发动机内衬垫在工作时除需要具备耐磨、耐蚀、耐高温和耐高压的作用外,还需具备密封防滑作用,所以工艺上要求其材料既要有一定的柔性以抗扭转,又要有足够的摩擦系数以防滑,还需具备耐磨、耐蚀等性能。现在国内衬垫材料一般采用在钢材料上进行一些表面涂覆处理或直接选用尼龙材料,随着发动机性能的不断升级,这类材料已不能满足高档机型的要求。国外已有在弹簧薄钢片上包覆金刚石镀层的衬垫,目前国内也有企业在研发用0.1mm厚的DIN C75S材料做基材,表面层采用镍基包覆金刚石衬垫以替代进口件。除基材、镀镍层性能外,金刚石的尺寸、嵌入量和嵌入深度等对性能影响更为关键,因此正确表征这些特性就显得尤为重要。
由于此工艺本身难度较大,金刚石尺寸只为10~50μm,颗粒小质地坚硬,现有的一些用光学显微镜观察尺寸分布、用轮廓仪测量粗糙度等常规检测方法不能很好地展示金刚石镀层的形貌和工艺特性,特别是纵向方向的形态几乎是不可能的,扫描电镜虽然也可观察三维形貌,但由于表面是金刚石,SEM的效果也不够理想,且纵向方向的测量也不能实现。
蔡司公司生产的高分辨率显微镜LSM700采用激光作为光源,利用先进的图像扫描与处理技术,不需要做导电处理、无须制样,在不损伤样品的前提下,可快速形成样品表面亚微米程度的三维结构信息,并可对样品表面形状、粗糙度、波度和阶梯高度等进行高精度分析与测量,很好地解决了此金刚石镀层形貌分布及纵向方向上的测量需求,对产品质量评估和企业研发具有十分重要的意义。
在此,本文对衬垫金刚石镀层常用检测方法与共聚焦检测方法进行对比说明。
衬垫描述
基材牌号DIN C75S,厚度约为0.1mm,上下表面为镍基包埋金刚石镀层,如图1所示。
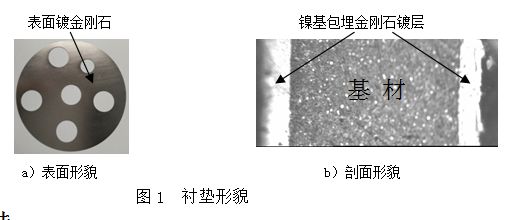
常用测试方法
1.体视镜观察形貌及分布
选取不同的区域放在体视镜下观察。如图2所示,表面可见大小不同形状各异的金刚石颗粒,由于受体视镜倍率和分辩力的限制,无法观察并分清起包埋作用的底层镍结晶及嵌入其中的金刚石形貌,只能对露在表层的明显具备金刚石色泽形貌的颗粒进行密度评估和粒径测量等。
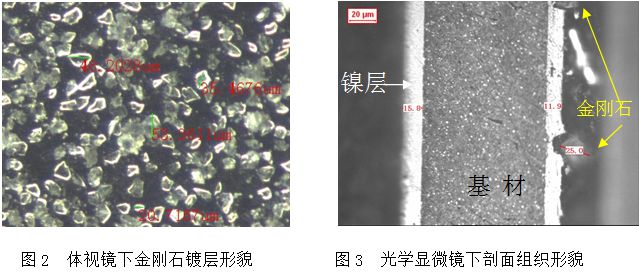
2.截面金相法测量嵌入深度
