雷诺混动丨日产HV电机技术
文章来源:EDC电驱未来
发布时间:2021-01-24
E-TECH由1.6L直列4缸汽油发动机、2台电机、使用牙嵌式离合器的多模式变速箱以及锂离子电池组成,混合动力车与插电式混合动力车的电池容量、电压不同,混合动力车电池容量1.2kWh、电压230V,插电式混合动力车电池容量9.8kWh、电压400V。
雷诺在法国销售(2020年上市)的Megane和Captur的插电式混合动力车(PHV)、Clio(相当于日本Lutecia)的混合动力车(HV)采用了新型混合动力系统“E-TECH”。
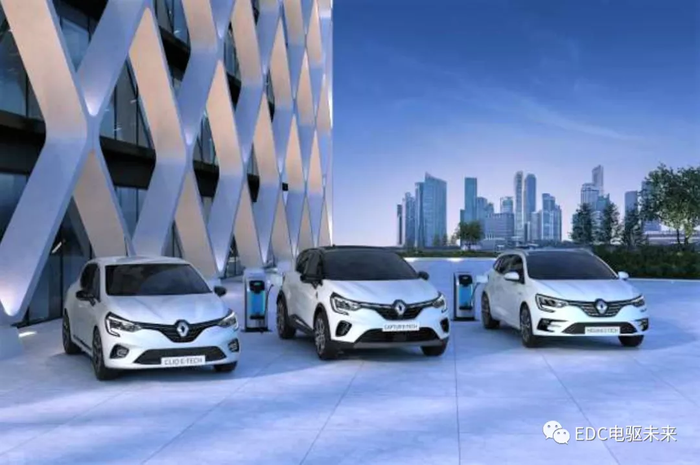
雷诺E-TECH配套车型(左起)Clio混动版、Megane和Captur的插混版
该系统由一个多模式变速箱和两台电机组成,该变速箱可以进行发动机轴4挡、电机轴2挡的换挡变速。驱动电机改良了日产X-Trail使用的电机,除了定子,转子也采用分割式铁芯工艺(“全球首个”:见下文)来降低成本。
E-TECH由1.6L直列4缸汽油发动机、2台电机、使用牙嵌式离合器的多模式变速箱以及锂离子电池组成,混合动力车与插电式混合动力车的电池容量、电压不同,混合动力车电池容量1.2kWh、电压230V,插电式混合动力车电池容量9.8kWh、电压400V。
2台电机的参数规格根据混合动力车与插电式混合动力车的电池电压差异而不同,混合动力车与插电式混合动力车的主驱动电机的功率分别为36kW、49kW,混合动力车与插电式混合动力车的HSG(起动发电机)的功率分别为15kW、25kW。
图2:
E-TECH组成部件的参数(根据雷诺资料制作)
动力总成采用的结构是在多模式变速箱上安装2台作为混合动力系统的电机,并集成在发动机上。
