动力电池 CTP 结构需要什么样的结构胶粘剂?
作者:胡东昇 徐多文
文章来源:AI《汽车制造业》
发布时间:2022-01-14
随着新能源汽车的快速发展,其中又以纯电、混合动力电动汽车为主,新能源汽车的核心部件——动力电池也在快速发展变化,结构胶的应用逐渐得到重视。
在电动汽车发展的前几年,动力电池是由数个或数十个电芯(包括圆柱形电芯、方形电芯及软包电芯)组装成模组,再由数个模组组装固定于PACK壳体中,形成汽车动力电池包。
这种结构由于有模组的存在,机械连接固定都比较方便,结构胶的应用并不十分必要。
近些年,由于电动汽车轻量化及长行驶里程的趋势压力,CTP结构应运而生。CTP结构提升了电池包的体积/重量能量密度,进一步延长了车辆续驶里程。
CTP结构是指动力电池包是由电芯(特别是方形电芯)直接组装到PACK壳体中(celltopack),这种结构省却或大幅度减少了中间模组部件,大大减轻了电池包的整体质量,直接为电动汽车的轻量化和续驶里程做出了贡献。这种CTP结构的电池包,一般需要大量使用胶粘剂来连接固定电芯,而无法使用传统的机械连接方式。
胶粘剂在动力电池CTP结构中的作用是非常重要的,用于CTP的胶粘剂有两大类现实需求:第一类就是以结构粘接为主,兼顾一定的导热作用;第二类就是以导热粘接为主,胶粘剂应用的目的是将电芯工作时产生的热量导出到外部的散热部件,实现热管理的部分功能作用,兼顾结构粘接要求。
这篇文章我们主要探讨第一类结构粘接的具体性能要求。这一类的结构胶粘剂必须起到把电芯与PACK壳体可靠连接、固定的作用,代替原来模组结构的机械连接。
由于整体PACK以及内部结构的可靠性、稳固性来自于结构胶的粘接连接,代替了原有的机械连接方式,因此结构胶的粘接强度及本体强度就要求有比较高的指标,一般来说8MPa以上,甚至更高的强度是很有必要的。这样高强度的结构胶应用于方形电芯的侧面或底面,根据电芯从尺寸及外形不同,一般粘接面积可以达到3000mm2以上,单个电芯粘接力可达24000N以上,有的特殊形状的方形电芯可以让粘接面积达到17000mm2,理论上单个电芯粘接力甚至可以达到136000N以上,较好地满足电芯直接稳固固定在PACK壳体内的要求。结构胶的强度衡量可以是对接拉伸强度或者是搭接拉剪强度。
要想使电芯获得高的固定粘接力,不仅要有结构胶本身的较高的拉伸强度以及更大的粘接面积,还要有对粘接材质的适应性,以及考虑被粘接材质的本体强度。
那么CTP结构的动力电池结构胶适用于哪些材质呢?首先看一看方形电芯的材质:方形电池的壳体一般使用3003铝合金。为了使电芯外壳具有绝缘性,大部分电芯生产厂商采用PET薄膜包覆或半包覆方形电池的外壳(图1);还有一种是采用绝缘粉末涂料(喷粉)的方式在电芯外壳涂覆一层绝缘涂层,见图2。
