清洗机原理
板料清洗机是通过喷嘴和刷辊,对板材表面进行清洗,并通过挤干辊的挤干,使板材上留下厚薄合适且均匀的油膜涂层的一种设备。清洗机大致由主电柜、清洗上箱体、下箱体、回油管、油箱、清洗油泵、引入辊、刷辊、挤干辊和其他电器元件等部件组成,如图1所示。
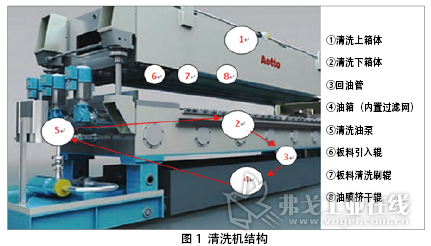
板料清洗
1.板料清洗过程
板料的清洗过程大致如下:板料由引入辊带入清洗机内,清洗机泵站工作,将油箱中清洗油按照设定的压力和流量喷射至清洗箱体内板料上下表面,同时清洗刷辊上下刷拭板料,通过清洗油喷淋和刷辊的刷洗去除其上下表面的颗粒杂质;液压站工作(有些清洗机为气压),通过设定的挤干压力将板料上的残油挤出,从而达到板料表面上留下厚薄合适且均匀的油膜涂层。清洗过程中产生的清洗油雾经油雾收集器回收到清洗油箱,过滤器及离心净油机完成对清洗油的过滤及净化处理。
2.清洗过程对板料清洁度的影响
在整个清洗过程中,包含板料清洗前输送、板料清洗及板料清洗后的输送三个环节,其影响板料清洁度的因素大致可以分为两类:外部因素和内部因素。外部因素包含板料本身、板料清洗前后输送带以及周边环境。清洗机单位时间内的清洗程度是一定的,板料本身越脏,清洗完残留在板料上的异物越多;板料清洗前后的传送机构和清洗后环境空气如果有异物,那么容易带到板料表面,也将降低板料表面清洁度。外部因素主要通过来料的检查和清洗环境的5S来控制,提高板料清洁度。
内部因素包含清洗油油质、过滤系统、刷辊重合度、刷辊转速、刷辊完整性、喷油角度和喷油量及清洗机内部清洁,内部因素原理如表1所示。

其中,刷辊重合度验证方法为在板料上放一张纸,将刷辊按照设定的重合度下降,此时会压出一道均匀的压痕,证明上下刷辊对板料有接触,如图2所示。
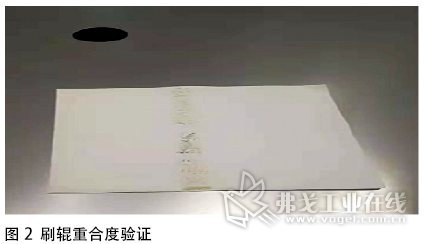
刷辊的磨损确认方法为在钢板上用记号笔或水性笔等画线,然后通过刷辊工序,根据画线有无消除,消除的表面痕迹是否均匀,确认刷辊工序通过后的状态,如图3所示。
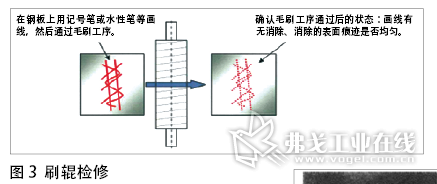
板料油膜厚度
清洗后板料油膜厚度对产品质量也至关重要,油膜厚度影响因素也分为外部和内部两类。
1.外部因素
外部因素一般有来料板料油膜和线速、板料尺寸、清洗油油品以及室温等方面。
(1)来料板料油膜和线速的影响
因为清洗机挤干速度跟生产线线速是匹配的,所以在单位时间内清洗机挤干的油量是固定的,如果来料板料油膜过厚,挤干后残留在板料上的油会增多。
(2)板料尺寸的影响
异性料(如拼焊板)或者双垛料(一厚一薄),会在厚薄板料交接的位置由于挤干辊挤干不到位,存在薄的板料一边(靠近厚板料)油会多一点;板料越小挤干效果越佳,板料越大挤干效果越差,同时也对挤干压力的设定增加难度。
(3)清洗油油品
清洗油有黏度、密度、酸值、闪点、水分及机械杂质等特性,一般来说黏度小,对清洗机挤干效果比较好,但是黏度小的清洗油闪点低,不符合涂装要求,同时防锈效果也不佳。清洗油油温高,清洗油黏度低,流动性好,挤干效果佳;但是温度太高会影响清洗油特性和挤干辊寿命,一般设定油温为30~40 ℃。
(4)室温
天气热,室温高,清洗油流动性大,冲压成品件底部积油风险更高;天气冷,室温低,清洗油流动性小,冲压件底部不易积油。
2.内部因素
内部因素主要包括挤干压力、喷油量和角度、挤干辊材料、使用年限及清洗机本身结构,内部因素原理如表2所示。
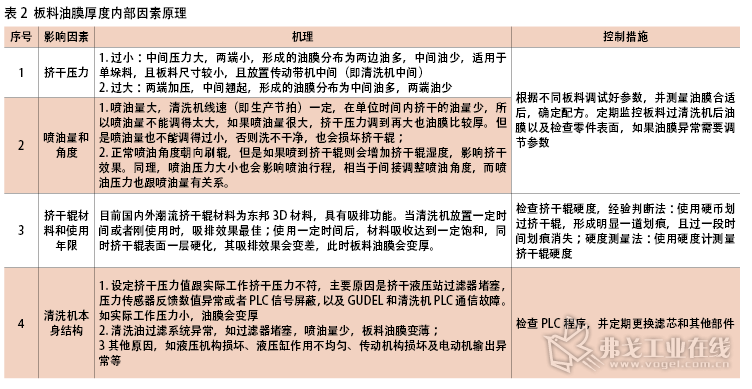
3.板料油膜厚度的验证和测量
常规油膜厚度测量有称重法和凸镜测量法,这里主要使用的是凸镜测量法。如图4所示,将凸镜放置于油斑上,用电筒侧面照射将看到一个圆形的亮斑,亮斑大小对应刻度表示油膜厚度。
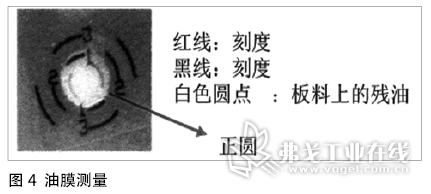
冲压板料涂油方式分为轻涂油、中涂油和重涂油3种,对应油膜重量分别为0.5~1.0 g/m2、1.0~1.5 g/m2及1.5~2.0 g/m2,根据上述分析的清洗油膜厚度因素调整清洗机参数,将得到对应的涂油标准。将不同涂油的冲压件分别做静置和涂装过车试验,中涂油以下零件放置两天试验,未发现零件底部和转折位置有明显积油;中涂油以下冲压件车身和涂装过车后质量正常。
结语
冲压件清洁度和油膜厚度是监控产品质量的重要环节,其主要影响因素有外部因素和内部因素,通过控制清洗机参数和外部环境因素可以达到良好的清洗效果和零件表面油膜厚度,提高冲压件质量。
评论 0
正在获取数据......