本文阐述了EC系列发动机进气凸轮轴OP30工序中靶齿孔加工中存在的问题,并分析了问题产生的原因,制定相应的解决措施以降低了废品率,从而确保EC系列发动机进气凸轮轴零件能够有效的产出。
作为神龙汽车有限公司e动战略重要产品之一的EC系列发动机,与老款TU系列发动机最大的区别在于:前者配备CVVT连续可变气门正时系统,通过正时传感器识别凸轮的位置,然后信息反馈到ECU进行处理,来调节节气门的开闭时间。其中,装配正时传感器的耙齿采用压装方式压入进气凸轮轴小头端的正时标记孔(俗称“耙齿孔”),这里对耙齿孔精度要求十分高,小了不便于压装,大了容易导致耙齿的松脱,造成发动机故障。因此,提高耙齿孔加工精度、保证零件加工质量成为凸轮轴新项目进程中的一大难点。
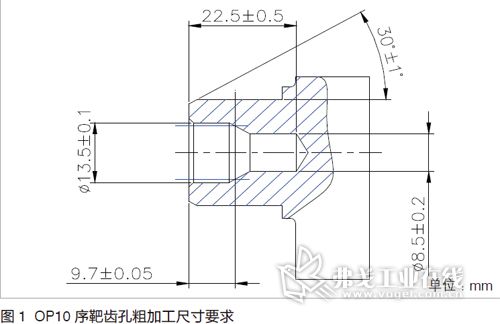
零件加工精度问题
1.耙齿孔加工尺寸过大
耙齿孔在OP10序中进行粗加工,尺寸为φ(13.5±0.1)mm,如图1所示。在OP30序中通过φ14mm铰刀对耙齿孔进行精铰,工艺要求的尺寸为φ14H7,如图2所示。由于种种原因,该孔在精加工工序一直存在加工尺寸过大的问题,从而导致生产车间不得不对零件进行100%检查,不仅严重制约了EC发动机新项目的进程,而且由于检查工具的磨损及其他因素,也导致了极大的质量隐患,增加了工废和加工成本。
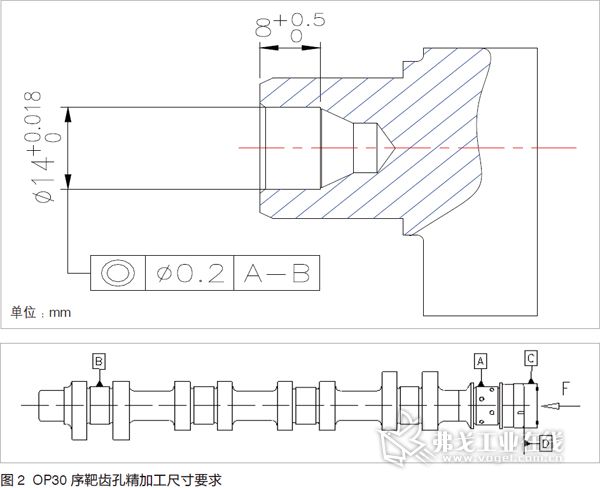
2.同轴度不稳定
从零件图样(见图2)可以看出,耙齿孔在同轴度方面有一定的要求,它是以凸轮轴第一、第五主轴颈形成的轴线作为定位基准。虽然同轴度的要求设定精度不算太高,为φ0.2mm,但是在加工过程中也时常出现同轴度不合格的情况,导致更多的工废,并且这种加工缺陷目视难以发现,所以目前所制定的临时措施是每30件一送检。这样不仅增加了质量控制的难度,而且严重制约了生产的加工节拍,同时也给操作工及3D间带来了更多的劳动负荷。

产生问题的可能性分析与改善
1.导致铰孔过大的因素及改善
(1)设备精度方面的影响
出现铰孔过大的现象,首先考虑是否由于设备精度的丧失,导致了零件加工精度的不合格。所以,我们先从设备精度的检查和调整着手,以便寻找加工稳定性不足的原因所在。
首先,检查主轴跳动是否合格。通过打表检查主轴锥度适配器的锥面及端面跳动,发现锥面跳动偏大,于是对主轴锥度适配器的跳动进行调整。调整前后的精度记录如表1所示。由此可知,调整后的精度完全符合设备要求的理想精度,生产跟踪发现加工状况明显好转,不合格率有一定的下降,但是仍有铰孔大的现象存在。
