
图1 中型变速箱壳体
变速箱壳体具有复杂的结构,面对多品种小批量定单化市场需求,如何实现高效、高柔性、高精度和低成本的变速箱壳体加工,东风汽车变速箱有限公司对壳体生产线规划做出了有益的探索。
产品结构特点和技术要求
变速箱箱体形状复杂,具有较多的孔系,壁薄、呈箱形(见图1、图2),其表面具有多处需要孔系加工,如箱体上的轴承孔、定位销孔、螺钉连接孔以及各种安装平面直接影响着变速器的装配质量和使用性能。因此,变速器箱体加工具有严格的技术规格要求。如:轴承孔的尺寸精度一般为IT6~IT7,表面粗糙度Ra1.6mm,圆度、圆柱度为0.01~0.012mm,各轴承孔的中心距公差0.05 mm,同中心线上的轴承孔的同轴度公差为0(M),主要装配表面(上盖结合面、前后端面)的平面度公差为0.1mm, 表面粗糙度Ra3.2mm,主要装配表面间的垂直度公差为0.1mm。
现有生产线现状
我公司现有变速箱壳体生产线基本情况见表1。

表1 现有生产线基本情况
1.现有生产线通过品种及市场需求
我公司现有产品多种类型,DF5S300轻型、DF5S420-DF6S900中型及DF6S1100-DF14S1600重型变速箱,有变速箱壳体1700K1-025、NB-025、NT-025、T-025、ND-025、KF-025、KBA-025及Z-025等多种型号产品,每个产品市场需求量从5 000~40 000不等。
2.现有生产线能力状况
变速箱壳体生产线能力只有4.2万,能力缺口主要依靠外制解决,变速箱壳体生产线瓶颈工序加工时间长(45 min),现有生产线布局的为机群布置,生产线物流方式为物流小车,零件的物流路线长。
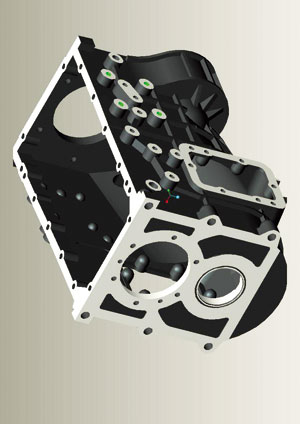
图2 重型变速箱壳体
新生产线规划
现有变速箱壳体生产线为立式加工中心和卧式加工中心组成的多品种混流生产线,生产线柔性化可以适应公司现有产品现状,但生产线瓶颈工序加工时间长,生产线节拍长,产能缺口大。
现有变速箱壳体生产线主要有两种,一种是组合机床自动生产线,另一种是加工中心生产线。组合机床自动生产线为多轴加工,生产效率较高,生产品种单一,零件加工成本低,生产能力大,不能满足多品种混流生产。加工中心生产线为单轴加工,生产效率较低,可以满足多品种混流生产,但生产能力不足。
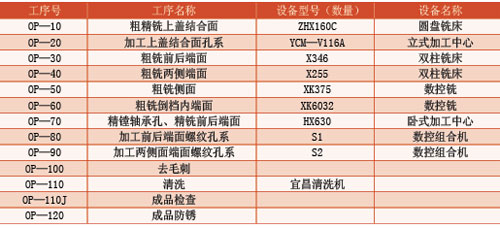
表2 变速箱壳体生产线主要加工工艺流程
变速箱壳体主要的工艺流程见表2,新的生产线规划如下:
1.生产线布局方案
采用普通设备、专机型加工中心机床和数控组合机床组合布线。
2.生产线物流有两种方案
方案一:生产线采用智能托盘安装零件,动力滚道按工位移动,零件上安装识别芯片,自动扫描芯片,加工中心识别芯片信息自动识别加工零件品种,调用加工程序。其特点是效率高,但投资额大。
方案二:生产线采用滚道连接,生产线采用直线布局和并列布局相结合的方式,并在分线合线处采用滚道,工件上、下料采用手动方式,输送工件的滚道布置在设备上下料的一侧。该方案效率较低,但投资额小。
相比较,采用方案二,更适合中国国情。
新生产线的规划特点
1.生产形式特点
生产线采用“普通设备+加工中心+数控组合机床”结合组成的混流线柔性生产线可以充分发挥组合机床和加工中心的优势,实现了组合机床的高效率与加工中心柔性化的统一。
2.缩短瓶颈工序加工时间
变速箱壳体生产线瓶颈工序加工时间由45min/件降到9min/件,降低了全线节拍,大幅度提升了产能,零件单件加工成本降低了30%。
3.主要加工工艺流程
变速箱壳体属于薄壁类零件,壳体零件刚性差,在装夹时容易变形,粗精加工分开,即在主要平面和各支承孔的粗加工之后再进行主要平面和各支承孔的精加工。这样,可以消除由粗加工所造成的内应力、切削力、切削热和夹紧力对加工精度的影响,并且有利于合理地选用设备等,提高产品加工质量。
4.与传统的组合机床加工线比较
新生产线工艺路线大幅缩减,由原来的29道工序缩减为9道工序,减少了机床的占地面积,减少了零件搬运过程中的磕碰。
5.设备选型方面特点
精加工设备关键工序采用准高速加工中心。采用的高速卧式加工中心,主轴最高转速8 000r/min,快速移动速度高达60m/min,进给速度可达50m/min,换刀时间(刀-刀)为3.5s。粗加工设备采用选择高刚性、大切削力的专用铣床,实现高效重切削加工,变速箱壳体外壁复杂加工表面采用高刚性数控卧铣加工。四面螺纹加工原工艺采用加工中心,占用了大量加工时间,新生产线采用数控组合机加工,根据零件品种不同,可快速更换多轴箱,缩短了生产节拍。
评论 0
正在获取数据......