本文利用一维流体仿真计算软件Flowmaster,对某型柴油机增加高压燃油泵润滑系统进行仿真计算。通过对发动机的润滑系统设计方案研究,建立符合该发动机的润滑系统计算模型,计算得到稳态工况下该发动机滑油压力分布状况。通过计算分析认为该润滑系统的设计整改能够满足发动机的运行需求。
发动机的润滑是由润滑系来实现的。润滑系的功能就是在发动机工作时连续不断地将数量足够、压力和温度适当的洁净润滑油输送到运动副的摩擦表面,并在摩擦表面之间形成油膜,实现液体摩擦,从而减小摩擦阻力、降低功率消耗、减轻机件磨损,以达到提高发动机工作可靠性和耐久性的目的。
润滑系统压力分布是判断发动机润滑系统工作性能的关键参数,同时也是发动机安全监控的重要指标。如果发动机润滑系统油压过低,将会对发动机造成很大的损害,甚至会使发动机提前报废。
本文基于一维流体分析软件Flowmaster建立某柴油机润滑系统一维计算模型。通过对润滑系统计算结果的评估分析,为发动机润滑系统的设计提供理论支持。
为方便阐述,本文所涉及的压力均为绝对压力。
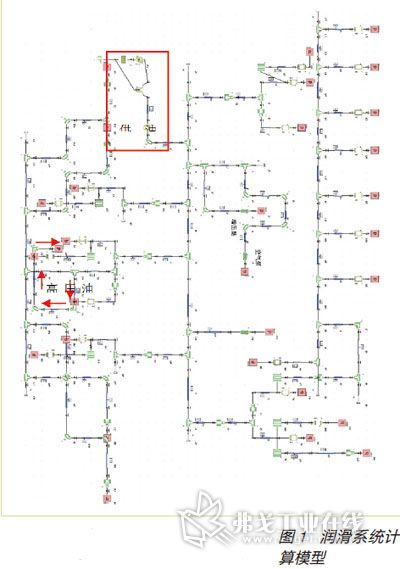
一维仿真模型的建立
根据润滑系统设计原理,利用一维流体计算软件Flowmaster搭建本文计算所涉及润滑系统,如图1所示。
整个润滑系统由供油系统和用油部件组成,用油部件主要包含主轴承、增压器、空气泵、真空泵和进排气凸轮轴等,其中以上所述部件均依靠供油系统提供的高压润滑油进行润滑,即所谓的“压力润滑”。
1. 模型解析
供油系统主要由油底壳、机油集滤器、机油泵、泄压阀和机油滤清器组成,其中机油泵是整个润滑系统的动力源,机油泵由发动机驱动,随发动机机转速的提升机油泵的供油能力增强。因此在发动机润滑系统分析中,主要考虑怠速工况时系统的油压能否满足发动机的运行需求即可。
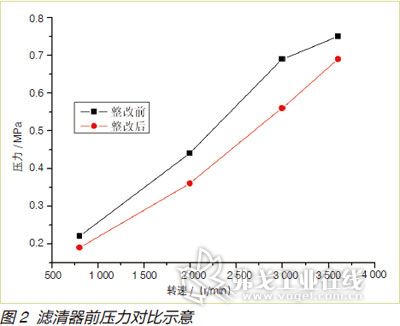
2. 参数确定
该柴油机机油泵为齿轮式机油泵,机油泵的供油能力为0.028L/r,机油泵与发动机的转速比为1:2。
增压器、真空泵和空气泵只需输入相关的机油流阻数据即可。
轴承类元件的直径和间隙会对机油的消耗量和系统的油压产生显著影响。
