同步工程在新能源电驱动项目的开发与应用
作者:章毅 王平 李维虎
文章来源:AI《汽车制造业》
发布时间:2021-12-04
针对新能源电驱动开发进行同步工程分析研究,制定更为优化的工业化设计方案,可大幅降低新能源电驱动装配工业化的工具、设备及人力资源的投资成本,为后续机型的柔性化生产提供了项目经验和工艺基础。
新能源电驱动项目生产准备中同步工程(SE)的作用及意义越来越重要。装配同步工程是在新电驱动产品开发过程中,分别在概念设计阶段、工程设计阶段和工业化准备阶段(或后工程设计阶段),以电驱动产品为对象进行工业化分析的过程。
为了配合新能源电驱动产品项目开发,实现该机型装配工业化生产,本项目对该机型装配工业化同步工程分析开展了研究,通过SE分析提出更为合理的设计方案,并完成该新机型装配工业化同步设计,以达到降低生产成本、提高生产效率并提升产品品质的目的。
电驱动设计具有系统性和集成性,产品开发过程都需要各部门尽可能同步作业,实现产品开发过程的一体化设计,如图1所示。而装配因涉及的零件数量大、装配工艺复杂等因素,新能源电驱动同步工程会涉及到电驱动设计的各个系统,零件设计中的装配顺序、装配方法和装配空间等对电驱动工业化生产有直接地的影响。
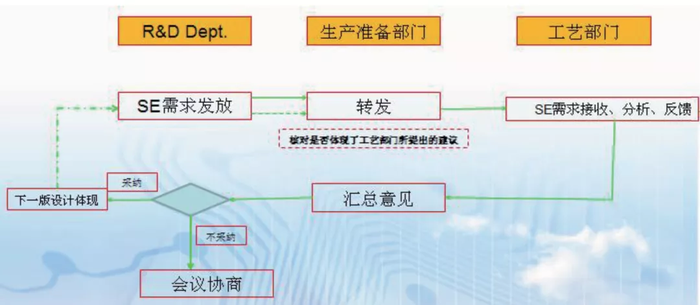
根据车型零件之间的装配关系、难易程度、实现形式等各种因素,定义出最优化的设计方案。
根据设计中零件在电驱动上的装配位置及装配方法的不同,分析该零件在装配生产线上的装配工位。在此过程中首先应确定零件安装点(转子、定子、合装热套及相关附件等),不同的安装位置对工序的编排、机器人PLC的编程、涂胶轨迹、总成测试及其他工艺布局有重大影响,如图2所示。
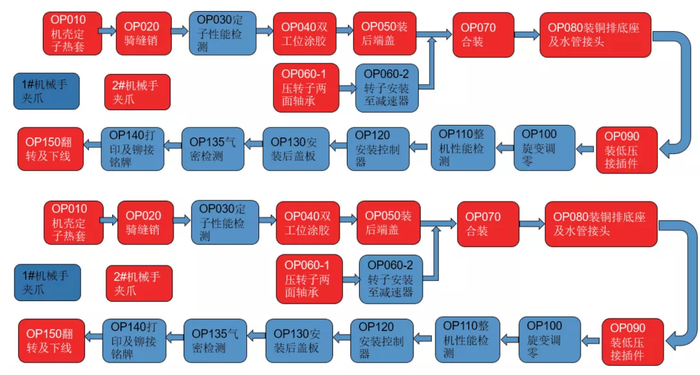
针对设计的零件来分析其装配的难易程度、装配空间等。如对于某款新机型减速器搬运工序,因机器人卡爪需适配两种产品的抓取工作,因此机械手卡爪需进行柔性化,增加快换压头尽快换销。对于一些需校核装配空间的情况,如某款新机型定子抓取热套的装配,应校核其装配时与周围环境件的位置关系,避免其放入时与环境件干涉,这一过程如图3、图4所示。
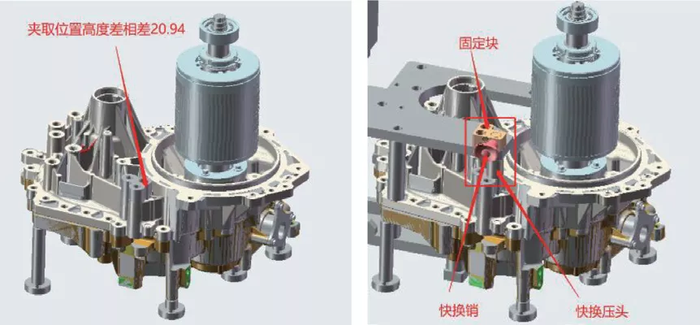
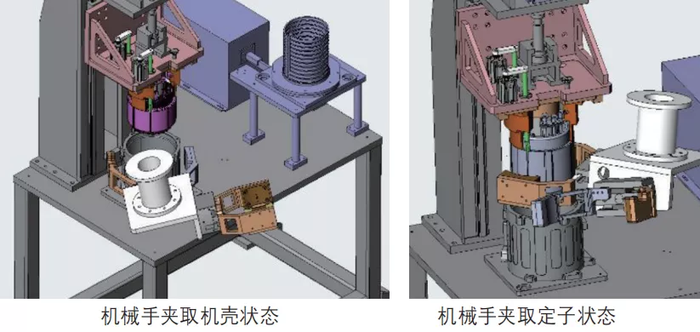