选取不同部位截取剖面试样,磨制、抛光和化学侵蚀后在光学显微镜下观察。如图3所示,基材为回火马氏体+弥散小碳化物,表面处理层为镍基底层上包埋着少量金刚石颗粒,由于金刚石质地坚硬,磨制金相试样时易脱落,给测量带来不便;且金相剖面法测量的区域非常小,所能检测的甚至只能是几个颗粒的嵌入状况,故此法只能参考使用。
3.粗糙度法测量平均嵌入深度
选取不同部位用轮廓仪进行表面粗糙度的测量,如图4所示,可以得到规定长度上的Ra和Rz值等,考虑金刚石的平均粒径,可计算出最大、平均嵌入深度等参数。由于金刚石尺寸小、分布也不均匀以及包埋深浅不一等特点,轮廓仪测量时测头不一定能接触到所有测量线上的颗粒,且包埋深的一些颗粒轮廓线也极易被当作基线上的杂峰过滤掉,最后参与计算结果的只是那些峰值明显的颗粒,难以完整反映测量线上的金刚石嵌入的真实状态,更不能说明整个表面的金刚石嵌入状态。
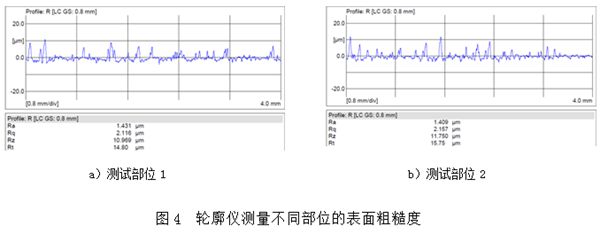
激光共聚焦方法
将试样放在Zeiss公司的Lsm700型激光共聚焦的扫描台上,在明场下观察镀层表面,确定合适的倍率后切换至激光模式;选择405nm激光器开始对试样进行三维扫描,扫描结束后生成全方位三维形貌图,在此基础上可进行一系列的分析。
1.形貌及分布
由于共聚焦显微镜的分辨率可达到水平0.1~0.2μm且Z轴10nm,比传统显微镜可提高至少40%。如图5所示,扫描后可清楚看出表面金刚石三维形貌及分布,并可识别出镍基底层的镍结晶。
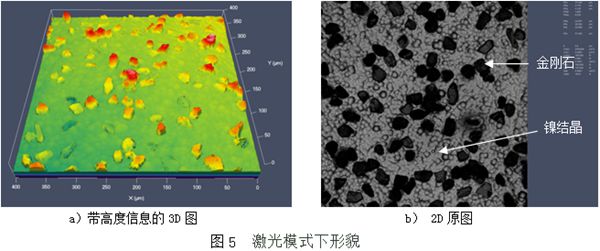
2.颗粒尺寸测量
激光模式下进入测量模块,如图6所示,可 方便快捷地测出任一颗粒的粒径以及长、宽和高尺寸。
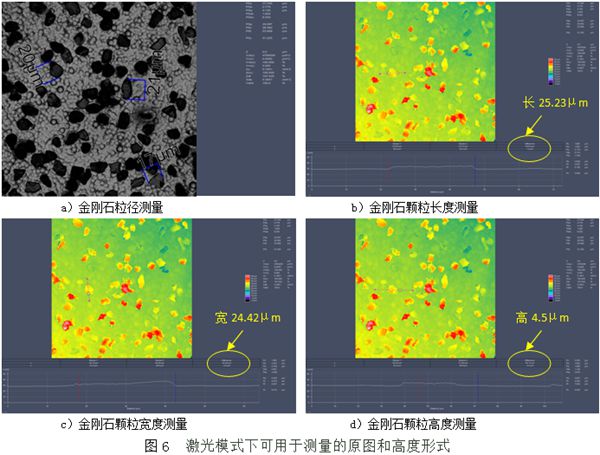
3.线粗糙度、面粗糙度测量
激光模式下进入测量模块,如图7所示,可方便快捷地测出任意方向线粗糙度及扫描区域的面粗糙度数值,Z轴分辨率可达10nm,与传统接触式轮廓仪测头所能分辨的微米级深度相比,检测精度提高了许多,并配有测量部位三维图形,也更形象直观;通过Zeiss Lsm700独有的图像拼接功能,可分析更大面积甚至垫片的整个平面全貌。
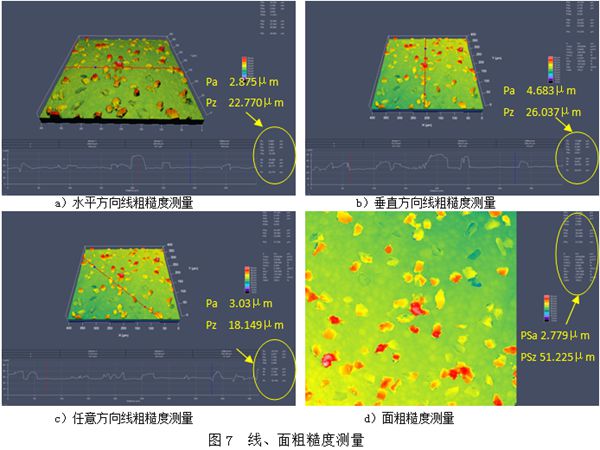
4.专用软件分析
(1)将扫描采集的图像导入专用Zeiss二维分析软件AXio Imaging 中,如图8所示,可实现一系列几何量、相面积含量等计算测量功能。
