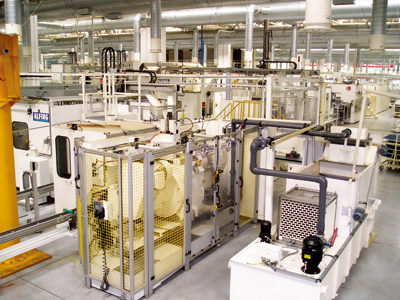
随着机床制造技术的发展,高速、高效及复合化的制造装备逐渐在汽车制造业推广使用。在华晨公司,先进的制造装备确保了高效低成本的连杆工艺方案的切实可行,帮助企业实现高效生产,生产成本也大幅下降。
近年来,随着汽车发动机技术的快速发展,发动机产品的升级更新越来越快,人们对发动机生产提出了新的要求:生产线的生产效率要高、投资要少,同时还要兼顾生产线的柔性及产品生命周期。
华晨1.8T发动机连杆生产线采用了世界先进的生产工艺和加工设备,在保证生产线高效率、高精度的前提下,最大限度地降低了生产线的投资。
高效低成本的工艺方案
华晨1.8T发动机连杆采用了不同于传统的生产工艺,充分体现了“高效低成本”理念:
1. 采用先进涨断工艺,简化工序,减少设备、刀具投资。连杆杆、盖分离采用涨断工艺。涨断后的分离面在装配时完全啮合,不需再进行接合面加工,因而取消了传统工艺中的接合面加工工序。在实际生产中,取消接合面加工不但降低了加工工时成本而且节省了接合面加工所需相关设备(包括工、检具)的投资。
涨断的分离面在连杆与连杆盖装配时完全啮合,不需要增加额外的精确定位,如螺栓孔定位(或定位销),只要两枚螺栓拉紧即可,这样可取消螺栓孔的精加工和定位销孔的加工,减少了加工工时和相关工、检具的投资。
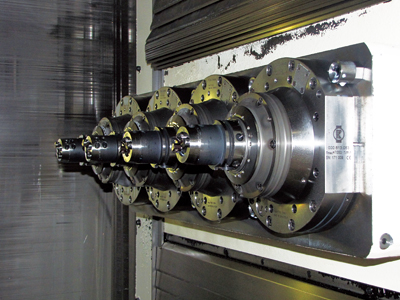
图1 四主轴加工中心
2. 采用多道工序集中加工的方案,在同一设备完成多道工序的加工,减少设备数量,压缩设备投资。采用多工位回转夹具加工中心,配合复合刀具,将除珩磨之外的其他切削加工内容集中在一台加工中心上完成,将生产线上的加工中心数量压缩至一台。
先进装备确保工艺方案切实可行
华晨1.8T发动机的连杆生产线的加工设备仅有四台,双端面磨床、四主轴加工中心、回转涨断机和珩磨机各一台。
1. 四主轴加工中心
由于连杆螺栓孔、大小头孔、大小头精加工等三道工序集中在同一设备进行,加工中心的加工内容多、节拍长,成为连杆线的瓶颈。为扩大加工中心产能,提高生产线的生产效率,同时保证生产线具有足够的柔性,连杆线选用高效率的四主轴加工中心进行以上三道工序的加工。
该四主轴加工中心采用单主轴箱,四主轴同向单排水平排列,联动控制。四主轴同步运动,可同时对四个连杆进行相同内容的加工。
根据加工内容的需要,四主轴加工中心装有四组不同夹具,由工作台翻转变换工位。为便于加工小头11°面,并减小上下料系统的复杂程度,工作台采用垂直翻转方式。四组夹具分别安装在90°、180°、270°和360°四个标准方向上,加工小头11°面时由工作台旋转进行角度补偿,确保工件在上下料工位保持标准角度,简化了机械手的结构和上下料的机械动作,因而减少了上下料辅助时间,提高了设备运行效率。
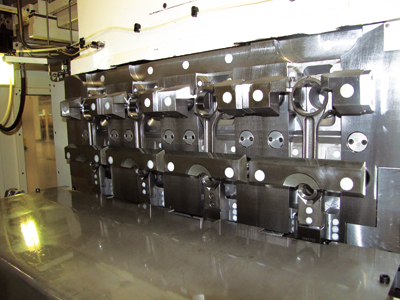
图2 垂直翻转工作台
对应加工中心的主轴数量,每组夹具数量为四个。加工中心同时加工四个连杆,生产效率较普通加工中心提高了三倍,有效地提高了生产线的生产效率。
同时该设备具有工件装载情况记忆功能,当上下料工位的夹具完成装夹动作后机床接收上下料系统提供的工件装载信息,确认该组夹具是否装有工件,如该组夹具未装工件则越过相应工位的加工,提高了设备运行效率。
2. 自动上料系统
四主轴加工中心完成三个不连续工序的加工,完成粗加工的连杆需到回转涨断机和双端面磨床完成涨断、压套等工序后再返回四主轴加工中心进一步加工。精加工工序有三个工位,因此加工过程中有多种状态的工件在各工序和工位间流动,流动过程较为复杂。这就要求有能够及时响应设备的请求,并正确分配工件流向的上下料系统,以确保四主轴加工中心能够高效运行。
连杆生产线配备的自动上料系统包括机械手、两个OP60在制品暂存工位、上料工位、下料工位和工件上(下)行分配器。
自动上料系统具备与四主轴加工中心通信的功能及工件待加工工序检测功能。上料时机械手检测工件状态,并向机床发送指令,将相应夹具移动至上下料工位。下料时机床发送下料工位信息,机械手根据信息将工件送至下料口或相应的暂存工位。
3. 双端面磨床
双端面磨床用于进行端面粗、精磨两道工序的加工。由于这两道工序的加工节拍都远高于其他工序,在正常生产的情况下这两道工序均可为下序准备充足的在制品,因此,两序间的切换未采用自动方式,而是采用手动切换。
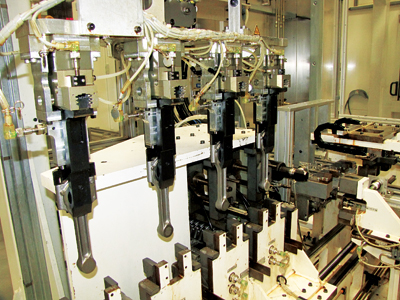
图3 上料机械手
工序切换时需调整砂轮位置,设定磨削厚度,并调用相应的控制程序对工件检测及下料分配器的位置进行设定。由于切换过程采用手动控制,简化了设备控制系统,从而使设备造价大幅降低,进一步减少了生产线投资。
结语
由于华晨1.8T发动机连杆生产线采用了先进的加工工艺,缩短了工艺路线,减少了设备投资,设备折旧成本大幅降低,因此产品的生产成本也大幅下降。且由于工艺路线短,连杆生产线全线仅有六台设备,占地面积小,为生产线的扩容预留了充足的空间。多工序对应一台加工设备的工艺设计不但压缩了生产线的投资,而且提高了设备的使用效率,使设备的折旧期更接近产品的生命周期,使产品更新换代时可根据具体情况选择设备改造或更换设备,为生产线的技术升级创造了有利条件。
评论 0
正在获取数据......