装置上方搭载的HSG(起动发电机)主要负责发动机的启动和行驶时的辅助,采用的是日系厂商制造的水冷式同步电机。
变速箱发动机的另一侧搭载的扁平型电机是水冷式分割铁芯集中绕组的36kW/49kW主驱动电机,可实现纯电行驶以及仅靠油门踏板即可加减速的再生制动。
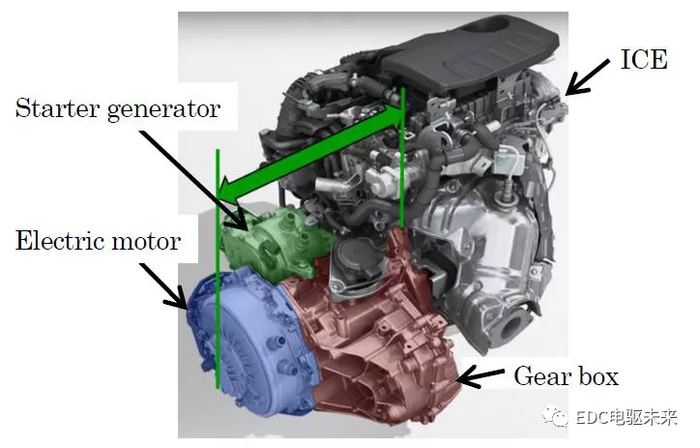
图3:动力总成的结构
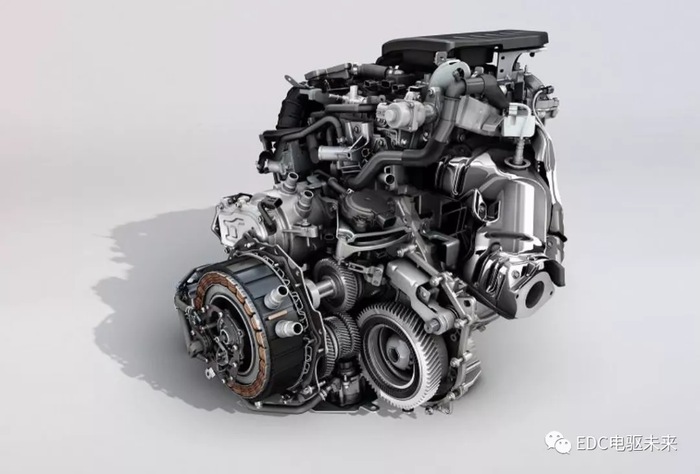
图4:动力总成的切割模型 (出处:雷诺)
E-TECH的变速机构是雷诺自主开发的多模式变速箱,可以在发动机轴上进行4挡变速,在电机轴上进行2挡变速。
纯电行驶(从出发开始到30km/h左右)的情况下,离合器C3a或C3b锁定,以各自的齿轮比通过驱动电机的动力驱动车轮,再生行驶时,动力经由相同路线反向传递,从电机获取再生电力。另外,还可逆转这种连接状态实现倒车操作,没有专用的倒档齿轮。
如果踩下油门,就会切换为依靠发动机动力行驶的模式,C2a、C2b或C1锁定,发动机动力传递到车轮。
E-TECH的变速机构没有摩擦离合器,采用牙嵌式离合器进行变速。
牙嵌式离合器(dog clutch)由于形似狗的牙齿因此得名,是一种啮合离合器,啮合齿轮廓在轴向方向凹凸分布整个圆周,通过与相对方向相同形状的齿轮啮合,可以实现快速的咬合,它也用于各种运输设备的变速器以及用于竞赛的变速器。
E-TECH中由于电机控制咬合位置,因此变速机构中没有“同步”装置。

图5:多模式变速箱的组成部件 (出处:雷诺)
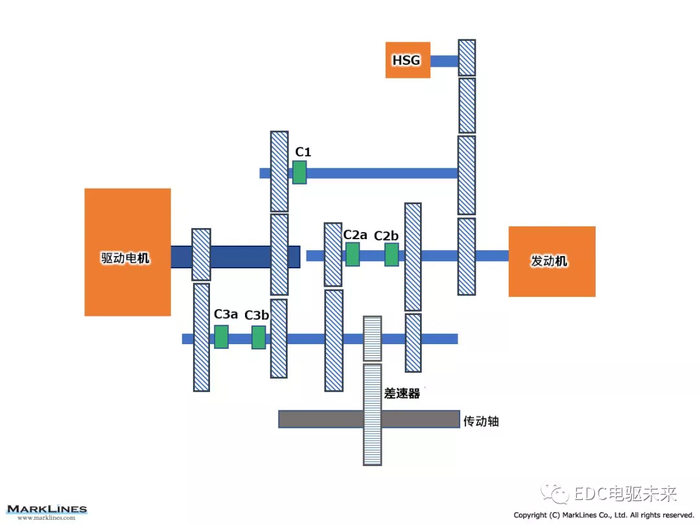
图6:齿轮结构概略 (根据雷诺资料制作)
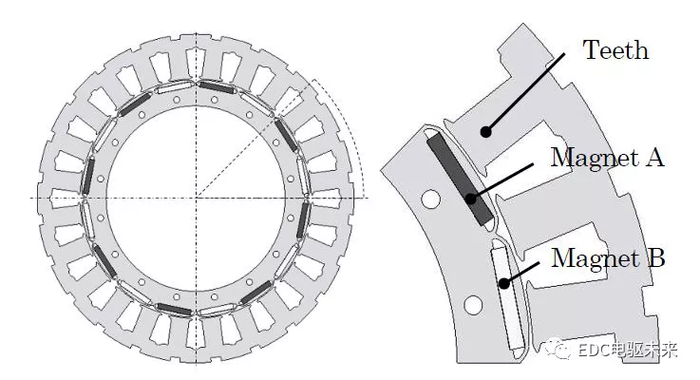
