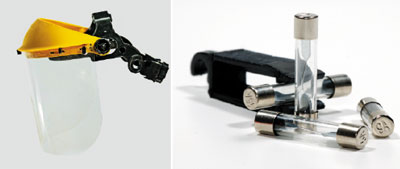
图1 V6CB线流程图
在发动机缸体线库存管理中,应用Pareto图以及其他统计方法找出造成目前库存状况的原因,进一步应用库存管理策略以及其他分析问题工具提出降低目前库存的方法,根据分析结果对生产线采取相应的措施,重新设置缸体线的安全库存量,可节约库存成本并提高生产线的运营效率。
SGMPT V6CB线是一条加工V6发动机缸体的自动生产线,目前主要加工两种型号的发动机缸体(LNJ和LW9),其生产流程图如图1所示。
此生产线之前因为没有对安全库存进行过科学的计算,在实际生产运营过程中存在以下问题:
1.因生产两种类型的产品(LW9和LNJ),加工批量不明确,制定的批量计划缺乏科学性,有时候两个星期转型一次,有时候两天转型一次,但每次转型时间都是一样的,即生产准备时间相同。
2.有时候因为库存量过小,一旦设备故障停机将影响发动机装配线的生产;但大部分情况为了不影响发动机装配线过量生产使得库存量非常高,造成了运营成本偏高从而引起很大的浪费,缸体库存量最高达到6000只。
3.生产系统不够稳定造成了生产交货间隔期(MLT)过长,缺少对MLT过长原因系统的分析,使得PM计划以及其他工作缺乏针对性,从而无法设置安全库存量。
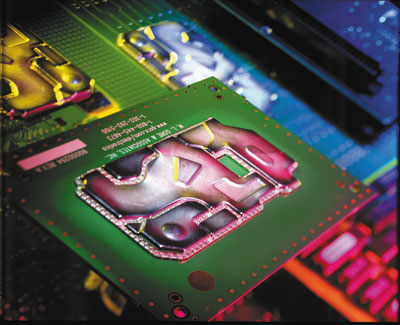
图2 批量-产能曲线图
生产经营管理概念的应用
V6CB从上面现状的描述及图1中可以看出它是一条很复杂的生产线,因设备故障、人员组织安排和加工刀具等都有不确定性,为了保证正常的生产必须对这些不确定性做出最佳的预测。首先,必须对此生产线的产能重新评估(批量-产能);其次,生产线的不确定性可以用安全库存(SS)来弥补。
从上面的描述可以看出,在本文中至少要用到生产经营管理概念中的批量-产能的概念以及安全库存(SS)的概念。
生产批量的确定
V6发动机装配线的需求量是368台/班次,V6CB线批量处理时间、单位处理时间以及每班次的生产时间等信息见表1。
因V6CB线生产加工两种型号的发动机缸体,两种型号缸体之间的转型时间即批量准备时间为120min,如果不存在转型,此加工线的生产能力为375台/班次,为了跟上装配的节拍(368台/班次)必须要合理地安排转型频次,即要合理地安排批量。如图2所示,批量至少为5000才能满足要求。
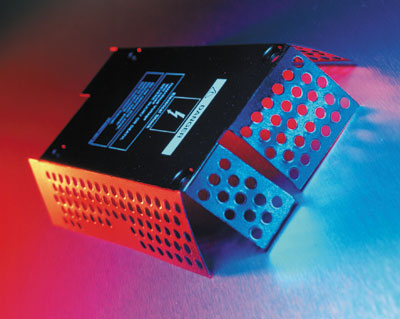
表1 V6CB线基本信息
安全库存的计算
安全库存(SS)规模取决于:所需的安全水平即安全系数(Z);现有不确定性水平即V6CB线产量的标准差(SD);易损期(VP)长短即V6CB缸体的盘点间隔期加上生产交货间隔期(MLT)。
1.易损期(VP)的确定
生产交货间隔期(MLT)分析以及改进:从安全库存的计算公式可以看出,如果安全系数以及SD不变,则必须要降低VP;如果盘点间隔期不变则必须要降低MLT。接下来我们对V6CB线的MLT进行分析。MLT主要由5个部分组成,即MLT=输送及加工时间+设备故障时间+换刀时间+测量时间+生产准备时间,表2为今年1~3月份MLT的平均值,从中可以看出来MLT大约为3.3个班次。

表2 1~3月份MLT统计表(均值)
MLT中的输送及加工时间、测量时间以及生产准备时间受现有机床特点以及质量控制规范的要求进行改进的可能性不大,接下来重点对故障时间以及换刀时间进行分析以及改进。
如图3所示,设备故障停机时间较长主要集中在OP70/OP75,且OP70/OP75机床结构、机床PM计划以及机床加工内容都基本上相似(但跟其他工位的机床完全不同),运用鱼刺图对OP70/OP75故障停机进行分析,得出OP70/OP75停机的原因主要是:OP70/OP75换刀故障;OP70/OP75机械手撞顶门;OP70/OP75上下料机械手之间碰撞。