其次,主轴锁刀夹紧力方面的检查。主轴锁刀的夹紧力不足会使刀具装夹到主轴后产生较大的跳动。利用OTT主轴夹紧力检测器对主轴锁刀的夹紧力进行检查,测得主轴拉刀力为10.4kN,远远低于夹紧力的下限值12.6kN。为此,我们重点对OTT夹紧拉爪和碟簧进行了检查,发现夹紧拉爪已经磨损,碟簧也已经老化。更换OTT夹紧拉爪和老化的碟簧后,重新检测夹紧力为13.6kN,符合标准值规定的(14.5±1.5)kN。装夹HSK50A专用主轴芯棒,打表部位如图3所示,跳动调整前后数据如表2所示。
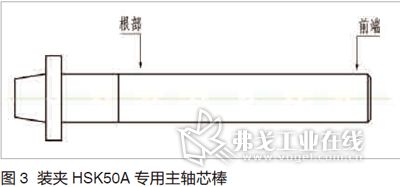
通过以上一系列的调整,主轴精度基本恢复了原有的状态,满足设备精度要求,零件加工质量得到了明显的改善。
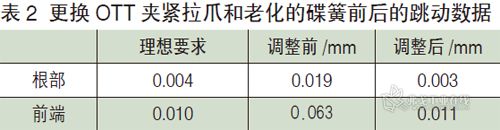
(2)切削液的影响
当设备精度保证后,加工产生的废品率得到明显的控制,但是生产线上每班还是会有1~2件零件加工尺寸过大。通过生产跟踪观测,每当加工偏大的时候,刀具或者刀柄与锥度适配器贴合面都会有铁屑存在,从而导致刀具在加工中产生这种不稳定性跳动的可能性增加。我们分析认为,以下两个方面可能会影响切削液的效果:一是,切削液过滤是否有效;二是,切削液压力及流量是否满足冲屑及刀具和主轴的冷却要求。
为此,我们首先检查了切削液过滤器。该过滤器采用SMC的筒式过滤器,过滤精度10mm。检查发现过滤桶底部沉积了大量的铁屑,从而反映出过滤系统的失效,导致了冲刀和主轴冲洗不干净。通过对过滤器结构进行优化,使密封有效,防止脏的切削液未通过过滤器进行有效过滤进入机床,从而完成了对切削液洁净度的确认。然后,我们对切削液压力及流量进行检查、确认。通过压力传感器观察,切削液压力为2MPa,流量为15L/min,完全符合机床设计需求。
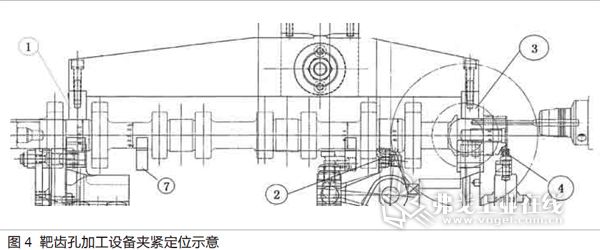
(3)加工参数的改善
从铰刀加工的特点来看,可以考虑对耙齿孔加工工艺进行优化。首先,考虑主轴转速对加工质量的影响。通过降低一定的主轴转速可以减少积屑瘤的产生,从而使加工孔的质量有一定好转,故将铰刀加工转速从1000r/min调整至800r/min,跟踪加工孔的不合格率有一定的下降。其次,考虑到加工工艺为法国PSA的成熟工艺,已经实现了量产化,并且加工余量单边为0.25mm,已经足够,故未在加工余量方面进行优化。
(4)刀具优化
铰刀的齿数影响铰孔精度、表面粗糙度、容屑空间和刀齿强度。由于加工零件材料为铸铁,为了提高铰孔精度,从而选择较多的齿数。在常用铰刀直径8~40mm范围内,一般取齿数4~8个,这里采用六刃铰刀。
