曲轴作为发动机核心零件之一,由于加工基准在曲轴中心孔和主轴颈间经常转换,产生基准不重合误差,再加上各轴颈加工精度高和轴类零件加工过程中刚性差的特点,是发动机本体五大件中加工质量最难保证的零件。
深滚压技术工艺背景
曲轴在工作中承受交变载荷,主轴颈和连杆颈圆角过渡处属于曲轴强度的薄弱环节,轴颈与曲柄臂过渡圆角在切削或磨削加工后刀痕存在应力集中,长期的高速旋转运转和较大的交变负荷应力将有可能造成曲轴圆角处产生裂纹或断裂。
在以往的工艺中,为了提高曲轴的疲劳强度,在曲拐半径一定的前提下,主要增加曲轴的主轴颈和连杆轴颈的直径,增加两轴颈的重叠高度或重叠面积来保证曲轴的疲劳强度。但是,这样会造成曲轴结构的庞大和重量的增加,不仅使材料的利用率低,同时也增加了发动机的重量,使发动机燃油经济性差。现在追求发动机的轻量化,很多曲轴主轴颈和连杆轴颈的重叠度减小,甚至重叠度为零或负重叠度,为了保证曲轴的强度,需要对轴颈和曲柄臂的过渡圆角进行处理。奇瑞发动机曲轴采用最先进的曲轴深滚压技术,使滚压后的曲轴圆角表面粗糙度小,滚压后表面形成一种硬化层和保持残余压应力等特点,对曲轴可以边滚压边矫直等特点,提高了曲轴整体疲劳强度。
深滚压技术的优点
使用深滚压技术,滚压轮在接触压力下沿着沟槽圆周方向移动,根据金属变形理论:零件表面在外力作用下,被滚压金属的原子间距离会暂时减小或晶粒间产生滑动,当外力达到一定数值时,被加工表面金属除产生弹性变形外,还形成塑性变形。由于塑性变形的产生,使零件被加工表面的形状、组织结构和物理性能都发生了变化,使金属被滚压层的组织变得紧密、晶粒变细、晶粒形状也沿着变形最大的方向延伸,在被滚压金属表层内产生一定残余压应力,使金属表面得到强化,提高了零件表层冷作硬化硬度,压平了微观不平度,降低了零件的表面粗糙度,被滚压金属表面的强度极限、屈服极限和疲劳极限都有提高。
深滚压加工特点主要有:圆角表面粗糙度低;曲轴整体疲劳强度得到很大程度的提高;成本低,生产率高,滚压过程中设备对曲轴滚压力进行监控,确保工件只有经过正确的深滚压后才被传送到下一工位,使设备开动率大于97%;磨削工序不用磨侧面和过渡圆角;边滚压边对曲轴进行校直(见图1),确保主轴颈跳动小于0.12mm,连杆轴颈的对称度满足磨削能力的要求。
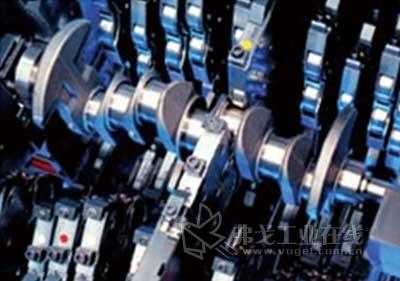
图1 曲轴滚压校直实体
1.滚压力
滚压力大小的设定决定了工件接触表面塑性变形量(工件材料的密度均匀性/有无疏松/硬度的均匀性也会对塑性变形有影响)的大小和工件表面残余压应力的大小,滚压力大小的设定主要取决于工件的材料、圆角的大小和发动机最大爆发压力,滚压力太小将达不到曲轴强化的效果,太大可能会压溃曲轴表面,降低曲轴的疲劳强度。奇瑞公司曲轴滚压力的设定是根据试验中心做抗疲劳强度,在疲劳试验机里施加800~900N.m的力,做上1千万次挤拉振动,试验后根据曲轴振动频率的下降检查圆角是否有裂纹确定滚压力的大小。
2.滚压的角度
滚压轮的压入方向和主轴颈轴线的夹角,一般根据各个厂家的设备和滚压轮大小而设定,奇瑞公司曲轴生产线滚压轮压入设定的角度为55°。
3.根据满负荷滚压力持续的圈数、滚压力的升压阶段和降压阶段等。
奇瑞发动机公司481H/484J曲轴,工件在放入滚压机床内进行滚压前,先利用激光进行扫描,扫描工件类型和工件摆放角度,便于滚压头准确抱合曲轴轴颈,圆角滚压满负荷滚压力持续的圈数为6圈,升压阶段和降压阶段各3圈,主轴颈每个单元的滚压力为18.5kN,连杆颈每个单元的滚压力是变压力的,在每个曲拐偏离曲轴中心在角度和距离上不同,滚压力从9kN到18.5kN变化着(见图2)。滚压后机床利用自动检测轴颈跳动功能,进行滚压校直功能,轴颈跳动低于0.12mm,机床进行打码标识,超过0.12mm,机床再次进行滚压校直。校直后再次进行检测,合格,打标记。