该阶段包括新车型工具操作空间校核分析、生产线适配性分析与定位公差分析。
利用计算机辅助程序对装配工具使用空间的校核分析。工具的操作空间直接影响到新机型在实际生产中零件的安装能否完成,对于校核中的工具干涉问题,工艺设计师与产品设计师共同制定优化方案,通过更改设计优化装配工具的操作空间,大幅减少特殊工具(特殊套筒、气动叉形扳手等)的投资。干涉主要分为工具与零件干涉(如某款新机型冷水管的安装)和工具与环境件干涉(如某款新机型后盖的压装)。
某款新机型冷水管的装配经SE校核分析,气动工具头与水冷管本体干涉约10mm,实际操作中气动工具将无法完成装配,按照图示环境须使用气动叉形电动扳手(特殊工具),增加工业化成本,通过设计反馈扩大水冷管Y向尺寸15mm(其中5mm为工具调整及零件误差范围),避免工具与水冷管Y向干涉,这样可使用普通拧紧工具紧固,降低成本。这一过程如图5所示。
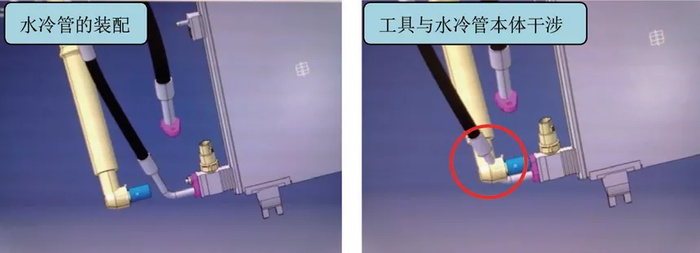
该处设计导致工具类型的选用受限,采用特殊头工具成本高(一把造价约8万元),而通过设计更改,采用普通拧紧工具紧固,成本低(一把造价约2万元)。某款新机型通过更改设计而减少特殊工具的使用约有10处左右,可节省车型工业化成本约60万元。
某款新机型后端盖压装经SE分析,后端盖与压装设备加强筋(环境件)干涉,后端盖无法正常放置到设备中,设备无法完成自动压装工作,而后端盖压装机构通过调整螺钉来调节后端盖压板的高度,避开干涉部位,有效地解决了端盖与设备加强筋的问题,如图6所示。
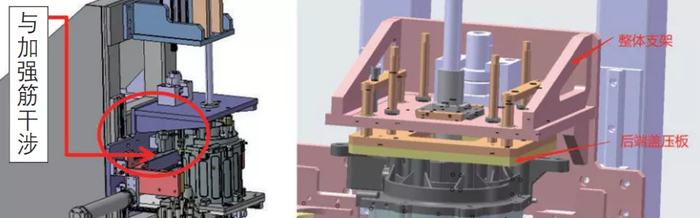
后端盖压装使用涉及到周围环境件的影响,部分零件安装空间不足须采用手动工具多次拧紧,通过新增整体支架及后端盖压装机构,大幅减少了总装装配工时,并且提升了产线的柔性化。某款新机型约20处可由扳手工具更改为气动或电动拧紧工具,单机装配可缩短至320s,根据年产量50000台计算,此项可降低约2.2个人力成本,按工人年薪3.5万元计算,可减少7.7万元。
新机型设计初期要以实际生产线为基础,符合生产线的基本约束要求。对于重要的定位设备,如定转子合装、转子轴承压装、后盖安装和总成翻转下线等,对电驱动尺寸的定位有特殊要求。因此设计的零件应有对应生产线的定位位置。气密检测及加注设备对于整机气密性等管口有匹配性要求,设计时应考虑将透气阀尺寸保持与设备一致。如图7所示,机械手夹持设备对于质量大的零件在设计时就应匹配。这样可避免增加新设备或者旧设备改造,大幅降低投资成本。