该柴油机活塞冷却喷嘴的开起压力为0.27MPa。
计算结果分析
根据该发动机的性能数据,本次分析主要对油温为80℃,发动机转速为800r/min、2000r/min、3000r/min和3600r/min时的工况进行分析。通过计算结果查看整改后系统的油压和机油流量的变化状况。
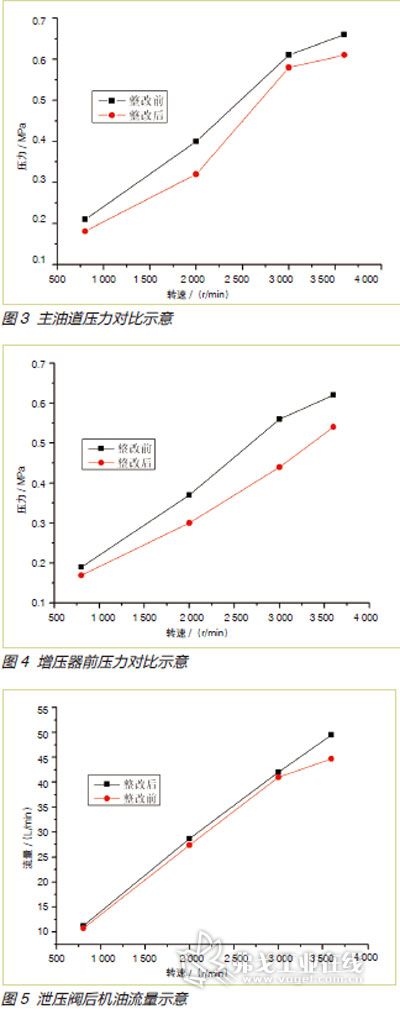
1. 压力计算结果
根据发动机润滑系统整改前后的设计方案,分别对两种设计状态进行计算分析,图2~图4分别为滤清器前压力对比、主油道压力和增压器前压力对比结果。
图3显示整改前后发动机额定转速800r/min时系统的主油道压力分别为0.21MPa和0.18MPa。而根据相关的评价指标,在发动机低速空转时,系统机油压力不应低于0.15~0.2MPa,从计算结果来看,整改后系统主油道油压与计算要求相当,根据计算经验该油压能够满足系统的运行需求。
从图4的油压对比示意图来看,整改后系统的油压均低于整改前系统的油压,主要原因是整改在原润滑系统上增加高压油泵出油孔,增加了系统的机油泄流量,故整改后系统的机油压力小于整改前。
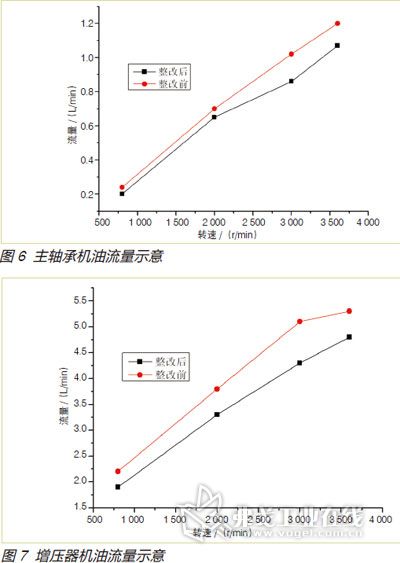
2. 流量计算结果
用油部件的机油流量也是考量润滑系统布置合理性的重要指标,图5~图7为本次计算润滑系统不同部位的机油流量。
从图5~图7可以看出,整改后系统的机油流量大于整改前,但是用油部件的机油流量小于整改前。主要原因是增加高压油泵出油口降低了系统的油压,发动机相同工况下系统油压降低则泄压阀的泄流量降低,从而整改后系统的总流量大于整改前;高压油泵支路分流了机油,且分流量大于系统的增加量,故系统各部件的机油流量均不同程度的减小。
从主要部件的机油流量来看,整改后系统的机油流量分布合理,能够满足发动机部件的润滑需求。
结论
计算结果表明:该柴油机润滑系统的设计能够满足发动机的运行需求,该设计方案可行。在润滑系统中增加机油润滑部件,将会降低系统的机油压力。因此,在润滑系统设计中应对润滑部件的泄流能力进行确认分析。在发动机润滑系统设计中,CFD分析可以为润滑系统的设计提供理论依据,保证设计工作的准确可靠。
评论 0
没有更多评论了