用的漆膜检测技术的应用形式主要有两种:一种是机器人+视觉+光源;第二种是隧道钢构+视觉+光源。
其中,机器人+视觉+光源的组合形式,由于机器人动作的灵活性,可应用于车身及保险杠。此种检测方式不受车型限制,可调整机器人轨迹,根据车型外观仿形,以尽可能地保证缺陷的识别率及检出率。由于每个视觉头检测能力有一定的范围,因此,需根据车型大小以及生产线节拍等,配置不同数量的机器人及检测头。一般地,对于30JPH的生产线,需要配置2~4台机器人才能满足此节拍下的检测需求,可适用于走停式或连续式输送线。
对于隧道钢构+视觉+光源的缺陷检测方式,分为车身检测以及尾门检测,其中,车身检测适用于走停式或连续式输送线,尾门检测受检测时间影响,建议采用走停式。此检测方式在最大车身通过范围内,同样不受车型限制,适用于所有车型。但相机的数量及布局,在前期规划时需尽可能地考虑产线上所有车型的特点,以保证一定的缺陷检出率。
此两种形式均在国内外有相关应用案例。部分案例中,还增加了缺陷自动标记、缺陷打磨等设备,实现车身外板的缺陷自动识别及自动处理。
视觉技术的进步、算法的日趋完善以及工业应用的日益增多,此三者相辅相成,可以推进算法逻辑的日趋完善,进而推动视觉技术的进步,有助于视觉技术更好地为工业自动化和智能化服务。
参考文献:
[1] 李大海,王瑞阳,张新伟.基于位相测量偏折术的高精度检测平面光学元件面形的方法[J].应用光学,2020,41(4):844-856.
[2]朱正德.谈“机器视觉”在汽车制造业中的应用[J].中国测试技术,2006,32(5):22-25.
本文为“AI汽车制造业”首发,未经授权不得转载。版权所有,转载请联系小编授权(VOGEL100)。本文作者:张艳芬 李飞 郭家 王云飞,单位:吉利汽车集团有限公司。责任编辑龚淑娟,责任较对何发。本文转载请注明来源:AI汽车制造业
评论
加载更多