图7:驱动电机的磁路
驱动电机采用的是扁平型的集中绕组电机,实现在小型车上的搭载。
电机类型方面,雷诺EV采用了其他整车厂的电动汽车未采用的电励磁同步电机(EESM),但E-TECH系统采用了与日产X-Trail混合动力车所用电机相同的IPMSM(内置式永磁同步电机)。而且从此次发布的公告也能了解到开发由日产负责,在日产的横滨工厂生产。
日产X-Trail混合动力车使用的电机只有定子是分割铁芯,E-TECH的电机除了定子铁芯,转子铁芯也是分割铁芯。
电机是16极24槽的IPMSM,由转子的16个磁极和定子的24个线圈组成,转子内径一侧的铁芯厚度小,磁体结构简单,每极一块磁铁。
E-TECH为了在电机驱动的启动、加速中实现顺畅的动力性能,所需的输出功率增加,最大扭矩和最大输出功率均大幅提升。
最大扭矩从日产X-Trail混合动力车所用电机的170Nm增至205Nm,最大输出功率从30kW增至36kW(混合动力)、49kW(插电式混合动力)。
定子的外径尺寸为255mm,与日产X-Trail混合动力车所用电机相同,但为了应对系统所需输出功率的增大,转子的外径尺寸比日产X-Trail混合动力车所用电机的178mm要大,增至184mm,铁芯的层叠厚度也比日产X-Trail混合动力车所用电机的55mm更厚,尺寸加厚到60mm,并且电机的扭矩密度提升了20%。
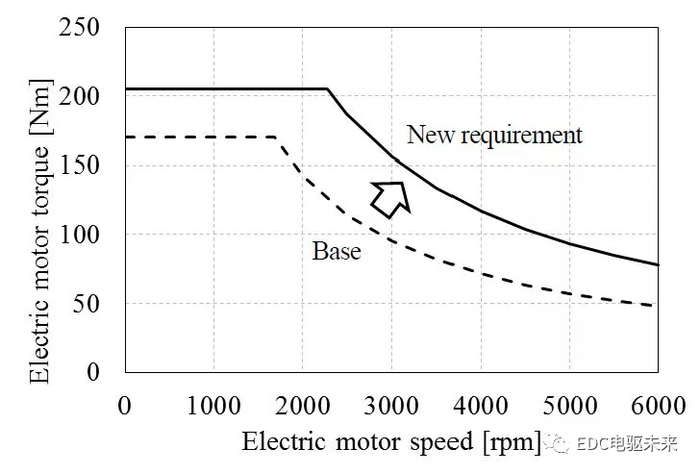
图8:X-Trail与E-TECH(插电式混合动力)电机的扭矩特性
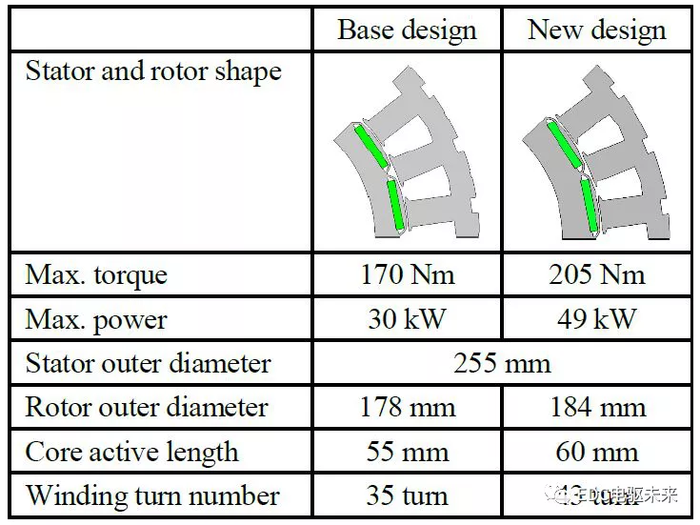
图9:X-Trail与E-TECH(插电式混合动力)电机的主要参数