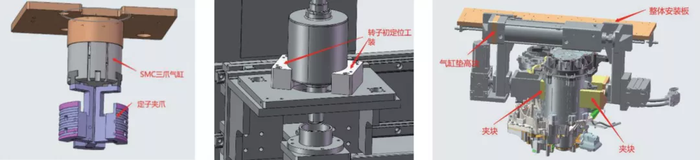
零件的定位、尺寸公差方案的确定直接影响到零件的装配难易度与装配质量。通过分析定位形式可以确定零件的装配方法。如圆孔和长圆孔定位,装配时必然是先预紧圆孔以预定位零件,再固定长圆孔。此外,部分零件结构需采用辅助定位形式,如增加定位销或者卡爪定位等。以上情况如图8所示。
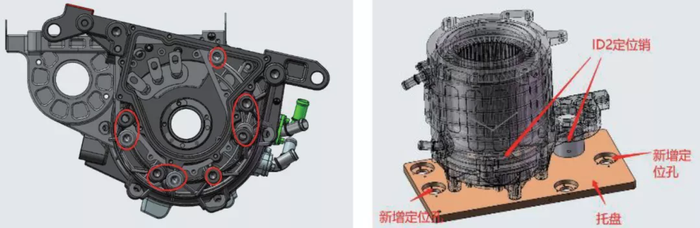
该阶段主要包含了制定装配工艺流程、工具的合理选用和工装的设计3个方面。
根据新机型较为完整的设计,以电驱动为对象,制定详细的电驱动装配工艺流程(图9)。根据电驱动数模分析,结合园区各线的工位,制定新产品电机各线工艺操作清单,编制初版装配工艺文件。对于设备限制的工位,定转子合装、转子轴承压装、后盖安装和总成翻转下线等,预先应该确定其装配工艺。
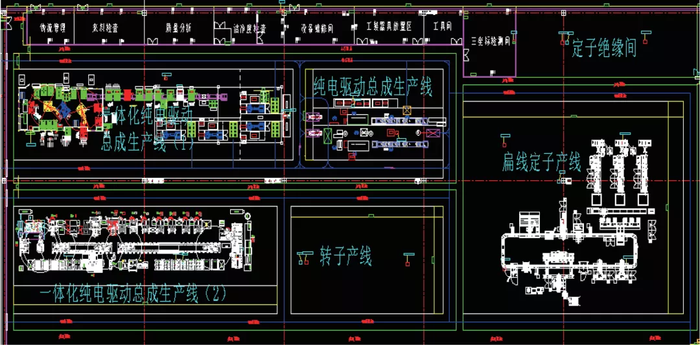
工具的规格(套筒的规格、紧固工具的选用等)各不相同,合理的选用工具能有效避免干涉及安装困难问题。根据标准件的不同确定装配套筒工具的尺寸,如M6对应规格H10的套筒;M8对应规格H13的套筒。根据力矩大小确定紧固工具的类型及规格,一般大于10N·m选用气动工具,小于10N·m选用电动工具。气动工具随着其定义力矩越大,所选气动工具的外廓尺寸也更大。根据紧固工具使用空间的不同,可以选用适当尺寸的套筒或者紧固工具,并采用CATIA建模形式。对于不同规格的工具进行模拟装配,以确定最佳尺寸规格的工具。
选用长度50mm的套筒,X向工具操作空间可预留约2mm,改选用长度30mm套筒,则空间预留约22mm,有利于工具正常操作,避免了因空间不够导致所选用工具无法使用的情况。
对于一些制造精度或者装配精度难以达到要求的位置,需设计采用合理的辅助工装定位。关键件的分装也需要有足够精度的定位。需要遵循六点定位原则,以保证总装装配精度。图10为某款新机型压装转子两面轴承的定位。
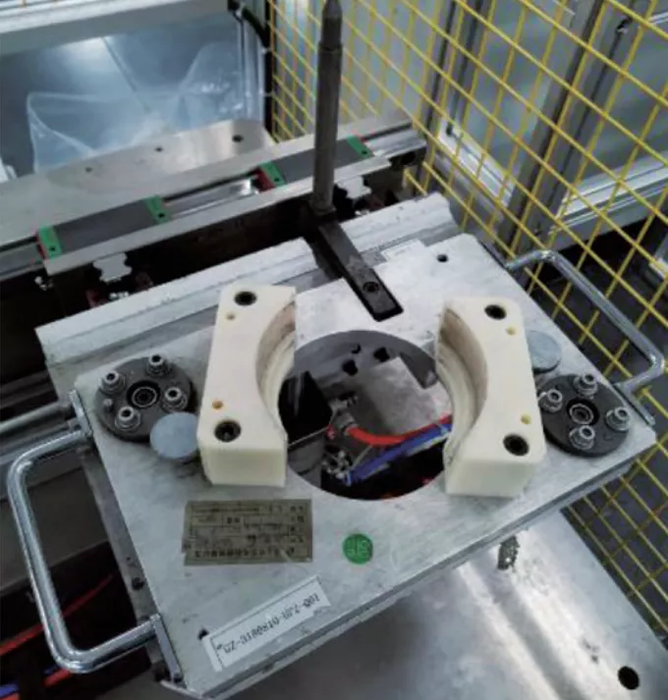
针对新能源电驱动开发进行同步工程分析研究,制定更为优化的工业化设计方案,大幅降低了装配工艺工业化的工具、设备及人力资源的投资成本,共计约节约成本107万元。与此同时为后续机型的柔性化生产提供了项目经验和工艺基础。
没有更多评论了