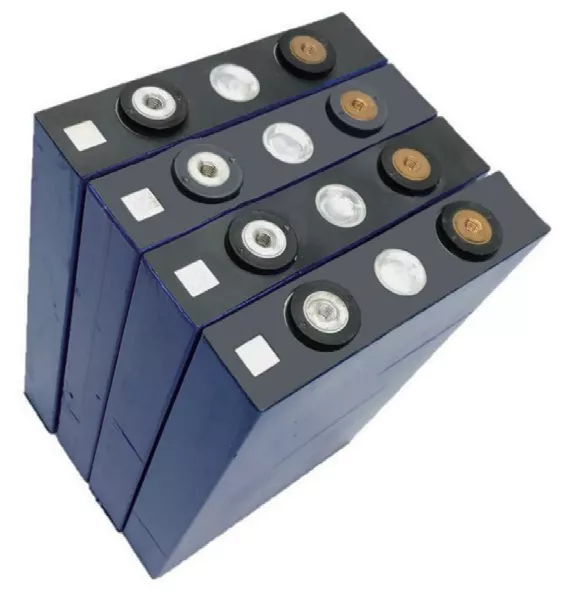
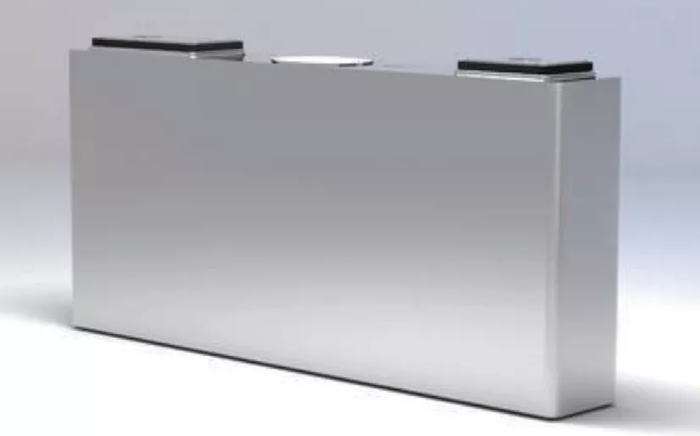
这两种电芯的表面材质以及相对应的PACK壳体或绝缘膜就是结构胶粘接的对象:PET(又称蓝膜)、喷粉涂层(环氧或其他树脂)及3003铝合金。结构胶必须对这几种材质具有良好的粘接性能。
由于PET蓝膜一般采用压敏胶背胶的方式将PET蓝膜包覆在电芯壳体外,或者采用热缩方式套在电芯壳体上,那么结构胶对于PET蓝膜(一般要经过等离子或火焰预处理)的粘接要能够保证粘接强度大于PET蓝膜的背胶与电芯铝合金壳体的粘接或者能够达到PET蓝膜破坏的强度。
对于3003铝合金以及喷粉涂层的粘接,要能够达到破坏时的内聚破坏,换句话说就是粘接胶层的破坏,而不是粘接胶层与铝合金或喷粉涂层的界面脱开。
动力电池PACK装载于汽车上,行驶中难免会受到颠簸、冲击及振动等,电芯的固定粘接也要承受挤压、剥离、弯曲和疲劳等各种力的考验。
粘接可靠性不仅取决于粘接强度,在受到冲击振动时,粘接胶层的柔韧性更重要。结构胶的柔韧性可以从两个方面来考察。
一是断裂伸长率:断裂伸长率是指胶粘剂本体在拉伸后断裂时的伸长长度与拉伸前长度的比值,用百分率表示。这一技术指标表征的是胶粘剂本体在受到外力作用时能够承受的受力变形能力,更高的断裂伸长率意味着可以抵御更大的受力变形。断裂伸长率达到100%,甚至≥150%就是这一期望的具体体现。
二是弹性模量(储能模量):这是反映材料抵抗弹性变形能力的指标,表征了材料存储弹性变形能量的能力,单位是MPa,是应力与应变的比值,其值越大,使材料发生一定弹性变形的应力也越大。
对于动力电池的电芯粘接可靠性,往往需要进行有限元分析,计算机模拟分析时一个重要的输入指标是模量(或泊松比)。因此,模量就是一个非常重要的指标。
储能模量的测试采用动态热机械分析仪(DMA)较为准确。
在CTP结构胶的工程应用中,低模量是更期望的特性。结合第一点的强度要求,低模量与高强度是有一定的相互克制的。有公司及一些标准储能模量(常温)要求低于800MPa,甚至个别的结构胶要求低于300MPa。
汽车的长期可靠运行的基本要求,传递到动力电池,CTP结构中结构胶的耐老化特性同样重要。对于胶粘剂来说,耐老化特性可以通过冷热循环和湿热老化测试来考察。可以参照GB/T7124的相关规定测试。
耐冷热循环测试不同的汽车厂家或标准有不同要求,老化条件参考汽车常用的耐老化测试方法,可以在-40~80℃(或90℃)高低温交变循环,单次循环模式见图3,循环次数可以由电池包设计及胶粘剂供应商双方商定。
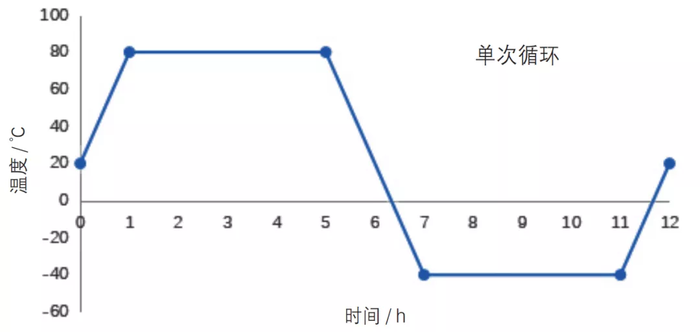
耐湿热老化,一般是“双85”(85℃,85%相对湿度)条件下,1000h老化。耐老化后的性能指标与初始指标进行比对,不小于70%。