铰刀直径公差直接影响被加工孔的尺寸精度、铰刀制造成本和使用寿命。铰孔时,由于刀齿径向跳动以及铰削用量和切削液等因素会使孔径大于铰刀直径,称为铰孔“扩张”;而由于刀刃钝圆半径挤压孔壁,则会使孔产生恢复而缩小,称为铰孔“收缩”。一般“扩张”和“收缩”的因素同时存在,最后结果应由实验决定。经验表明:用高速钢铰刀铰孔一般发生扩张,用硬质合金铰刀铰孔一般发生收缩;当铰削薄壁孔时,也常会发生收缩。
铰刀的公称直径等于孔的公称直径时,铰刀的上下偏差则要考虑扩张量、收缩量,并留出必要的磨损公差。因此,最初我们采用的铰刀公差的上偏差为+0.015mm,下偏差为+0.003mm。为了降低因加工过大导致的废品率,并且不影响使孔不至收缩而太小,所以将铰刀公差优化为上偏差0.009mm,下偏差为+0.003mm。
2. 同轴度不稳定的分析
(1)上道工序的零件尺寸对同轴度的影响
从图2可以看出,同轴度这个尺寸定位是以凸轮轴第一、第五主轴颈的轴线为基准,测量耙齿孔。因在OP30序中第一、第五主轴颈还未进行精加工,只是精车,所以该尺寸和第一、第五主轴颈的尺寸等相关。
在调整同轴度前,首先检查并调整OP20加工的零件符合工艺要求,并尽量控制第一、第五主轴颈的直径偏差在同一方向,且偏差相差不大(最好控制在0.03mm以内)。然后,检查第一、第五主轴颈的径向跳动,调整OP20的加工机床,控制在工艺要求的最小值,这样有利于调整OP30。
(2)OP30夹具的影响
设备在加工耙齿孔时两顶尖后退,以第一、第五主轴颈定位,辅助夹爪夹紧,工作台旋转90°后进行加工,如图4所示。其中,影响最大的是参与定位的第一、第五主轴颈定位块。如果此定位块磨损,将直接造成零件轴线的高低变化,导致零件轴线与主轴轴线不平行,加工出来的零件同轴度超差。
调整前,首先更换新的定位块(注意备件尺寸,最好检测定位块的尺寸确认符合图样要求),安装样件,夹紧样件,在主轴上架表,旋转工作台,使样件与主轴平行,检查样件的上母线和侧母线,要求小于0.02mm/300mm;调整的部位有定位块、工作台的旋转角度等。此外,还要注意的是图4中的夹紧块①和③是否有异常磨损,并及时更换;夹紧臂的工作状态是否正常、压紧力能否有浮动等。
(3)其他因素的影响
机床坐标检查,加工靶齿孔时主轴的(X轴、Y轴)坐标要与零件的轴线同轴,即在主轴加工位置检查,在主轴上架表,旋转主轴,检查零件是否与主轴同轴。如不同轴可适当调整X轴、Y轴坐标,保证同轴度在0.05mm内。
结语
本文针对EC凸轮轴靶齿孔加工中存在的问题从设备、工艺参数、刀具和切削液等方面进行了分析和研究,并逐一进行改善,从而彻底解决了靶齿孔加工不稳定的问题。本案例的经验和方法可推广到其他轴类零件孔的加工分析中,对设备加工以及调整有一定的借鉴作用。
评论 0
正在获取数据......