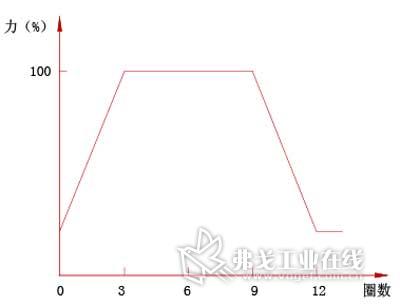
图2 深滚压压力参数变化趋势
4 .滚压后的效果
(1)滚压后工件的伸长量:由于工件在滚压中受到了轴向的作用力,且产生了塑性变形,导致工件的总长度会伸长,各个轴颈的开裆变大。工件滚压后的延伸量由产品和工艺根据工件材料的不同进行试验对比确定,目前奇瑞公司曲轴材料有球墨铸铁和锻钢等,两者的延伸量截然不同,球墨铸铁材料的曲轴在上述的滚压力作用下,每个轴颈轴向的延伸量约为0.06mm,锻钢曲轴每个轴颈延伸量约为0.03mm。
(2)滚轮的压入量(即圆角的塑性变形量)由滚压力大小、压入方向、滚压圈数和工件的材质特性决定,奇瑞发动机曲轴圆角的压入量通过轮廓度仪进行滚压前后的对比,压入量约为0.15mm。
(3)滚压后,轴颈的圆角粗糙度有很大提高,圆角粗糙度由车削的RZ20降低到RZ6.3,圆角的滚压与磨削后的轴颈光滑过渡,曲轴的疲劳强度增加。
滚压过程中质量控制
要从本质上控制滚压的效果就要在过程中控制滚压后的残留压应力,但是残留压应力的检测非常麻烦、耗时且成本很高,不能满足现场生产快捷方便的要求,残余压应力的检测只限于在产品开发或零件试验时完成。现场控制滚压的质量主要可以从两方面来检查滚压的效果:
1.滚压的被动参数。控制滚压力、滚压圈数和滚压角度,每月从生产线随机抽取1~2根曲轴做疲劳试验。
2.滚压的主动参数。生产过程中只控制滚压力、滚压圈数和滚压角度。曲轴在疲劳试验、发动机强化试验和整车试验合格后就固化滚压参数(滚压力、滚压圈数和滚压角度),控制滚压轮的压入量。
奇瑞发动机二厂曲轴生产线曲轴滚压采用HEGENSCHEIDT公司的滚压设备,整机由9个滚压单元对5个主轴颈和4个连杆轴颈同时进行滚压,装有滚压工具和压力传感器的前臂,带支持和导向滚子的后臂,通过闭合前后臂的气压、液压阀使前后臂夹紧曲轴轴颈,头架带动曲轴旋转,同时比例阀根据RTC的电信号加压进行滚压。工件由机械手上料,使用曲轴两端的中心孔定位,自动夹紧法兰径,激光探测器检测曲轴第二连杆颈高度来核对曲轴型号是否正确。滚压机床在设计中充分考虑到了生产的一致性问题,机床有对压力的双重检查保险机构,液压系统的压力控制和每个滚压单元的滚压压力实时监控,在滚压压力超过设置范围后,机床会报警。滚压完毕后机床检测装置自动测量曲轴各主轴颈的跳动量,若测量超差,机床中的RTC系统进行运算在曲轴的不同部位,施加不同的压力,对曲轴进行继续滚压校直,以达到工艺的加工精度要求,每一个滚压合格的工件会打上标记。在设备预验收时检测圆角的压入量,一般要求压入量不小于0.15mm。HEGENSCHEIDT拥有专门检测压入量的检测室,配备了专门的检测人员,其检测过程如下:先扫描未滚压的工件圆角轮廓,再扫描滚压后的圆角轮廓,把扫描后的轮廓放大40倍后对比测量圆角的压入量。由确定的压入量可确定一组滚压参数,如果这组滚压参数滚压过的工件经过疲劳试验合格,则可以固化这组参数。
结语
曲轴圆角滚压工艺是目前最为理想的强化工艺之一,它不仅能够显著提高曲轴的疲劳寿命(圆角滚压的曲轴疲劳强度约增加60%以上),而且还可获得较好的表面加工质量,经滚压加工后的圆角不必精磨,就可以满足表面质量要求,从而有利于提高生产率和降低加工成本。
评论 0
正在获取数据......