发动机热试后进气歧管紧固件转矩衰减严重,本文通过对进气歧管结构、紧固件拧紧工艺和转矩衰减特点的分析,发现进气歧管本身质量问题是导致转矩衰减的主要原因,经过改进进气歧管结构和尺寸,转矩衰减问题得到有效控制。
发动机分为汽油机和柴油机,两者进气歧管结构材料不一致,柴油机为铸铝件,汽油机为塑料件。从拧紧技术角度来看,柴油机的进气歧管为硬连接,汽油机的为软连接。软连接结构受热胀冷缩和振动影响较大,紧固件发动机工作过程中容易发生蠕动,导致转矩逐渐衰减,因此,进气歧管的转矩衰减多发生于汽油机上。进气歧管紧固件转矩衰减会导致可燃混合气泄漏,进而导致发动机功率不足、油耗高等问题。
发动机转矩衰减是发动机制造过程中的常见问题,通常由以下3个原因引起:零件结合部位有材质比较软的垫片;拧紧工艺不合理,如拧紧工具和拧紧顺序的选择不合理;紧固件之间叠装有零件。
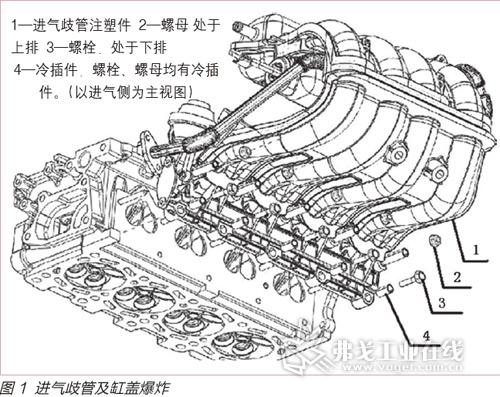
前两个原因引起的转矩衰减,在紧固件被拧紧之后会马上表现出来,热试后更加明显,遵循“先紧易松”原则。第三种情况则与零件承压面的精度和紧固件的选择有很大关系。这3种原因引起的转矩衰减集中发生在某个或某几个紧固件上。但有些转矩衰减的紧固件分布没有规律,这需要结合零件加工质量和受力进行分析。下面以进气歧管转矩衰减问题为例,从零件结构、受力分析和零件质量等方面来阐述转矩衰减的原因和解决办法。
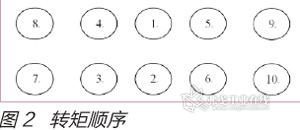
结构及拧紧工艺介绍
1.结构
进气歧管上与拧紧有关的零部件主要有注塑件、冷插件和密封圈,其材料和作用如表1所示。相关零件配合示意图如图1所示。
2.拧紧工艺
(1)人工装配进气歧管到缸盖上(双头螺柱前一工序已拧紧),装螺栓、螺母并预拧2牙。
(2)用气动拧紧枪预紧螺栓、螺母到进气歧管贴合缸盖为止。
(3)用单轴电枪拧紧,按从中间向两边顺序拧紧,图2圆圈中数字为拧紧的顺序。上面一排为螺母,下排为螺栓。
(4)转矩控制要求 动态8~12Nm,静态7~13Nm(以下涉及的转矩值,未特别注明的均为静态转矩)。
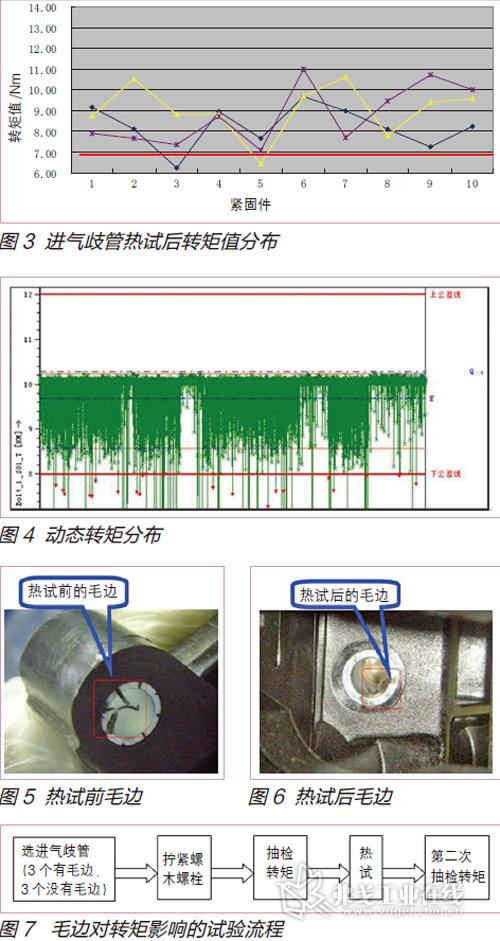
转矩衰减特点
1. 以抽取3台发动机热试后的转矩值为例进行分析
转矩值分布如图3所示,由图可得出以下规律:
(1)热试前,螺栓、螺母动态转矩值分布为9.8~10.5Nm,热试后转矩值均出现衰减,分布无规律。图中两个转矩低于红线的均为螺母,但螺栓也有在红线附近的,83%的转矩值低于理想的静态转矩值10Nm;
