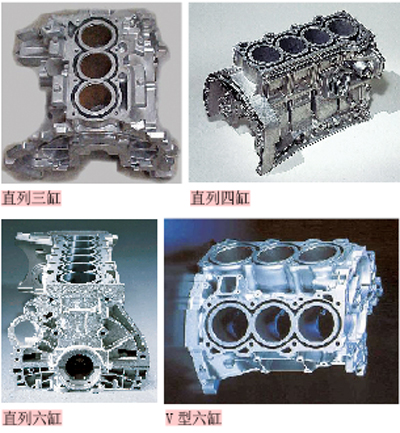
图1 常用汽车缸体
采用缸体压铸方式生产发动机缸体,可缩短工艺路线,提高生产率,具有明显的技术优势和经济优势,尽管这一生产方式存在个别的缺点,但随着压铸工艺水平的不断提高,人们将不断克服,缸体的压铸生产已逐渐成为新的发展趋势。
缸体压铸特点
随着人们对环保、轻量化的要求日益提高,汽车中的许多关键部件,如发动机缸体等,逐渐转向采用压铸生产。
相比传统的铸造,压铸缸体有以下优点:
1.效率高。在所有的铸造方法中,压铸是一种生产率最高的方法,这主要是由压铸过程的特点决定,且随着生产工艺过程中机械化、自动化程度的进一步发展而提高。生产一个缸体的时间一般为3min左右,相对传统的低压或者砂型铸造省时省力。
2.精度高。只需个别部位加工即可使用。
3.铸件的强度和表面硬度较高。
4.节能省耗。一般每台设备每年可生产7万件左右。
5.占地面积少。
6.工艺路线短。传统的铸造工艺,缸体生产需要经过造型、制芯、浇注、冷却、落砂、清理、机加以及热处理等诸多工序。而压铸则只需提前加工模具,浇注后很快将缸体毛坯铸件从压铸岛(压铸机和各周边设备一起统称为压铸岛)中取出,或者由人工去除飞边毛刺,之后进行检验、加工等即可。
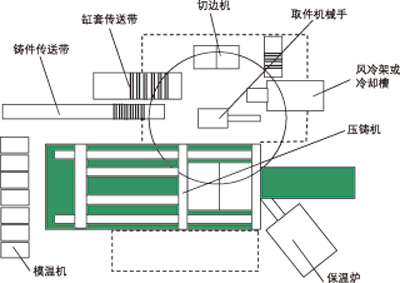
图2 压铸岛的典型布局
压铸也存在一定的缺点:
1.铸造缺陷较多。由于液体合金充型速度极快,型腔中的气体很难完全排除,常以气孔形式存留在铸件中。另外,压铸填充过程中的氧化夹杂等,如果集渣包等设计不合理,容易残留在产品内部。
2.压铸初次投资较高。据统计,如果生产的缸体数量低于10万个,低压铸造或砂型铸造的成本低于压铸。
缸体样式及压铸岛布局
排量在2.0L以下的汽车缸体一般为直列三缸或四缸,而大于2.0L排量的缸体则可能为直列六缸或V型六缸。图1所示分别为汽车的直列三缸、直列四缸、直列六缸和V型六缸缸体的外形。
目前来讲,一般的压铸岛布局比较复杂,而且没有标准的布局格式。每个压铸厂家都会根据自己生产的经验和特点提出一些与众不同的布置,从而方便生产。压铸岛的基本周边设备一般如下:
1.压铸机,吨位从2200~4 400t不等,主要由产品投影面积和增压压力决定。
2.铝合金融化炉,或者铝合金保温炉,吨位一般在2t左右,由产品重量和生产节拍决定。
3.喷涂设备,采用双轴式喷涂或机器人喷涂,喷嘴的布局和喷头结构要求高,要能保证喷涂的质量;脱模剂的容器需要足够大,否则脱模剂添加过于频繁。
4.取件设备,一般采用机器人取件,因为轴数太少,普通的简单取件手不能满足要求,且无法实现自动化运行。
5.风冷架或水冷箱,根据不同厂家的要求、经验和缸体的特点而定。
6.切边机,用于去除集渣包和浇道等。
7.缸套输送带,缸套作为镶嵌件需要用输送带送达相应位置,由机器人放入模具。
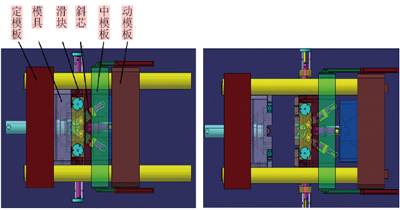
图3 V型缸体生产原理
8.模温机,因为缸体生产对模具温度要求很高,模温机不可或缺。
压铸岛的布局可以各式各样,图2所示为一典型布置,仅供参考。
V型缸体的生产
