气缸盖是发动机的重要部件,气缸盖阀座系统的压装、加工是气缸盖加工的关键工序,其质量直接影响发动机的使用性能。各发动机厂建线时对阀座的加工都已足够重视,而压装设备和压装工艺的选择却容易被忽视,本文就普遍采用的常温压装设备的分类、各类设备的特点及常见压装问题的案例进行了系统的分析。
汽车发动机的主要部件气缸盖的气门导管、座圈的加工工艺流程一般为:机加气门导管、座圈底孔→装配气门导管、座圈→精加工气门导管、座圈孔。气门导管、座圈的加工精度是保证发动机配气系统质量的主要因素,也是气门导管、座圈的压装质量的重要影响因素,如出现气门座压装不到位,结合面有缝隙,会引起气门脱落和机油消耗量大等严重质量问题,因此,如何选用压装工艺和压装设备是缸盖生产线建设中不可忽视的关键工艺环节。
现有气门座压装主要有常温压装、液氮压装和工件加热后压装等工艺方法,液氮压装、工件加热后压装分别是通过对气门座低温冷却和对缸盖高温加热,以减小装配过盈量带来的装配压力,常温后热胀冷缩原理使装配更紧密,但存在对变温实效性要求高、设备投资大等因素。而国内经济型小排量发动机厂仍普遍采用常温压装工艺,根据生产线投资和效率要求的不同,常温压装设备差异也较大,下文就常温压装设备的使用进行介绍。
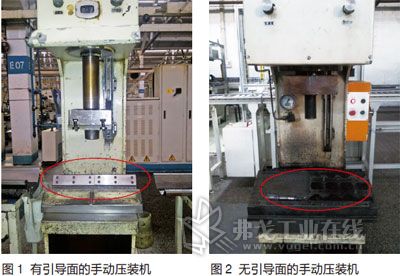
压装设备种类
从发动机压装技术发展历程和国内发动机厂普遍采用的压装设备现状看,压装机主要有以下三种类型:手动压装机、半自动压装机和全自动压装机。
1.手动压装机
手动压装机是单头液压油缸压力机配专用夹具组合而成;压装时采用手持压装工具压装。压装步骤一般为将气门手动套入压装工具上,然后将手持压装工具连同导管(或座圈)一同对准导管底孔(或座圈底孔),压头压下,将导管(或座圈)压入,移动工件,继续完成其他各孔压装。
夹具的类型一般有两种形式,一种为固定夹具,适合缸盖进排气面,形状规则,有平整引导面的缸盖(见图1);另一种为可滑动结构,上夹具板相对夹具底座可相对移动,适合进排气侧无引导面的缸盖(见图2)。
2.半自动压装机
半自动压装机由机体、升降压装装置、上料装置以及夹具移动装置等部分组成,其中升降压装装置是由液压缸(或气液增压缸、伺服电动机)驱动压头实现气门导管、座圈压装,夹具移动装置为夹具由伺服滑台驱动移动缸盖气门导管、座圈孔距要求的步距,以实现各孔连续压装。上料装置为人工将导管、座圈放入料夹内,导管、座圈在重力作用下或气缸推动下移动到压头取料口,压头在取料口自动取料压装。压装方式有管座对压(见图3)和管座分压(见图4)两种形式。
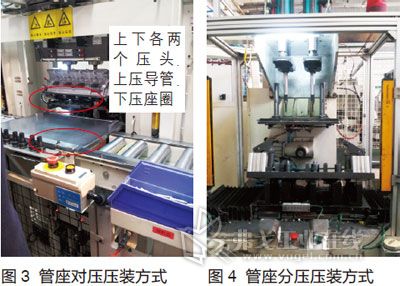
3.全自动压装机
全自动压装机由机体、自动压装装置、自动上料装置和工件自动输送装置等部分组成,压装流程为,工件放置在入料口(或由上工序通过机动滚道输送至上料口)→工件自动输送到压装工位→上料装置自动上料(气门座圈、气门导管)→压头自动压装→压装一次完成或夹具移动完成多次压装(取决于压头数量)。自动压装机进料工位和压装工位如图5和图6所示。
压装设备的特点及选型原则
1.手动压装机
设备结构简单,投资成本少,制作周期短,维修维护简易,适合用于小批量新品试制,或建线需求紧迫,年产小于5万台的缸盖线也可以考虑采用;其缺点是操作者劳动强度大,压装质量和效率受人为因素影响大,质量保证能力有限。
2.半自动压装机
