0 引言
在机床的切削加工中,表面粗糙度是评价产品表面质量的关键指标之一。缸体作为发动机中最重要的部件之一,既有端面密封要求,也有通孔类O形胶圈密封要求,因此对于密封区域粗糙度有着较高的质量要求。通过调查研究,端面加工过程表面粗糙度不符合质量标准的主要表现为加工刀痕,曲面类加工过程表面粗糙度不合格的主要表现为加工刀痕、加工振纹,因此对于曲面类加工振纹的研究很有必要。
1 试验分析
1.1 试验设计试验材料及设备
试验涉及的材料是某1.5L自然吸气式缸体铸铁毛坯,加工设备为MAGXS211数控卧式加工中心,加工刀具是硬质合金镗刀。
1.2 试验设计
根据缸体表面质量的影响大小,将加工转速、加工进给、刀具长度以及刀具跳动分为高水平与低水平,进行正交试验(具体数据见表1和表2)。
1.3 试验结果分析
1.3.1 加工转速对于缸体表面质量的影响
加工中心干切的过程中,工件表面质量随着切削转速的提高而逐渐变好,表面粗糙度值随着切削转速的提高而变得更小;而此次研究对象的加工过程属于湿加工,即有切削液辅助加工,在一定范围内时,切削转速的提高无法对工件表面质量、表面粗糙度进行有效改善或者提升,由试验结果得出,在一定范围内,提高或降低切削加工转速对通孔表面质量的影响不显著。
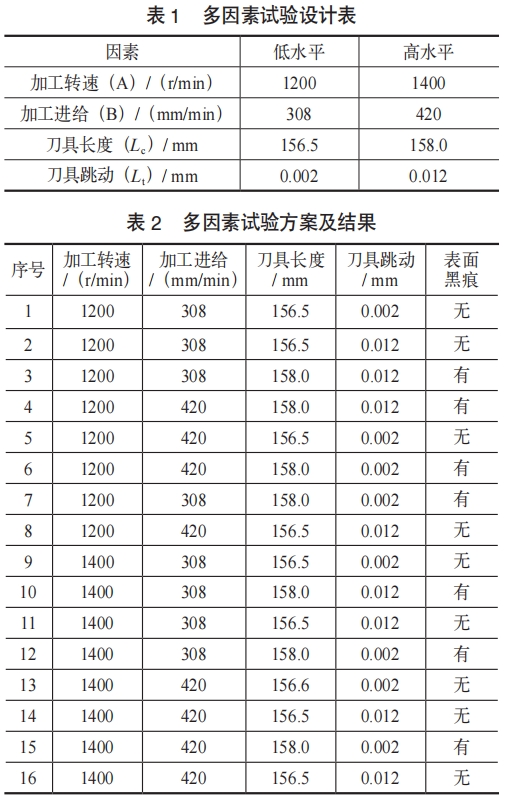
1.3.2 加工进给对于缸体表面质量的影响
切削深度和进给量的增大,都会使切削力增大,工件的变形量随之增大;同时,较大的切削深度及进给量会增大工件的切削残留面积,加剧积屑瘤的产生,从而降低加工精度及表面粗糙度。由试验结论得出,在同一切削转速下,进给高低都会出现表面质量合格和不合格的现象,因此加工进给的增大减小对于此问题无显著影响。
1.3.3 加工刀具长度对于缸体表面质量的影响
加工所用刀具为铣刀,按其长度一般分为长刀、中刀和短刀三种类型,具体长度视加工物料和工件形状而定。一般来说,长刀的长度在150mm以上,中刀的长度在75~150mm之间,短刀的长度在75mm以下。该问题涉及刀具大于150mm,即为长刀。铣刀长度直接决定了加工中所能够切削的深度,因此铣刀长度越长,加工深度也就越深,但是也容易产生加工中的摆动和振动,对加工精度和表面质量造成影响。另外,刀具长度过长也会导致刀具扭曲变形,严重时甚至会断裂。由试验结果可知,当刀具长度在低水平时,无论匹配何种切削参数,均不再出现加工表面不合格的情况,反之,在刀具长度处于高水平的情况下,会100%出现加工表面不合格(图1、图2)的情况,因此刀具长度的长短对于该问题有显著影响。
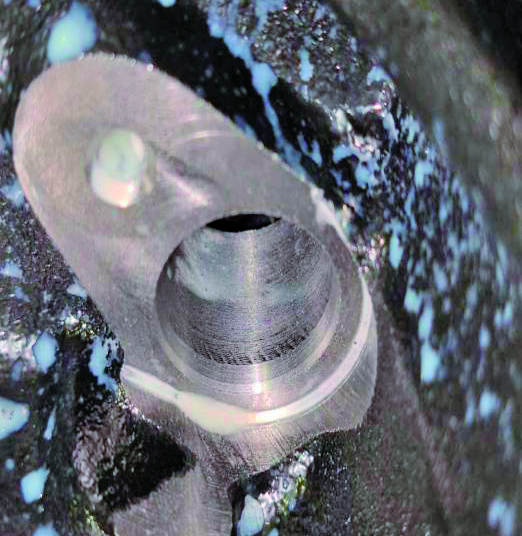
图1 合格通孔表面