结构胶应用于动力电池,作为汽车动力电池材料的一部分,阻燃性是基本的要求。阻燃测试考虑其应用环境,采用铝—胶—铝三明治结构胶层厚度0.5mm进行测试,要求达到V0级。可以按照GB/T2408的规定进行测试。
结构胶直接应用于电芯粘接,绝缘性也是基本要求,介电强度要大于10kV/mm;体积电阻率要大于1×1012Ω.cm。可以参照GB/T1408的相关规定测试。
对于高强度低模量的结构粘接胶,一般不考察其导热特性。
在动力电池PACK系统中,热管理是非常重要的一个子系统,电芯的热量需要能够及时散发出去,保证电池在最佳工作温度范围内,这时需要专门的导热材料(如导热胶)发挥这个作用,它的主体作用与我们前面探讨的结构胶是不一样的,它重点考察的是导热性能。当然,结构胶有一定的导热能力是更好的,对以结构粘接为主要诉求的结构胶的导热系数能够在0.2W/(m·K)以上,能够起到一定的导热散热功效[空气的导热系数约为0.0267W/(m·K)]。
用于CTP结构电芯粘接用高强度低模量结构胶,是否满足新能源汽车的正常行驶要求,还是需要对整体电池包进行振动台架测试,满足耐冲击振动要求,可以参照《GB/T31467.3电动汽车用锂离子动力蓄电池包和系统第3部分:安全性要求与测试方法》。
工程胶粘剂是一门应用科学,结构胶是应用在动力电池PACK的总装工艺过程中,其应用工艺的重要性不言而喻。
CTP结构的动力电池PACK特点是电芯尺寸加大或特异形状,取消了中间模组或大幅度减少,其组装过程是由电芯直接组装粘接到PACK壳体:粘接用胶量相对较大,涂胶胶线走线相对较长;粘接合拢时间依据自动化程度有所差异;组装粘接完成的动力电池PACK,由于体积较大,搬运相对困难;汽车行业的特点是生产批量大、节拍快。
结构胶要适应以上装配及结构特点,其工艺性能具体要求可以体现在以下几个方面:
一般来说可操作时间是指胶粘剂施胶后保持粘性,不影响粘接效果的时间。对于双组分结构胶,A/B组分混合后就开始反应,一定时间后混合后的胶粘剂会失去粘性,粘接就会出现浸润不好等潜在失效可能,这一段时间可以认为是可操作时间。
由于动力电池PACK部件以及电芯尺寸都比较大,需要涂胶装配零部件较多,在胶粘剂涂敷后到部件合拢粘接装配的时间是装配工艺节拍和设备能力等决定的,那么结构胶的可操作时间就要考虑从A/B组分混合后(如果是双组分的)到粘接部件的合拢装配、工装夹具定位的时间间隔,并留出足够的安全系数。
装配工艺节拍的不同、自动化程度不同,以及后续固化方式的不同等,对应结构胶的可操作时间也会不同。
如果是快节拍装配,常温后固化,则可操作时间要求比较短,可能会要求≥5min,甚至更短;如果是装配节拍相对慢一些且装配线考虑涂胶装配后的加温固化,则可操作时间可以要求更长,甚至要求≥40min。