(2)不遵循“先紧易松”原则,先拧紧的螺栓和螺母转矩衰减幅度并不大于后拧紧的。
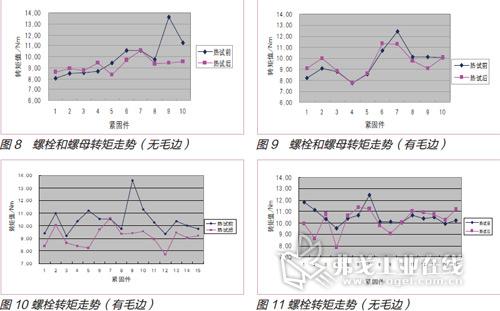
2.动态转矩分析
收集该工位电枪一周的动态转矩值(见图4),平均值为9.7Nm,无明显波动。
因此,进气歧管质量问题导致转矩衰减的可能性较大,现场调查发现进气歧管注塑件的承压面,即冷插件周围有毛边,并且冷插件的高度大于注塑件厚度,这两方面均会导致转矩值衰减。下面分别对这两项进行分析验证。

图12 零件配合关系
毛边对转矩带来的影响
1.毛边对转矩值的影响
毛边主要存在于螺栓压紧的冷插件周围,热试后毛边被压平于冷插件上,具体如图5、图6所示。产生毛边的原因为:进气歧管注塑件的冷插件安装孔内有凸筋,当把冷插件压入进气歧管时,凸筋可以加大冷插件与注塑件的摩擦力,同时,凸筋也会被冷插件挤到注塑件之外,形成图中的毛边。
挑选6台发动机做对比试验,毛边主要集中在螺栓的承压面,螺母较少,所以本次毛边对转矩的影响验证主要针对螺栓来分析。试验流程如图7所示。
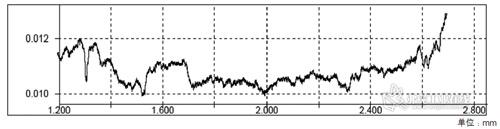
图13 紧固件承压面平面度
2.数据分析
图8、图9为两台发动机的转矩曲线图,前5个为螺母转矩,后5个为螺栓转矩。经对比得出以下规律:
(1)螺母、螺栓转矩值范围不一致,螺母为8~9.5Nm,螺栓为9.5~11Nm;
(2)螺母热试后转矩无衰减,螺栓转矩则出现衰减。
螺栓、螺母的转矩值范围不一致,并且毛边集中在螺栓的承压面,所以螺母转矩值热试前后无明显变化。对抽检的6台发动机螺栓的转矩进行汇总分析(见图10、图11),得出以下规律:
(1)无毛边的螺栓中转矩衰减的比例明显少于有毛边的。无毛边的为33%,有毛边为93%。
(2)转矩衰减的螺栓不集中在特定的部位。
(3)无毛边与有毛边螺栓热试前后转矩值对比如表2所示。
由本次验证可知,经过一次热试,进气歧管注塑件上的毛边会导致转矩为10Nm的紧固件平均衰减1.3Nm。虽然验证表明毛边会导致转矩衰减,但衰减幅度有限,转矩值全部在7Nm以上。经过进一步测量分析,注塑件厚度不合格,也是导致转矩衰减的重要原因。
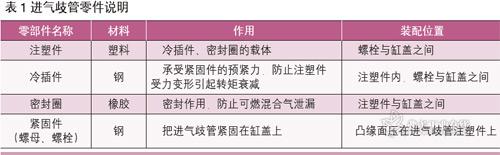
零件尺寸对转矩的影响
1.零件尺寸技术要求(以螺母为例)