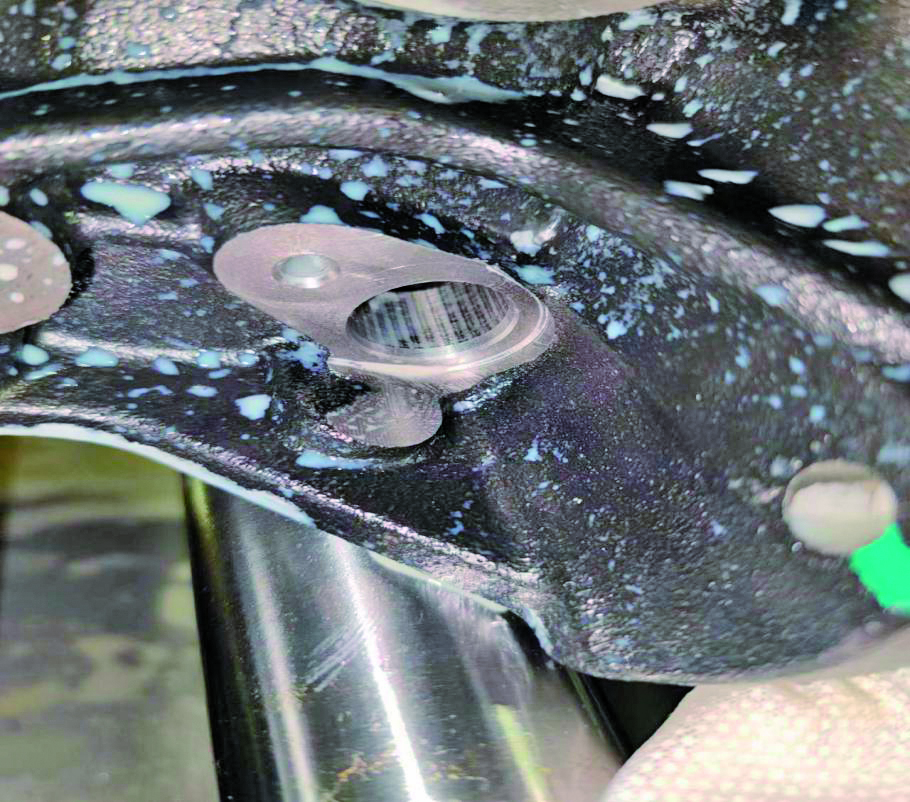
图2 不合适通孔表面
1.3.4 加工刀具跳动对于缸体表面质量的影响
由试验结果不难看出,刀具的各项参数对加工表面质量的影响都是程度不同的,本问题中,刀具跳动对表面质量的影响不显著,但刀具跳动涉及主轴与刀具本身的配合等关系,同样也是影响加工表面质量的关键因素。
(1)刀具产生径向跳动的原因
刀具径向跳动是不可避免的,产生跳动的原因包括加工中心主轴部件的制造误差(不可消除)、刀具(含刀柄与刀杆)不同轴以及刀具自身结构等。
(2)改善刀具径向跳动的具体措施
1)改变刀柄的夹持方式传统的刀杆与刀柄装配主要采用侧面固定式,由于夹持力在侧面且刀柄与刀杆间存在间隙,因此刀杆相对于刀柄中心会产生一定的偏斜。为解决这一问题,最佳方法是采用液压式刀辆或热涨式刀柄,消除装配间隙,同时,夹持力分布均匀,保证刀杆与刀柄的同轴,可有效减小刀具的径向跳动。
2)选择组合式刀具结构传统的刀杆为一体化刀杆,轴心具有较高的直线度,但刀具较重,自重将导致刀杆产生一定的挠度,在加工中产生径向跳动,使加工表面质量不理想。而选择组合式刀具结构,能明显缓解这一现象。组合式刀具是根据实际加工需要由多节刀杆组装而成的,每节刀杆之间采用热涨式刀柄、过盈配合,所以刀杆自身同轴度很高。此外,在满足刚度的条件下,尽量减小刀杆直径,这样既能减小自重和惯性力,从而减小刀杆的径向跳动,又便于排屑。
3)刀头部分增设定位导向块在采用中心钻定位设计时,在刀头部分增设导向块,可以防止刀具加工过程中因切制力不均而引起刀具跳动。
2 结论
用正交试验法对缸体加工表面质量进行研究探索,对影响加工表面质量的各种主要因素进行研究。结果表明,切削参数对铸铁缸体表面加工质量的影响仅在一定范围内有显著影响,而刀具长度、刀具跳动等对表面质量的影响较为显著,因此在保证切削条件、毛坯材料等在较合适水平时,适当提升刀具参数质量是很有必要的。
参考文献
[1]许寒飞,何煦,李扬,等.正交试验设计(DOE)对熔融混炼工艺参数的优化研究[J].信息记录材料,2021(22):10~12.
[2]赵宝爱,杨晓东,李志鹏,等.机械加工表面质量的探究[J].内燃机与配件,2021(17):122~124.
[3]李广,姚远,陈相旺,等.基于全因子DOE的机车抗蛇行减振器布置方式及参数优化[J].中南大学学报(自然科学版),2023,54(05):2074-2084
本文为“AI汽车制造业”首发,未经授权不得转载。版权所有,转载请联系小编授权(VOGEL100)。本文作者:杨鸿翔 林观生 龚顺行 张陈伟 何聪,单位:上汽通用五菱汽车股份有限公司,责任编辑龚淑娟,责任较对何发。本文转载请注明来源:AI汽车制造业
评论 0
正在获取数据......