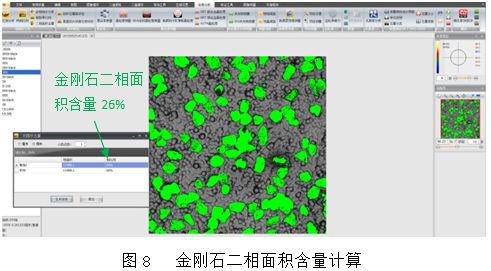
(2)将扫描采集的图像导入专用Zeiss三维分析软件Cofomap中,如图9所示,可实现一系列三维几何量、任意选取区域的线和面粗糙度测量功能。
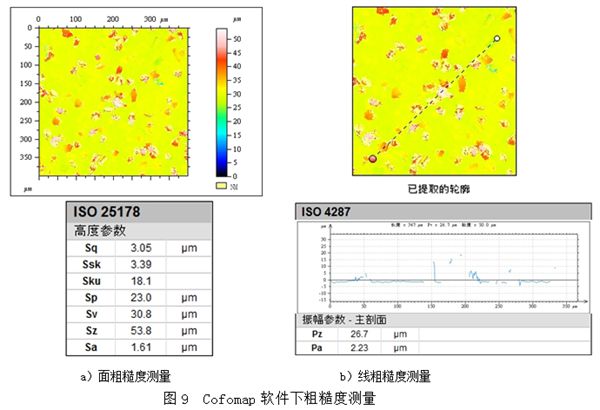
三维激光共聚焦显微镜分析的优点
上述为针对垫片同一区域用光学显微镜、轮廓仪和LSM700三维激光共聚焦显微镜分别检测结果,将这些结果进行对比可看出三维激光共聚焦显微镜检测具有如下优点:
1.共聚焦显微镜观察到的金刚石颗粒形貌比体视镜下形貌轮廊清晰,既可观察到金刚石大小分布,还可分清起包埋作用的底层镍的结晶,层次分明,不易象体视镜下因分不清颗粒性质而造成误判。
2.共聚焦显微镜扫描所得的三维图可针对任意颗粒进行三维尺寸测量,比体视镜、金相显微镜的二维影像测量更为科学。
3.共聚焦显微镜测量线粗糙度可在图形上选取任意方向和部位进行测量,用于评价的样本量可在一个图形上取若干组进行平均,一次实现多样本量测量;而接触式粗糙度检测只单一反映测头经过轨迹的粗糙度水平,效率低,多样本平均比较麻烦。
4.共聚焦显微镜由于Z轴分辨力可达10nm,与传统接触式轮廓仪测头所能分辨的微米级深度相比,检测精度高,加上测量部位三维图形展示,更形象直观。用轮廓仪进行表面粗糙度的测量,因金刚石尺寸小、分布不均匀和包埋深浅不一等特点,测头不一定能接触到所有测量线上的颗粒,且包埋深的一些颗粒轮廓线也极易被当作基线上的杂峰过滤掉,最后参与计算结果的只是那些峰值明显的颗粒,难以完整反映测量线上的金刚石嵌入的真实状态。
5.共聚焦显微镜可以测量出面粗糙度值,通过Zeiss Lsm700独有的图像拼接功能,可分析更大面积甚至垫片的整个平面形貌和面粗糙度值,而接触式轮廓仪只能检测线粗糙度。
结语
分析表面镀金刚石的薄垫片方法,因共聚焦扫描显微镜可进行三维扫描,分辨力高,可观察到样品表面亚微米程度的三维形貌,可测量多种微小的尺寸,无需制样便可分析垫片上金刚石形貌、尺寸、嵌入量和嵌入深度等,三维比二维分析更形象、更准确和更方便。用面粗糙度表征整个面金刚石嵌入深度比线粗糙度更科学,再与其他专用软件配合使用,还可得到更多的测量参数信息。因此,共聚焦扫描显微镜很好地解决了此金刚石镀层形貌分布及纵向方向上的测量需求,对产品质量评估和企业研发具有十分重要的意义。
评论 0
正在获取数据......