随着最大扭矩的提升,转矩脉动增大,针对旋转48阶分量(频率为转速48倍的振动分量,是车辆声音振动性能恶化的原因)采取对策。
图10说明了48阶转矩脉动的产生原理,随着图中从左到右时间的流逝,显示了转子顺时针旋转的样子,图中的箭头用向量表示磁通量,旋转的同时箭头的大小也会发生变化。
黑色磁铁和白色磁铁在转子表面显示S极和N极,定子的24个齿会被激发2倍大的48阶脉动分量。
48阶转矩脉动分量在结构上因与定子的齿数关系而产生,不能完全消除,但是针对对转矩脉动影响较大的转子外围形状和定子的齿尖形状进行详细研究,实现扭矩密度和转矩脉动的减小,使转矩脉动比传统电机减小了60%。
图11显示了集中绕组(Concentrated winding)和分布绕组(Distributed winding)的各种电机转矩脉动和扭矩密度的关系,从中可以得知E-TECH搭载的电机尽管是集中绕组,但转矩脉动得到了抑制,与分布绕组的电机相当,有助于改善声音振动性能。
图10:转矩脉动(48阶)产生的概念图
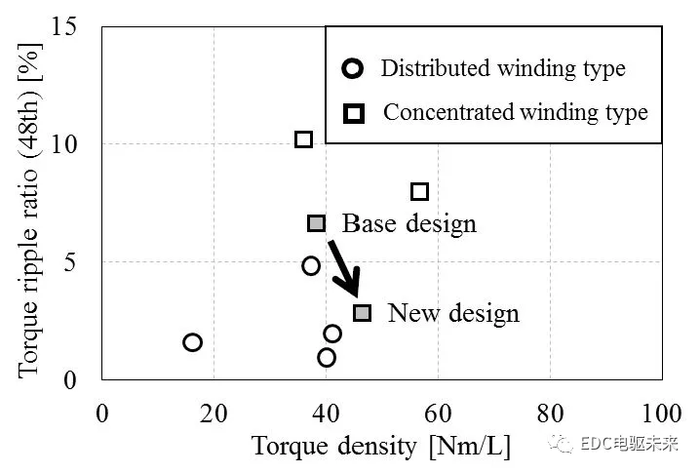
图11:各种电机的转矩脉动和扭矩密度的关系
驱动电机在混合动力车上安装的布局方式有很多,但是对于夹在单元之间或者安装在单元末端的单电机混合动力车来说需要轴长较短的扁平型电机,线圈末端比分布绕组要小,因此很多情况下采用能够缩短轴长的集中绕组。
集中绕组的电机为了抑制轴长的同时确保扭矩,增大了直径,并且磁路位于转子的中心附近而降低了对性能的改善贡献,另一方面因为单元小型化的需求,很多情况下需要布局减速器的机械零部件,所以电机的空心度较高。
由于像这样大直径并且中心部位是空心的电机铁芯的材料成品率很低(电磁钢板的大部分成为废弃材料),因此采用“分割铁芯”的方法,将铁芯分割成一个个小块而不是使用一整个圆形的铁芯,并在加工后进行组合,从而实现原本的大直径尺寸,提升了利用率。