国内目前还没有采用压铸方法进行V型缸体生产的厂家。V型发动机缸体主要是缸套部分的抽芯比较困难,其余部分和直列的缸体没有太大的区别。比较简单的解决方法是在动定模板之间添加第三块模板,且称为中模板。中模板和动模板之间用液压连接。开模时,先打开动模板,然后抽芯,然后再打开中模板。之后上下左右滑块打开,这样就可以顺利把缸体从模具中取出。
图3所示为某V型缸体生产原理示意图,按照图中所示原理,欧洲、美国、韩国等地区和国家已经实现了V6缸体的压铸生产。
压铸工艺要点
首先,应该合理设计缸体压铸件的浇注系统。通常缸体压铸件的浇注系统有两种形式:单侧浇注系统和双侧浇注系统。单侧浇注系统一般用于小型缸体,双侧浇注系统一般用于大型缸体。浇注系统应注意沿金属液流动方向逐步缩减,以减少气体卷入。齿形激冷排气块排气集渣效果良好,获得广泛使用。齿形排气道的厚度大致控制在0.6mm以下。
缸体压铸件质量对压射工艺参数的变化非常敏感。速度过高容易造成铸件中的气体增加,过低则容易造成充填不良现象。压射压力过低,铸件中气孔、缩孔等缺陷增加;压力过高,飞边及毛刺等增加,对模具损害也大。压铸过程中应十分小心调整工艺参数,采取合适的压射速度,确定合理的速度转换位置,使型腔中的气体尽量排出,使残余气体在铸件内部呈弥散分布状态,而不至于穿透铸件断面,形成泄漏。此外,应注意及时增压,在凝固之前对铸件进行有效压实。实际上,缸体尺寸大、结构复杂、壁厚差异大,很难选取一个好的工艺规范。通常,缸体压铸的慢压射速度控制在0.2m/s左右,快压射速度控制在3~5m/s;或者填充速度控制在30~50m/s,压力一般不低于70MPa。
缸体压铸对压铸温度更为敏感。对于常用合金,金属液的温度要控制在640~680℃之间,模具的温度喷涂后控制在150~200℃之间。要使用模温机对模具温度进行控制,实际上,模温机已成为缸体压铸中不可缺少的辅助设备。同时要设置足够的冷却/加热管道,保证对模具温度的有效控制。推荐采用独立进、出水冷却方式并且可调,冷却水可以按要求流量直接到达要求冷却的部位,充分发挥冷却作用。动定模温差不能过大,否则容易造成铸件热应力增大,出现开裂现象。
另外,脱模剂对缸体压铸至为重要。好的脱模剂除可以控制模具温度分布外,还可以减少开模时的摩擦力,避免粘模现象发生。尤其在模具温度偏高时,更应注意脱模剂的合理和有效使用。
除了前述各因素外,合金液的质量也不可忽略。应充分注意合金液质量,避免合金污染,必要时应进行除气和精炼处理。真空方法也是缸体压铸一个有效的质量保证措施,但会增加额外工序。目前,许多压铸厂在生产缸体时未采用真空方法,也能压铸出合格产品。
缸体压铸件的缺陷主要包括气孔、缩孔、冷隔、裂纹和夹渣等,严格遵守工艺规范及操作规则是控制缺陷产生根本手段。
结语
缸体的压铸生产有其自身的优缺点,但在技术和经济上具有明显的优势。它不仅能达到较高的生产率,而且从材料至成品的整个生产过程也表现为最短。由传统铸造方法转向压铸法生产铝合金汽车缸体已经成为一个发展趋势,仅2008一个年度,国内不同厂家由布勒公司引入了7条2 700t级别的铝合金发动机缸体生产线。由此可见,我国汽车缸体压铸生产规模在逐步扩大,水平在提高。
评论 0
正在获取数据......