机加工生产线布局设计是制造工程规划设计的重要内容之一,生产线布局的精益程度对于提高生产效率、产品质量以及资源利用率至关重要,进而达到降低运行成本、提高经济效益的效果。本文针对机加工生产线如何进行精益布局设计进行了探讨。
生产线布局问题是现代企业发展中面临的重要课题之一,精益规划生产线设备布局,如何在最短的时间内以最低的成本生产出符合市场需求的产品,将是决定企业在激烈的市场竞争中持续发展的重要保证。
在我公司40万台发动机新基地建设中,我们参考丰田生产方式,通过运用精益生产的基本原则、理论及方法,实现了“一个流”生产。发动机5C件生产线设备按照U/C型布置,有效改善了作业组合,减少了工序间在制品零件的数量;减少了走动时间和搬运的浪费;提高了生产效率,实现了精益化生产。发动机5C件加工线及装配线布局如图1所示。
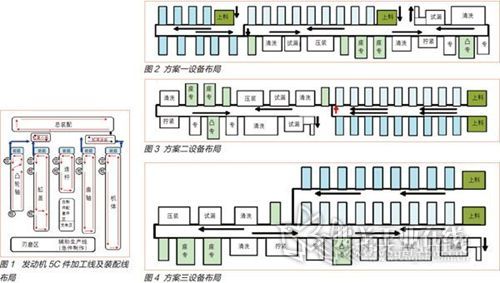
机加生产线的设计原则
生产线布局设计是系统中单元的选择及单元的排列组合,即结合车间场地、空间结构特点及工艺约束,对设备进行合理布局。要充分考虑设备之间在空间位置上的协调性,以确保生产系统物流畅通及设备的充分使用。
加工设备布局需要遵循包括工艺性、经济性、可持续性以及安全性在内的四大原则。
在此,以我公司发动机缸盖加工生产线平面布局为例,浅谈如何利用丰田生产方式的准时化支柱,优化工艺设计思路,实现一人多机管理,通过有效率的劳动提高生产效率。
“一个流”生产要求作业场地、人员和设备必须得到合理的配置,实现人尽其才、物尽其用以及时尽其效。在对该缸盖生产线进行平面设计时,按照工艺流程来排列生产设备,以逆时针拉动,尽可能使设备的布置流水线化。为了真正实现精益生产,我们对以下几种布线方式进行了分析比较。
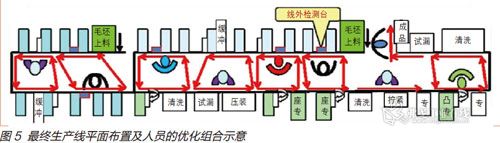
方案一:粗加工工序采用复列设备并C形套线布置,即实现U形生产,如图2所示。
方案二:粗加工工序采用复列设备平行直线布置,并序后实现U形生产,如图3所示。
方案三:粗加工工序采用复列设备,其中一条辅线为直线布置并入主线,另一条线与精加工设备成U形生产线,如图4所示。
三种生产线布线方式对比如表所示,经过整体的思考和规划后,优先选用方案一进行生产线平面布置及人员的优化组合。最终的生产线平面布置及人员的优化组合如图5所示。
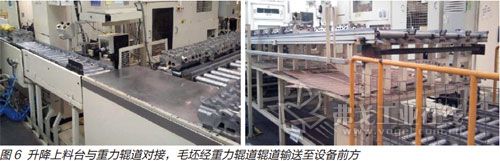
机加生产线的布局特点
1. 图5所示的缸盖生产线采用U/C形布线,实现“一个流”生产,其主要特点如下:
(1)U/C形布置使生产线距离最短,消除了人员走动和工件搬运的浪费,提高了生产效率。
(2)“一个流”生产,各道工序严格按节拍进行生产,将浪费显现化,消除批量不良品发生。
(3)消除在制品堆积与等待的浪费,第一时间暴露生产中存在的浪费并及时排除,降低成本。
(4)以“生产节拍”为目标,一人多机操作,实现少人化生产;培养多能工以均衡生产,且利于人员的增减。
(5)采用站立走动的作业方式,制定适宜的上料高度,增加作业人员工作的灵活性,从而提高工作效率。
(6)采用小型柔性加工设备和辅助设备相结合,易于生产线变更,节省空间。
(7)作业标准化,员工严格按照作业指导书的要求,按既定的生产节拍进行生产。
(8)流水化布局,要求每一道工序严格控制工作质量,做到质量在过程中控制,遵循内部用户原则。
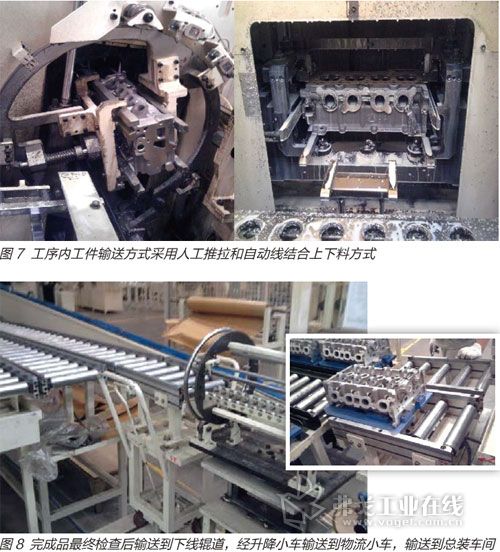
2.在物流方面,其工件流向为操作者正对机床,工件从右到左,逆向流动,主要特点如下:
(1)毛坯上料采用物流小车与液压升降台对接辊道形式(见图6)。
(2)成品下料采用滚道和成品车对接输送(见图7)。
(3)工序内工件输送方式采用人工推拉和自动线结合上下料方式(见图8)。
生产线实施标准化作业,其中标准手持是指按照作业顺序进行作业时,为了能够反复以相同的顺序、动作作业而在工序内持有的最小限度的在制品。缸盖生产线的标准手持包括生产线内设备上正在加工的零件数量(1件)和工序间滑道规定保持的零件个数(1件)。

结语
生产线布局问题是现代企业发展中面临的重要课题之一,精益规划生产线设备布局,如何在最短的时间内以最低的成本生产出符合市场需求的产品,将是决定企业在激烈的市场竞争中持续发展的重要保证。
目前,机加工线使用U形布局是推行精益生产的一种方式,通过5C件加工线布局优化过程的实践和创新,实现了“一个流”节拍生产、一人多机操作以及物流距离最短。经过总结,我们发现U形生产线布局具有以下优点:结构紧凑,U形布局从几何学上讲,能减少既有生产线的占用面积;并行粗加工线的设计,在单台设备故障或换刀时,不会影响节拍;U形加工线出现瓶颈问题,便于现场管理及时发现流水线哪部分有问题需要调整;封闭开口,减少产品和员工走动,最大限度减少动作的浪费,提升工作效率;优化作业组合,实现一人多机操作;员工技术水平较高,能掌握多工序操作能力;由于上下工序衔接,存放量少,物料搬运工作量少,搬运成本降低;生产计划简单,易于控制。
但其也存在缺点,主要表现为:设备专用性强,产品一旦变换,适应性较差;生产线的速度取决于最慢的部分,部分设备发生故障时会导致整条生产线中断;发生缺料或人员不在岗时,生产受影响较大;对员工的技术要求、素质要求较高,需要较长培训周期。
评论 0
正在获取数据......