半自动压装机一般为立式结构,占地空间小,特别是管座对压装机完成全部气门管座的压装只需要两个工位,是比较节约占地面积的方案。同时半自动压装机缸盖、气门导管和座圈为人工上料,省去自动输送和自动选料装置,解决投资成本的同时,减少了输送、筛选中的故障几率,减少了维修时间和成本,是现在对整线自动化程度要求不是特别高的生产线普遍采用的压装模式。这也是三种设备中性价比最高的设备方案。
3.全自动压装机
其特点在于整个压装过程不受人为因素影响,工位间输送不存在人为磕碰伤问题,最为节约劳动力;缺点在于设备投资成本高,使用中的维修成本和技术要求都较高。
压装常见问题解决方案
1.气门座压装有缝问题
气门座压装质量要求为气门座与气门座底孔间配合无缝隙,一般检测标准是0.02mm塞尺检查缝隙不能进入。而气门座压装有缝问题也是压装过程中最为常见的质量问题,且不容易被检测发现,会带来质量隐患。
气门座压装缝隙一般由以下几方面造成:压头垂直度改变;夹具定位销孔定位精度有丧失;夹具支撑面有磨损,夹具平面度、角度得不到保证。
针对以上原因可进行逐项排查,如用角度尺对夹具角度进行找正(见图7),制作找正样棒对压装位置进行找正(见图8),重新配做夹具定位销,重新修磨定位面等。
除以上常规的检测调整方法外,对于手动压装机在压装过程中可以尝试进行两次压装方式。第一次进行预压,压头压入一半抬起,压装辅助工具旋转180°后再次压装,最终将气门座压装到位,避免压装不垂直状态产生的微小缝隙问题。
半自动压装机和自动压装机的气门座压装深度,一般由行程感应或压力感应控制,伺服电动机驱动的压装设备能通过位移控制较好地保证压装深度,而液压缸和气液增压缸驱动压头的压装机单靠行程感应是不能满足压装要求的,因此一般有压力感应保证压装深度,而在到位进行几秒的保压时间是保证压力反馈的准确性、保证压装无缝隙的必要手段。此外,压力监控曲线能很直观地反映压装受力过程,是分析压装问题的有力帮手,建议增加此项功能。
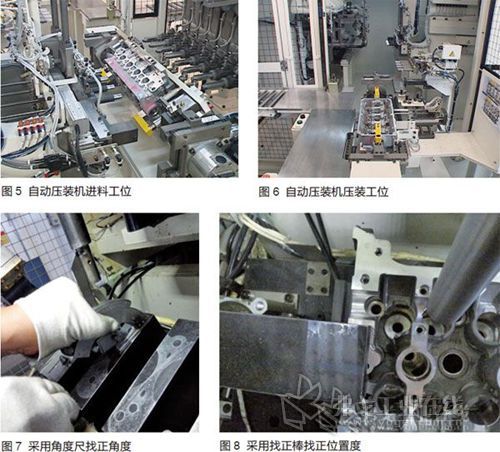
2.气门导管压装不到位问题
气门导管压装有压装深度要求,虽然不像气门座压装精度要求那么严格,但压装深度不满足会对装配产生不良影响,因此也不能忽视。
(1)原因分析
第一,压头相对于气门导管底孔垂直度得不到保证,导致压装受力大,压头提前返回。第二,压力不稳定,油压受温度影响,粘稠度变化,影响压装力;风源气压不稳定影响气液增压缸输出压力。
(2)解决方案
首先,调整压头及夹具,保证压装垂直度;其次,根据季节交替的温度变化,及时更换液压油,保证液压动力头的压力稳定性。在入口风源处增加储气罐和气压平衡罐,保证风量和风压。
此外由于气门导管是通孔结构,无法像气门座压装那样直接用压力的突然增加来判定压装到位,因此一些压装机厂家会设计成压头直接压装到弹簧窝上,以保证压装深度,但这种方法因为力直接作用在缸盖上,可能在弹簧窝上留有压装痕迹,或造成缸盖出现变形或压装裂纹问题,因此建议采用位移感应或硬限位方式控制压装深度。
结语
目前国内经济型小排量发动机厂普遍采用常温压装设备,通常有手动压装机、半自动压装机和全自动压装机三种类型。各种设备类型结构特点各不相同,需根据规划产能和投资成本进行合理选择,同时应充分考虑压装中的常见压装问题,进行技术上的精度要求和检测要求,从而采用性价比最高的压装设备,压装可靠稳定的缸盖,保证发动机配气系统质量要求。
评论 0
正在获取数据......