胶粘剂的固化特性是随着时间推移(或加温等其他措施),其强度逐渐是上升的。结合动力电池PACK粘接组装工艺及后续工艺,粘接后的电池电芯具有一定的结构强度后更方便后续装配工艺的实施,因此结构胶的初固时间(固化速度或达到定位强度时间)也是非常重要的工艺性能指标。
根据PACK装配工艺、工装及设备设计不同,粘接后的固化工艺有常温固化和加温固化两种方式。
为保证组装效率,常温固化的结构胶一般要求尽可能短时间内达到能够搬运等定位强度(约0.5MPa),这一要求与充分的可操作时间有一定矛盾。因此,达到定位强度的初固时间一般在30~60min。
加温固化的结构胶可以兼顾长可操作时间与快速定位初固的要求,初固时间在70~80℃条件下15~20min,达到0.5MPa的定位强度。后固化可在80℃、4h时达到8MPa以上的强度或基本完全固化。加温固化的装配线需要配置加温设备。
动力电池PACK电芯粘接组装过程中,电芯被拿取、定位和涂胶等工艺动作,以及涂胶完成后的组装粘接工艺动作,很有可能需要翻转,涂胶位置也有可能是垂直立面。这要求涂敷在电芯或PACK壳体(或保护层)上的结构胶不能流淌,涂敷的胶粘剂胶线需要保持涂敷的形状,以保证组装粘接的过程可靠稳定。因此,良好的触变性是结构胶必须的工艺性能,以保证涂敷的胶粘剂形状稳定,立面不流淌。
同时,由于动力电池PACK尺寸都比较大,组装过程中的涂胶机器手操作半径范围也大,有的可达2m以上,再加上涂胶工序场地、电芯上装工位以及结构胶胶桶定位工位的实际距离考虑,结构胶的输胶管路长度都比较长,可能达到5~10m,因此结构胶的粘度不宜太高,以便于顺畅打胶,A/B组分混合后的粘度不宜超过60000cps。否则就需要非常高的输送压力,也可能造成出胶速率低,影响涂胶效率、整体装配效率。另外,A/B组分的结构胶,两组分的粘度也不宜相差太大,以保证稳定的混合效果。
一般动力电池的结构胶是双组分的,混合均匀后的胶粘剂才能够发挥其性能,对于A/B组分的混合比例,虽然不是强制性要求,但是考虑到混合的稳定性,实际工程应用中还是A/B组分的比例差别不大的情况下,更能够保证混合均匀及稳定。A/B组分1:1或2:1或4:1的混合比例,有利于涂胶机比较稳定、精确地混合,也有利于粘接质量的稳定保证。
综上所述,动力电池CTP结构的粘接用结构胶,从应用角度来看,基本性能要求具有良好的材质适应性、高强度低模量、良好的耐候性以及阻燃绝缘环保等基础性能。配合动力电池的组装工艺过程,在操作时间、初固定位时间、触变性和混合比例方面有一些工程性的工艺性能要求。富乐公司深入动力电池粘接应用研究,近期推出的动力电池结构胶产品AT1241/AT1242,具有更高的强度更低的模量,完全贴合了新能源汽车的应用环境以及组装工艺要求,可以根据装配工艺常温固化或高温加热固化,让CTP结构的动力电池PACK组装更多选择。
获取更多评论