定子的分割铁芯通常被当做一种提升材料成品率也就是降低成本的对策来实施,但是因为转子材料成品率低下的程度要比定子小,而且对于要分割并组装以高转速旋转并承受离心力的转子来说,在制作上面具有风险,因此虽然大型设备的电动机等采用了该方法,但是电动汽车的电机并未采用这种方法。
本次E-TECH采用的驱动电机除了定子铁芯外,作为全球首个量产应用技术,还尝试分割转子铁芯,转子形状由于16个磁体周围部位重复采用同一个形状,因此可以分割为16份,但是太细了,所以分割为4个部分,并且圆周方向分割为4部分的4极使用一块铁芯,材料成品率从日产X-Trail混合动力车所用电机的22%提升至43%。
作为转子的层叠方法,每层叠一块在圆周方向分割为4部分的4极铁芯,就在错开1个极的同时进行“砖叠”,在层叠完成后,将各个极的内径部位朝轴向焊接连接起来。
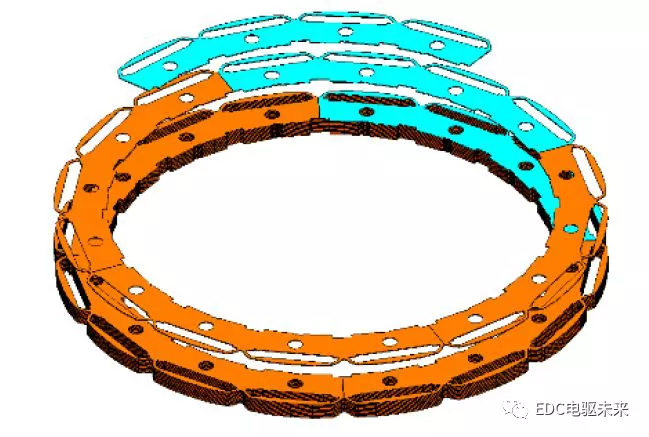
图12:分割铁芯转子的结构
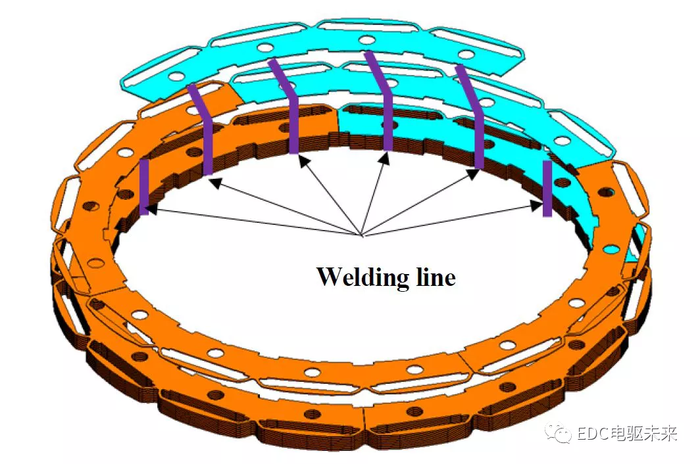
图13:分割铁芯转子的焊接部位
在分割铁芯转子的开发中,为了不仅确保暂时的旋转应力,而且还要确保耐用性能,实施了加减速耐用性测试(0rpm→最高转速→0rpm的重复变化),确认了因焊接强度不足而断裂的部位并采取了相应措施。
分割铁芯转子没有连接机构,仅通过焊接部位在轴向连接,旋转产生的离心应力集中在焊接部位,因此该部位的变化很重要。
图14的图片是完成加减速耐用性测试的产品的转子焊接部位,轴向端部(图片上方的一块)的焊接断裂。
当扩大焊接部位时,轴向端部的铁芯焊接宽度为1.3mm,比一般的1.6mm更窄。
