浅析焊装生产线防错系统
文章来源:AI《汽车制造业》
发布时间:2021-08-10
为了防止白车身在焊装时发生漏焊、错焊、混装和漏装,需要建立模块化、精益化和敏捷化的防错系统,需要对制造过程进行有效的风险分析,建立并维护从识别问题到控制潜在影响的严密的 " 风险预防 " 防错管理体系,确保制造过程的系统性、完整性、可靠性和有效性,达到提升产品质量的目的。
为了防止白车身在焊装时发生漏焊、错焊、混装和漏装,需要建立模块化、精益化和敏捷化的防错系统,需要对制造过程进行有效的风险分析,建立并维护从识别问题到控制潜在影响的严密的 " 风险预防 " 防错管理体系,确保制造过程的系统性、完整性、可靠性和有效性,达到提升产品质量的目的。
随着自主品牌汽车销量日益增长,汽车制造面临很多的产品质量问题。召回及索赔保证了消费者的利益,也使得汽车生产企业的质量意识及责任意识有所提高。为了将汽车产品的质量水平提升上去,应采取防错技术,争取用最低的成本将这些问题处理好,达到零缺陷的目标。
防错不是找出错误,而是防患于未然,减少风险和损失,提高产品可靠性,因此,需要从产品策划就开始考虑防错。
(1)产品策划时从零件自身形状及装配方式出发,考虑并解决后续生产时可能出现的错误。
(2)工艺规划时从设备及工艺布置出发,考虑并解决后续生产时可能出现的错误。
(3)通过生产组织及人员培训,解决后续生产时可能出现的错误。
(4)错误出现后,通过下工位装配能发现,或通过点检能发现,且返工量不大,确保损失最小化。
焊装防错的工艺开发流程有 6 个阶段(图 1),包括:焊装工艺策划防错、焊装工艺分析防错、焊装工艺设计、焊装设备工装开发,焊装工艺验证、焊装工艺优化及维护。本文主要介绍焊装防错工艺开发流程的前 4 个阶段。
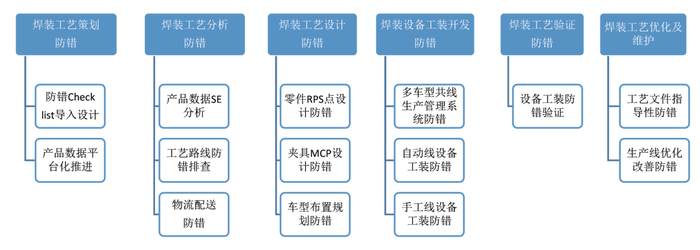
▲图 1 焊装工艺开发流程六个阶段防错
焊装工艺策划阶段的防错,首先需将防错Check list 导入设计,然后根据类别对零部件进行分类管控,分别采取不同的技术策略。
(1)相像(高难度识别):零部件结构相似,局部型面有变化,即使放在一起也难以识别,只能通过检具或三坐标识别;
(2)相似(难识别):结构有不同,差异较小,不放在一起无法识别;
(3)相近(易错装):零部件虽在结构、大小上有不同,但差异较小,有识别特征,但不明显,不能快速、清晰识别,容易混淆。
a.LH/RH 或 L/R :左 / 右识别标识(如铰链、支架等);
b.1、2、3…或 A、B、C…:连续件标识(结构上接近的多个零件);
c. 箭头 : 向前或向上标识(结构上接近对称的零部件);
e. 结构防错。标识防错只能从识别上防错,结构上防错才可以实现真正的装配防错。
通过 CPS 等通信网络将工厂内外的事物和服务连接起来,实现整个社会资源的优化和共享,创造前所未有的价值,构建新的商业模式,从材料、制造到消费的全产业链网络标准。
零件 RPS 设计要在零件模具、检具开发设计之前考虑零件搭接关系,尺寸控制重点部位,合理设计零件定位,避免车身精度受零件转配累计尺寸偏差影响。
夹具 MCP 设计在夹具开发前期阶段应考虑每个零件定位防错要求。
焊装产线布置规划要从产线区域布置,考虑零部件的上线防错顺序。
手工线设备工装防错主要考虑手工夹具防错、零件防错、焊接设备防错。其中夹具定位设计不仅要满足 MCP 要求,还要满足对相似件差异部位做定位设计。
a. 车型参数防错:采用手动旋钮切换 4 种车型按钮,每种车型采用不同颜色的指示灯显示,可以独立切换 16 个焊接规范,有效控制不同车型之间的焊接参数防错。
b. 车型配置防错:A 与 B 手工分装线,共用夹具较多,一个总成件上局部零件存在差异,需要对差异零件做车型气路切换(A 夹具气路防错改造有 30套左右)。
c. 焊点数量防错:采用焊点计数器,可以有效控制工位焊点数量(不漏点、不多焊焊点)。
a. 近距离防错:接近开关零部件差异部位在工装的下方,取件方向背向传感器,可以在工装部位增加传感器支架,安装接近开关。
b. 远距离防错:激光传感器零件差异部位在工装的上方,而且是取件的方向,传感器支架无法安装,因此采用激光对射的方式。
c. 非金属件防错:视觉检测车身胶块是塑料件,一般的光点开关检测不到,需要通过视觉拍照成像比对数据,判断是否遗漏或错装。
d. 涂胶检测防错:视觉检测机器人涂胶是没法识别涂胶位置及尺寸大小的,普通的传感器也无法检测固态的胶体,需要对机器人涂胶设备上增加视觉检测,在涂胶的过程进行防错确认。
e. 尺寸较小难识别零件防错:视觉检测侧围外板 A 柱焊装冲孔φ4 mm 孔(6 个),普通的检测设备无法识别,采用视觉检测设备可以在线检测防错。
f. 尺 寸 一 致 性 防 错:在 线检测与生产线共线,检测工位和生产线连接,根据检测频次要求和内容确定是否需要进入检测位,测量完成后,车身正常返回生产线。
多车型柔性化生产管理规划方式,由车间 MES 系统下发计划给生产管理系统,生产管理系统分配车型信息,传递给各区域PLC 系统,PLC 系统将车型信息转换设备层识别代码,自动切换设备程序。

