
图1 方案1示意图
发动机工厂箱体类零件加工多采用加工中心进行生产,加工设备选型和生产线的组线方案是否合理直接关系到产品质量、生产效率和后期维护成本。本文以缸体生产线为例,同时结合奇瑞公司新发动机工厂运作模式,对缸体生产线的设备选型和组线方案进行分析,并提出了相关建议。
目前,消费者对轿车的要求越来越高,不仅要求空间大、外观漂亮,更对发动机的油耗和动力性能提出了更高的期望。为此,各大汽车厂商在研发发动机时,广泛采用了新技术和新工艺来降低油耗并提升动力,如双VVT技术、增压技术及燃油缸内直喷技术等。
汽车制造业是典型的大批量生产模式,通常采用自动化程度较高的流水线,同时为了满足低油耗、强动力的设计要求,在生产设备选型中大量采用了高精度、高质量的数控加工中心。加工设备的质量直接决定了产品的稳定性和生产效率,只有选择适合的机床品牌和型号,并结合工厂实际情况和设备特性,采用适用的组线方案,使设备性能充分发挥,才能高效率地制造出优质产品。

图2 方案2示意图
设备选型因素
为了保证发动机的优良性能,首先,要保证产品的精度满足设计要求,缸体、缸盖形状复杂(壁薄、多空腔和多孔系)、结构特殊,对孔、面精度要求较高。其次,在生产线前期规划时需考虑产品一致性、生产效率及后期维护成本,因此,在所有的发动机生产线中,箱体类零件如缸体、缸盖及框架等大多采用数控加工设备进行自制。我公司经过长期的实践验证,采用了大量国外诸如德国、日本等先进数控加工中心,该类设备精度较高,加工质量稳定,故障率低。我公司已有设备开动率为70%左右,新工厂通过引入先进设备预计可以达到80%,设备开动率的提升将大幅提高生产率,降低成本。
1. 加工中心的种类
加工中心大体可分为立式加工中心和卧式加工中心两种。卧式加工中心按照分类方法不同,可分为几种不同类型:
按进给方式分为两种类型:主轴进给和工件进给。从结构上来看,工件进给类型的加工中心将三轴复合运动进行了分解,主轴框架结构得以简化,刚性好,稳定性要高于其他类型机床,机床体积缩小,后期维护方便;其缺点是快进速度慢。主轴进给类型相比工件进给类型具有较高的快进、后退速度,机床可以很好地满足节拍要求,故在切削力较小时,使用主轴进给可以节省时间。

图3 U形与直列排布对比
按轴数不同,可分为三轴两联动、五轴四联动等。轴数越多,造价越高, 对于缸体、缸盖等箱体类零件,三轴两联动已满足要求。
按主轴头数,分为单主轴头和双主轴头两种。双主轴头可实现同时加工两个工件,效率较高,如GROB的G系列卧式加工中心,但相对单主轴头,维修复杂。
按工作台数量,常见的有单工作台和多工作台两种。对于小型箱体类零件,单工作台和双工作台常见。双工作台可实现一个工作台加工,另一个工作台进行装卸作业,可充分利用机床辅助时间提高生产效率。
2. 加工中心的规格与参数
加工中心的规格包括X/Y/Z轴行程、主轴转速、进给速度、快进速度及刀库容量等,参数包括静态精度、定位精度、重复定位精度、加工精度、热变形状况和抗振动性能等。如何根据实际需要和投资额选择合适的加工中心,成为技术人员面临的难题。
许多机床厂商提供“交钥匙工程”,但汽车厂需要对设备厂家的方案进行确认,依然需要技术人员进行判别,并选择合理的方案。根据工件材质的不同,应采用不同的加工方法,例如铸铝件,由于其硬度低,可采用主轴转矩较小的加工中心,并使用较高的主轴转速;对于灰铸铁件,其硬度高,难加工,宜采用较低的加工速度,因此选择低速高转矩的加工中心。

图4 极限塞规与综合检具
3. 合理选用专机
加工中心具有通用性强,换型方便等优点,但却不能满足大批量流水线生产所追求的质量高度一致性的目标。合理选用专机可以提升加工质量,降低生产成本,同时还可以弥补刀具的一些不足之处。加工中心与专机配合使用,可以起到刚柔并济的作用。下面以缸体的曲轴孔加工方式为例进行介绍:
方案1:加工中心方案。受制于刀具长度和刀具旋转精度,一般分粗镗、精镗两步,粗镗分两次加工,第一次加工两档,工件旋转180°加工另外两档;精镗刀分为两把,第一把加工出第1、2档,然后以第1、2档为导向,用另一把长镗刀加工出剩余两档,如图1所示。
方案2:专机加工方案。专机镗刀长度不受限制,可根据加工需要定制长镗刀,镗刀两端加装镗刀架,可以很好地保证加工精度;并且可以在一把长镗刀上安装粗加刀片和精加刀片,实现一次进刀,完成粗、精镗两道工序,如图2所示。