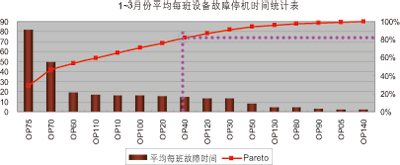
图3 1~3月份平均每班设备故障停机时间统计
小组成员把目光全部集中在上述故障上面,对这些故障进行了深入的分析研究(见图4),并采取了下列措施:
(1)OP70/OP75换刀故障:经过对换刀机构的系统全面分析后发现,逻辑程序不够严谨是造成换刀故障的主要原因,然后对逻辑程序进行了相应的修改,增加了逻辑程序上的互锁,从而保证了换刀过程的正常进行;
(2)OP70/OP75机械手撞顶门:主要是顶门机械结构故障引起传感器信号错误,然后对顶门进行了重新设计并对顶门进行了改造;
(3)OP70/OP75上下料机械手之间碰撞:主要是因为两个机械手之间互锁的逻辑不是非常严密,然后对机械手的程序进行了修改。
以上措施全部就位后预计OP75的停机时间可以从每个班次的82min降低到28.27min,OP70的停机时间可以从每个班次的50min降低到21.966min。
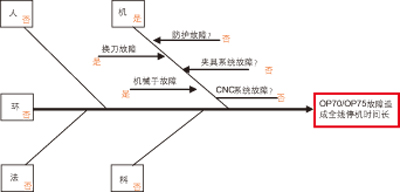
图4 停机分析鱼刺图
图5为1~3月份各个班次上的换刀时间统计情况,从图中可以看出换刀时间最长的为OP100。
运用鱼刺图对OP100换刀时间长的原因进行分析(见图6),发现OP100换刀时间长主要是因为OP100上多个工位的刀片寿命偏低造成在生产过程中要频繁换刀片,这些工位为:Sta3、Sta9和Sta18。
Sta3、Sta9和Sta18加工过程中所使用的刀片是完全一样的,而根据上述分析小组成员决定提高刀片寿命是降低换刀时间过长的最好方法,提高刀片寿命最好的方法是选用带涂层的刀片,最后小组成员一致认为Sta3、Sta9和Sta18全部选用带涂层的刀片。以上措施就位后,预计OP100每班次的换刀时间可以从83min降到52.5min。
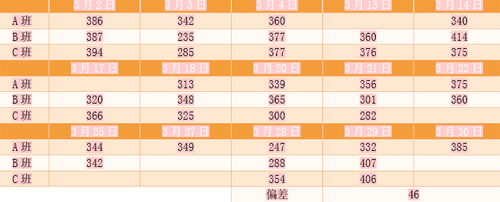
表3 标准差
如上述设备改进措施以及刀具优化措施到位,预计MLT将从3.3个班次降低到2.9个班次。
盘点间隔期:以前盘点间隔期平均为18个班次,即1个星期盘点一次(平均每个星期盘点一次),为了降低VP,建议每个班次对V6CB线的缸体盘点一次。
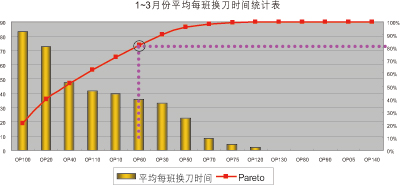
图5 1~3月份平均每班换刀时间统计
2.安全系数以及标准差
表3是根据3月份每个班次产量计算出来的标准差(SD)=46;
取安全系数Z=3,则断货概率
;则每年断货次数=断货概率×每年的班次数=0.13%×(365×6/7×3)=1.3次。
以上按照每年365天,每周6天且每天3班生产,进行计算。
取得的结果
通过对批量-产能以及库存的分析取得了如下结果:
1.明确了生产线的生产批量,至少为5000只,即明确了生产线转型的安排。
2.通过对生产线进行改进和优化,预计MLT将由3.3个班次降低到2.9个班次。
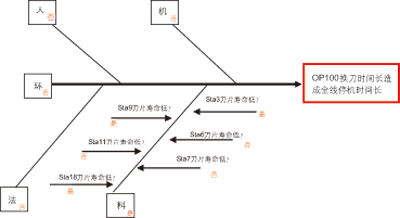
图6 换刀分析鱼刺图
3.生产线最高时候库存为6000,如不对生产线进行改进,则每种型号缸体安全库存可以设置为两种型号缸体则为1274只;对生产线进行改进且重新调整了盘点间隔期后,预计每种型号缸体安全库存可以设置为,两种型号缸体则为544只。
结语
通过运用生产经营管理方法,我们对SGMPT V6CB线进行了系统的分析并对生产线进行了适当改进:通过分析,明确了生产线发动机缸体的生产批量,避免了批量不明确所带来的运营成本的提高;运用库存管理策略重新设置了安全库存量,预计库存量可由最高时候的6000只降到544只;如果安全库存量为544则可以计算出每年的断货次数为1.3次,生产线以及客户可以接受此安全库存的安全水平。
评论 0
正在获取数据......