▲图 2 机舱区域系统防错
①纵梁 10 工位员工装配纵梁时,将 EMS 下发的车型信息码贴在纵梁上;
② ER10PD 工位在上纵梁之前,扫描车型码信息,传递给上位机,上位机再转换数据给机舱PLC 程序;
③ PLC 接受上位机信息发送型号给 ER05 工位,ER05 工位液晶屏显示上件车型配置,同步将车型型号传递给夹具;
④ ER05 形式车型配置,指导员工应配置的零件,车型共用夹具,信号传递给车型传感器,识别装配后的件是否正确,不共用的夹具,直接从库位切换夹具;
⑤ ER05 装配完成后,将车型配置发送给ER10工位机器人,机器人调用匹配的车型焊接程序进行焊接;
⑥后一工位保持一致的车型传递方案,传递工位车型配置信息、夹具车型信息、机器人车型焊接程序,直至机舱总成下线。

▲图 3 侧围区域系统防错
①机舱通过 APC 输送,在下线之前,自动扫码枪读取车型配置,传递给 SB 区域液晶屏形式上件车型配置,及 SB10 夹具车型切换、机器人车型程序;
② SB10 工位显示屏显示车型配置,指导员工上对应的配置零件,车型夹具、置放台接受信号后,通过不同车型传感器识别装配后的件是否正确,机器人接收型号后,调动匹配车型程序进行焊接;
③ SB10 焊接完成通过,将车型信息通过辊床输送传递给下个程序 PLC 系统,调动相关的夹具、置台和机器人相关的车型信息,调用车型程序,可以通过传感器识别传递的车型是否与车型配置一致,后续持续保持此种传递方式,直至侧围下线。

▲图 4 主下线区域车型防错
①机舱通过 APC 输送,在下线之前,自动扫码枪读取车型配置,传递给 UB/MB 区域液晶屏显示上件车型配置,及 UB10夹具、零部件放置台车型、机器人车型程序切换;
② UB10 工位显示屏显示车型配置,指导员工上对应的配置零件,车型夹具、置放台接受信号后,通过不同车型传感器识别装配后的件是否正确,机器人接收型号后,调动匹配车型程序进行焊接;
③ UB10 焊接完成通过,将车型信息通过辊床输送传递给下个程序 PLC 系 统, 调 用 车型程序,可以通过传感器识别传递的车型是否与车型配置一致,后续持续保持此种传递方式,直至车身下线。

▲图 5 主线区域系统防错
①侧围与下车型匹配 UB10 发送车型信息,侧围通过 EMS 小车传递车型信息与下车体匹配);
② 侧围下线工位将侧围抓取至 EMS 小车,同步将侧围配置信息通过 RFID 读取码,写入EMS 小车载码体上;
③ EMS 小车输送侧围至主线合拼工位,总拼工位读码,根据下部车型配置信息,读取侧围总成是否与下部车型配置匹配;
④ 侧围匹配一致后,进行装配焊接,若不匹配,小车放行不一致的侧围,直至匹配到一致的侧围进行装配。
在汽车制造过程中,防错技术的合理有效运用具有十分重要的作用。由于汽车零部件的质量直接影响到汽车的质量,为避免出现质量问题,制造过程中的防错应重点放在关键零部件上,采取先进的防错检测方法,加强对制造过程的控制,才能实现汽车的零缺陷。
防错不是找出错误,而是防范于未然,减少风险和损失,提高产品可靠性。采用多方论证的方法,能够发挥集体的经验与智慧,多站在顾客的立场上对产品设计、制造过程设计中的失误进行评定。经验积累,为以后的设计开发提供宝贵的参考。
正在获取数据......