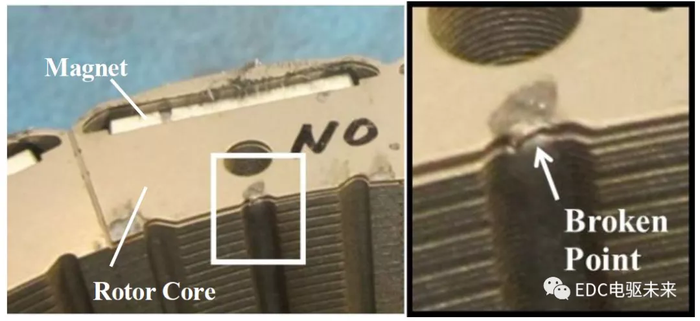
图14:加减速耐用性测试导致的焊接断裂部位
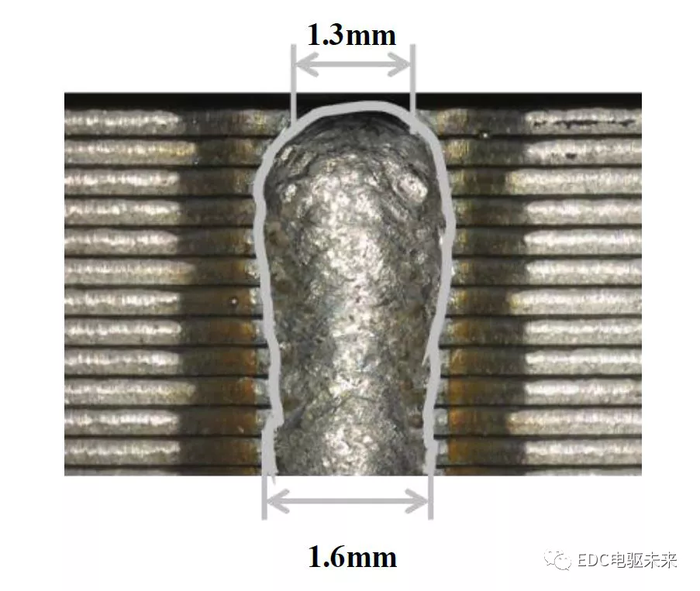
图15:焊接部位放大图
连接分割转子铁芯的焊接通过激光焊接实施,在激光焊接的开始位置——铁芯端部,通过圆形的激光照射使焊接宽度部分变窄,另外还有一个结构方面的因素是铁芯端部仅在一侧连接,对焊接施加的负荷会增加。
因此,我们改变了焊接的方法,采用的方法是不仅在内径部位轴向焊接(图16的A~B),而且仅端部在圆周方向上别的部位也追加进行了焊接(图C、D),解决了焊接强度和加减速耐用性测试的目标循环问题。
在量产工序中通过管理焊接深度和焊接宽度来保障焊接强度的质量。
在量产线中,对焊接的起点和终点进行调整,对焊接工艺的吸气管进行改良,所有焊接点均确保了1.33以上的工艺能力指数Cpk。
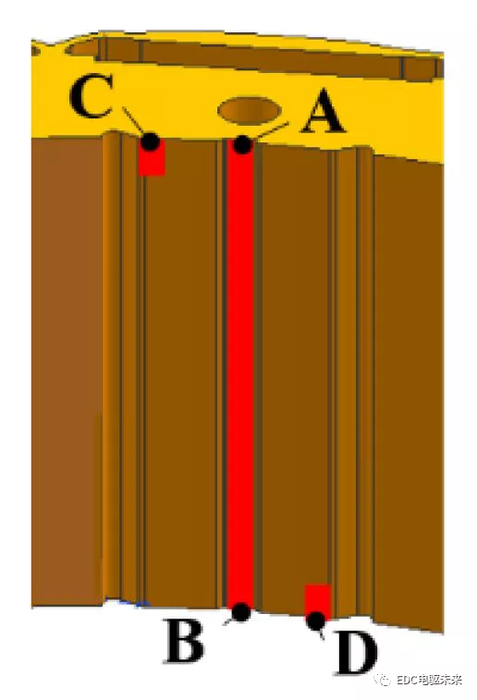
图16:焊接部位
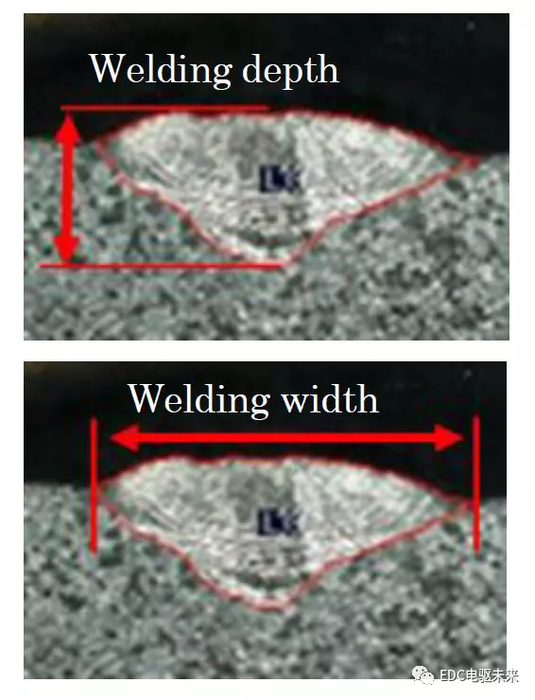
图17:焊接部位的横截面(焊接深度和焊接宽度)
与传统的秋季大会演讲一样,线上举行的演讲结束后也有问答环节,内容如下。
A:就强度而言,对于离心力的强度是最重要的,已经通过设计解决了这个问题。
A:如果增加分割数量就会提高成品率,但因为会影响到尺寸精度,所以分割成4部分刚刚好。
Q:分割时磁阻增加,扭矩下降,转矩脉动会如何变化?
A:扭矩略微下降,但不明显。分割部位由于是砖叠重叠的,因此不会影响转矩脉动(类似偏斜)。
Q:优化结构的做法是使用了优化模块还是根据经验技术进行的?
A:因为有基础部件——电机,因此利用经验技术的地方较多。
汽车技术会・2020年秋季大会学术讲座
获取更多评论