两种加工方案的利弊如表1所示。
4. 成本因素
在生产线规划初期,必须要考虑投资成本,需要核算投资回收周期,机床自动化程度越高,相应的投资也越大,工人劳动强度越小,对工人操作熟练性要求低。如今我国的人口红利优势正在逐步消失,人工成本问题需要进行重点考虑,因此,采用自动化程度高的设备,减少操作工人数量是符合公司长远利益的。同时,需要兼顾考虑投资成本,对各个方案进行比对,找到合适的平衡点,以争取用最少的投资获得最大的收益。
5. 其他因素
数控机床常用的数控系统有FANUC和SIEMENS两种,FANUC进入中国时间较久,拥有广泛的客户;SIEMENS开放性好,在大量高端机床上被采用,欧洲机床多采用该系统。目前,这两种系统在我厂都有应用。可根据企业实际情况,选用本企业员工熟悉的系统,减少磨合时间,防止出错。
生产线投产后,设备不可避免地会发生各种故障,而且一旦关键工序的机床发生故障,就有可能导致停线,损失严重。设备厂商的响应速度和售后服务质量,无论是对工艺规划人员还是最终用户来讲,都是一个需要考虑的重要因素。

生产线的组线方案
1. 组线形式
传统的生产线排布方式为直线排列,如图3a所示,现在大多企业采用U形或十字排列方式,如图3b所示。U形排布非常紧凑、可实现一人操作多台机床,还具有占地面积小,人员走动距离短等优势,同时考虑到市场变化和投资风险,可采用分期投资和设备分步实施。但其不足是维修空间小,作业机械不易进入。总体来说,生产线采用U形布置优势明显(见表2),故我公司缸体线在对比了各种方案后最终采用了U形布置,通过采用此方案可提高每人年生产率30%左右。
2. 工件上下料方式
对于机加工生产线,工件上下料方式可采用自动和人工两种方式。采用机械手或机器人可实现无人化工厂,操作员数量少,劳动强度降低,但相应的投资较高。采用人工上下料方式,工人劳动强度较大,同时对于铸铁件等较重工件,需要配备吊具进行操作,增加了安全隐患。为了更好地控制投资成本,并结合工厂实际情况,我公司缸体线采用了折中的方法,采用人工推拉料方式进行作业,减少了工件上下搬运,从而杜绝磕碰和划伤,保证了自制件的产品质量,可减小50%左右工废率。
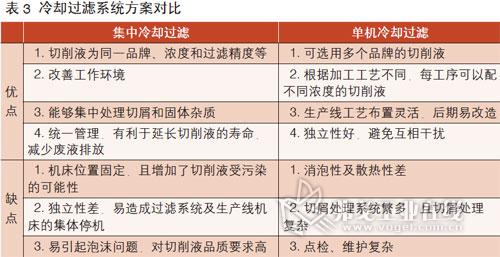
3. 质量控制方式
生产线量检具配备方案是前期规划的重要任务,对于产品的关键尺寸需要配备在线检具进行质量抽检,并能进行数据汇总分析,便于过程监控。同时,需要考虑极限塞规的布置,做到方便取用且降低误碰率。使用在线检具与综合检具相配合的方案,如图4所示,能减少三坐标测量项目,从而达到减少检测时间和设备待机时间的目的。
生产线规划初期就需要考虑质量追溯要求,对于多工序、多单元生产和多品种共线尤为重要,在工件上打印流水号,能起到发生质量问题时可以在最短时间里找到问题根源的作用。
4. 切削液供应方式
对于整线的切削液供给方式也是初期规划考虑的重点。切削液供给有两种方式:集中冷却过滤供给和单机冷却过滤供给。对于较大产能的生产线,采用集中冷却过滤系统成本较低,同时维护方便,两种方案的优缺点如表3所示。
结语
在机加工行业,特别是发动机厂机加工线需要购置大量加工设备,一次性投资较大,故在发动机生产线规划筹建时,需要权衡利弊,综合考虑。
本文内容结合我工厂缸体线组线的具体情况,对加工设备的选型和生产线规划工作进行了重点分析,希望能为发动机箱体类零件的加工线初期规划提供借鉴和参考。
评论 0
没有更多评论了