鉴于国内曲轴生产厂家大多采用单工位机床的现状,沈阳机床展开了对双工位曲轴油孔加工机床的研究,成功开发出了双工位曲轴油孔加工机床的自动上下料系统,有效解决了这一影响曲轴油孔加工效率提升的瓶颈问题。
曲轴油孔是发动机曲轴加工工序中的一个关键环节。目前,国外曲轴油孔最常见的高效加工方法是二支甚至三支曲轴油孔同时进行加工。由于此类设备需要进口且价格昂贵,因此,国内曲轴生产厂家大多采用单工位机床,用多台设备的加工方式来弥补曲轴油孔的加工效率。其缺点是需要增加车间的作业面积和劳动力成本。
双工位曲轴油孔加工机床的开发重点是解决工件的上下料及装夹定位问题,因为若采用人工完成二组四支曲轴的上下料,将会极大地降低机床的加工效率。基于这种市场需求,我公司在原有单工位曲轴油孔加工机床的基础上,开发出了双工位曲轴油孔加工机床,采用自动上下料系统有效解决了这一影响曲轴油孔加工效率提升的瓶颈问题。
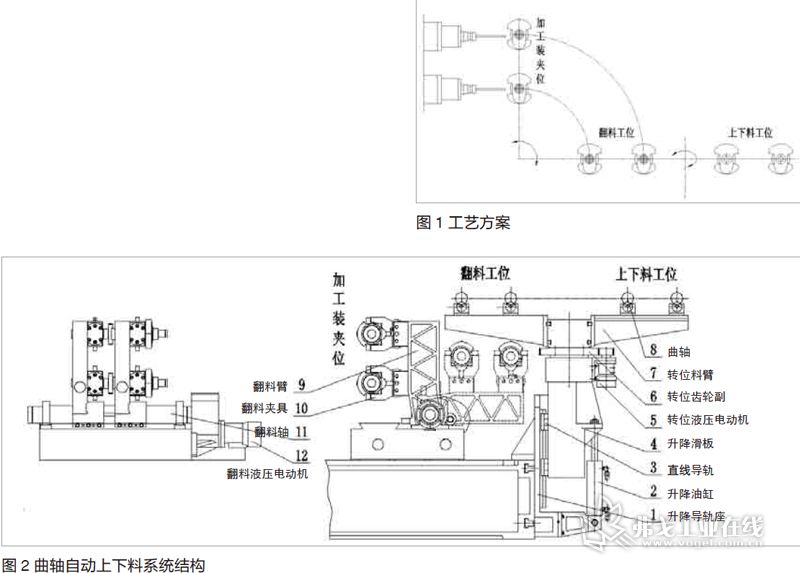
工艺方案分析
在双工位曲轴油孔加工时,曲轴需要上下装夹,而曲轴由人工或机械手摆放到上下料工位时,二支曲轴采用水平布置的方式比较方便,因此从上下料工位到装夹工位需要翻转机构将曲轴从水平位置翻转到垂直位置。同时,为了能够实现在加工时完成曲轴的上下料工作,需要将上下料工位设计成交换式,以提高设备的使用效率。双工位曲轴油孔加工自动上下料工艺方案如图1所示。
根据以上分析可知,如何将工件由上下料工位交换至翻料工位,如何将工件由翻料工位翻转至加工装夹区,如何避免工件交换机构与翻转机构的干涉问题,这些都是本方案的重点和难点。针对上面的分析,我们设计开发了具有升降功能的工件交换机构及具有夹紧定位功能的工件翻转机构。
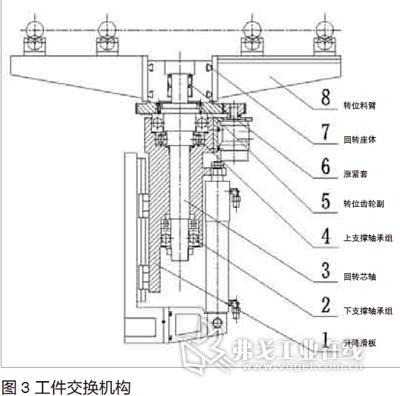
结构特点及工作原理
双工位曲轴油孔加工机床的曲轴上下料装置结构如图2所示,主要由升降机构、转位机构和翻料机构三部分组成。
上下料时,人工将曲轴放置在转位料臂的上下料工位上,安装在升降导轨座上的升降油缸推动安装在直线导轨上的升降滑板升起;升降滑板升起到位后,转位电动机驱动转位齿轮副回转,从而将曲轴由上下工位交换至翻料工位;曲轴交换至翻料工位后,转位托盘在升降油缸的驱动下下降,将曲轴落入翻料卡爪中;翻料夹具将曲轴夹紧后,翻料液压电动机驱动翻料轴及翻料臂回转,将曲轴翻转至机床加工装夹位后,完成机床的全部上下料动作。
该装置主要部件具有如下特点:
1.工件交换机构
如图3所示,工件交换机构主要由升降滑板、回转芯轴和转位料臂等部分组成。其中,回转芯轴通过上下支撑轴承组安装在升降滑板上,驱动芯轴回转的齿轮副安装在回转芯轴的法兰盘上,回转座体通过涨紧套安装在回转芯轴的端部。转位料臂通过T型块与回转座体连接在一起,转位料臂之间的距离可沿T型槽在回转座体的长度方向进行调整,以满足不同长度曲轴的上下料要求,具有很好的柔性。工件交换机构的升降及回转均配有开关到位检测,可以保证机床运转的可靠与安全。
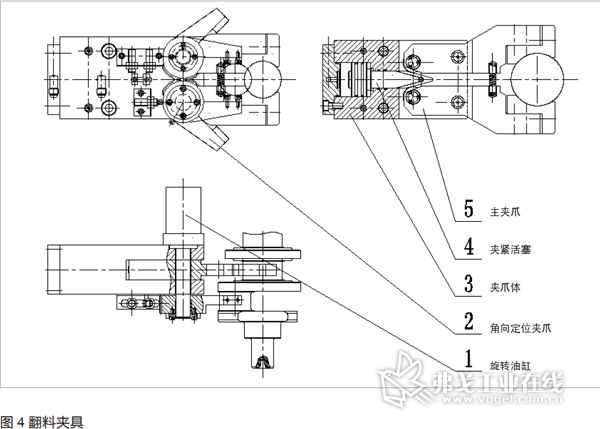
2.翻料夹具
翻料夹具(见图4)是翻料机构的重要组成部分,用于完成曲轴翻转上料时的角向定位及翻转夹紧功能,主要由角向定位及主夹紧二部分组成。角向定位夹爪及主夹爪均通过销轴安装在夹爪体上。角向定位夹爪由旋转油缸驱动,夹紧曲轴连杆颈完成角向定位;主夹爪由夹紧活塞驱动,夹紧曲轴的主轴颈完成翻转上料时的曲轴夹紧功能。角向定位夹爪及主夹爪均配有开关到位检测,可以保证机床运转的可靠与
安全。
结语
在设计之初,我们对曲轴油孔加工的工艺特点、加工要求以及具体的结构方案设计进行了充分的研究,因此,该曲轴自动上下料装置在实际使用过程中具有很好的柔性、可靠性以及使用精度,为双工位曲轴油孔加工数控机床的开发提供了成功基础,也为实现多工位曲轴自动化加工积累了技术经验。
该双工位曲轴油孔加工机床自动上下料装置的开发,在最大程度上满足了国内曲轴加工效率的同时,充分考虑了国内曲轴油孔加工设备的市场需求,在一定程度可上替代进口同类设备。
评论 0
正在获取数据......