零件尺寸技术要求如表3所示。将零件送实验室进行测量,结果为注塑件厚度不合格,平均值为35.0mm,超出下差0.2mm。其余尺寸均满足要求。
根据测量值,可以由公式D1=H注-H冷-D2计算出D1实际为-0.3~-0.2mm,表明冷插件凸出注塑件0.2~0.3mm。
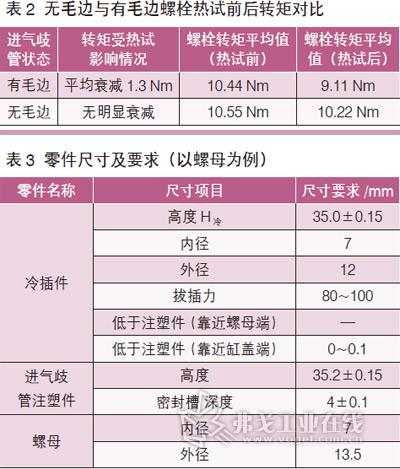
2. 零件配合关系及受力分析
零件配合关系及受力分析如图12所示。从图中可知,螺母拧紧后完全贴紧注塑件,产生的轴向压力大部分集中在进气歧管的注塑件上。注塑件和密封垫有一定形变,注塑件的形变使螺母既压紧注塑件同时也压紧冷插件。因此部分轴向力会分布在冷插件和密封垫上。
由于图中D1与设计要求不符,即冷插件高度高于注塑件0.2mm,零件的配合关系会出现如下情况:
(1)螺母首先接触冷插件,其转矩值为10Nm,根据T=K×F×d公式,其中T为转矩,K为摩擦因数(取经验值0.2),d为螺纹直径8mm,可算出螺栓的轴向力F=6250Nm ,可见F远大于冷插件的拔插力。拧紧过程中冷插件逐渐贴近缸盖,密封垫被压缩,即D1逐渐趋于零。D2则由原来的正值变成负值。
(2)拧紧完成后,螺栓凸缘面将压紧冷插套和注塑件,即D1等于零,密封垫在轴向力作用下产生变形。D2为负值后,注塑件未能完全贴紧缸盖,与缸盖的间隙为D2的绝对值。
3.转矩衰减原因
紧固件拧紧后,注塑件与缸盖之间存在间隙,即冷插件比注塑件高出的值,这个间隙由密封垫填充,因此,轴向力同时分布在注塑件和冷插件上。对紧固件承压面平面度进行检测,承压面外端部分要比中间高出1~2mm,轴向力主要分布在凸出位置,当相邻的紧固件相继拧紧,密封垫不断被压缩,注塑件更加贴近缸盖,原来分布在注塑件上的轴向力变为零,剩余轴向力全部集中在冷插件上。根据T=K×F×d公式,轴向力F减小50%,T同样减小50%(见图13)。
螺母的环形承压面由原来以螺母凸缘面最大直径为外端圆,变为以冷插件的最大直径为外端圆。由公式可知,承压面的面积减少了21%,螺母的抗松能力降低。
结语
根据以上分析,解决进气歧管转矩衰减问题,需保证承压面无毛边,同时冷插件高度低于注塑件。针对这两个原因,可采取下面两项措施:取消注塑件上用于增加摩擦力的凸筋,将圆形孔改为正六边形的孔,用六边形对边与冷插件的过盈配合来保证摩擦力;加大冷插件圆角尺寸,降低冷插件压入注塑件时毛边被挤出来的风险;在注塑件生产过程中严格控制其高度值,保证冷插件两端均低于注塑件。
评论 0
正在获取数据......