某四缸汽油机缸盖在压装气门导管过程中,导管端面有崩角现象,从而导致燃烧室试漏不合格。为查明问题的根本原因,本文对气门进行了材料成分、断口、显微组织、硬度和几何尺寸等参数的比较分析。
某汽车公司发动机工厂,在加工四缸汽油机缸盖过程中,最终试漏机燃烧试漏不合格,沉水发现导管端面有崩角现象。为查找崩角断裂失效的原因,本文对崩角断裂失效导管原件(见图1)和同批次正常零件(见图2)的相关参数进行了比较分析,同时也对气门导管压装机设备参数、状态进行了确认。
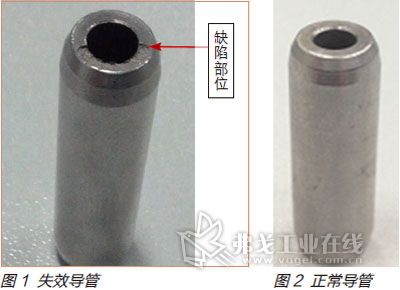
对比分析方法
1.几何尺寸测量
根据设计图样及气门导管压装的关键尺寸(见图3),对同批次零件进行相应几何尺寸测量,检测设备为光学投影仪(精度为1mm)。
由于导管是在压装过程中出现崩角,且导管压装过程属于过盈配合。若从缸盖上取出崩角断裂失效的导管,需强行敲打而出,敲打端面处呈凹凸状,破坏导管外观形貌,无法检测其几何尺寸。
根据GB/T2828.1《计数抽样检验程序》对该批次未使用的气门导管进行抽检检测,抽检数量为3个,检测结果显示气门导管几何尺寸均符合图样要求,因测量报告数量较多,本文中不进行详细介绍。
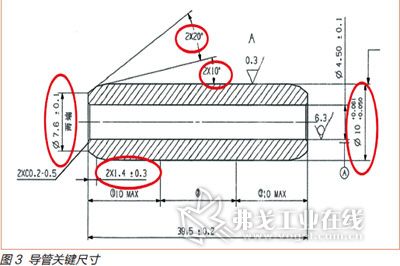
2.材料化学成分
在崩角失效导管和正常导管上,取样进行化学分析,结果(质量分数)如表1所示。由此可见,导管材料属铁基粉末冶金,失效导管的化学成分符合图样要求。
3.硬度测量
在失效导管的端面及圆柱表面,进行洛氏(HRB)的硬度测量,其硬度检测结果符合图样要求,具体数值如表2所示。
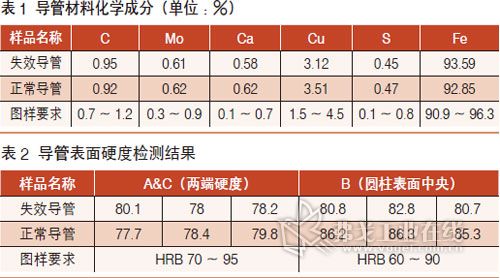
4.金相组织分析
在失效导管及正常导管端头相同部位截取金相试样,经磨制和抛光圆截面,其金相显微组织如图4和图5所示。其中,图4为试样抛光后未经腐蚀的金相显微组织对比,可以看出,失效导管的孔隙较多且分布较为均匀,大小不一,但对导管崩角失效影响不大;正常导管的孔隙较少、大小以及分布较为均匀。图5所示为试样进行3%硝酸酒精腐蚀后的金相显微组织,可以看出,失效导管的基体为较粗层状珠光体和铁素体,其边上分布着黑色孔隙黑色的孔隙和灰色的颗粒氧化物;正常导管的基体为珠光体和铁素体,其边上分布着黑色孔隙黑色的孔隙和灰色的颗粒氧化物。按JB T2798-1999《铁基粉末冶金烧结制品金相标准》进行评定,其金相组织符合设计要求。
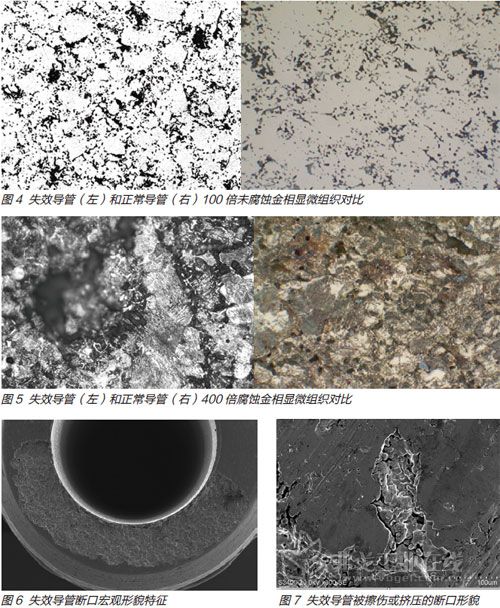
5.断口宏观分析
气门导管崩角发生在导管端部(见图1),以局部端面片层脱落且无形变的方式失效。断口宏观形貌特征如图6所示,断口面的原貌较为完好,其断口特点为粗糙、无纤维状区和剪切唇区,均为起始于外径周边的收敛性放射状云,并在断口面的内径周围存在许多细小的宏观台阶,这说明零件加工状态和使用状态下存在相当的应力集中所致。由于失效导管断口面上不存在纤维状区和剪切唇标记,仅为粗糙的放射状区标记,表明该材料脆性大、强度低。所以裂纹起源始于工件外圆周边,裂纹由外向内以放射状特征扩展,最终发生脆性断裂。
6.断口微观分析
为了能更好地进行断口微观比对分析,对正常气门导管进行一处人为崩角断口,对失效导管和正常导管的断口在扫面电镜中进行断口形貌观察。因导管断口不干净无法使用电镜做正常的拍照观察,需经超声波清洗机清洗后才能放入扫描电镜中进行观察。
对失效导管断口进行微观分析发现断口边界有明显间隙,有较少部分断面被外力擦伤或挤压破坏了形貌,但其为少量且不影响整体断口微观分析;整个断口绝大部分形貌如图7所示,断口表面光滑,颗粒间空隙大小不均匀,无任何正常断裂的痕迹,即无蜂窝状烧结颈;仅部分局部端面有少量的蜂窝状烧结颈。与正常导管的断口形貌比较可知,失效导管断口微观形貌异常,无蜂窝状烧结颈,裂缝沿着颗粒与颗粒边界产生,即因颗粒间粘附能力弱。在正常压装力下,颗粒间易出现裂纹,并以片层脱落的方式断裂失效。全面审核供应商制造导管的过程中发现,在导管压制时出现裂纹缺陷,未处理的缺陷零件经烧结后无法形成正常的烧结颈。
结语
采用对比分析的方法,对问题导管进行全面精密的测量分析后,可以确定引起此次断口崩角断裂失效的根本原因是导管在压制过程中已出现裂纹和疏松的现象,零件带着缺陷经过烧结后,无法形成正常的烧结颈,降低导管的加工性能,从而在将导管压装至缸盖上时易发生崩角断裂。
评论 0
正在获取数据......