电驱系统行星齿轮机构齿圈加工工艺
作者:张才源 黄超 等
文章来源:AI《汽车制造业》
发布时间:2022-03-16
本文研究了行星齿轮机构齿圈的加工工艺方法,梳理了常见加工问题并做了详细论证。对热处理加工变形和齿形精加工做了简要描述,定义了热处理工艺方法控制变形,通过小批量验证了工艺稳定性。感应压淬技术能够提高工艺效率,内珩齿工艺能够保证齿轮精度要求。
电动汽车AT变速器里面的行星齿轮机构齿圈广泛采用的热处理工艺为软氮化工艺,热后齿形不再进行精加工,且保证加工精度9级即能满足使用要求。随着电驱行业对NVH要求的日益提高,9级精度不再满足使用要求,对热后加工精度提出了更高要求。目前,国内外电驱系统行星齿轮机构齿圈热后精加工量产工艺研究不广泛,如何使用精加工工艺且对在量产工艺中出现的问题研究不够,导致目前市场无充足的对标,产生了一系列加工及NVH问题等。本文将对行星齿轮机构齿圈的加工工艺重新验证。
行星齿轮机构齿圈机加工序见表1。齿圈结构如图1所示。
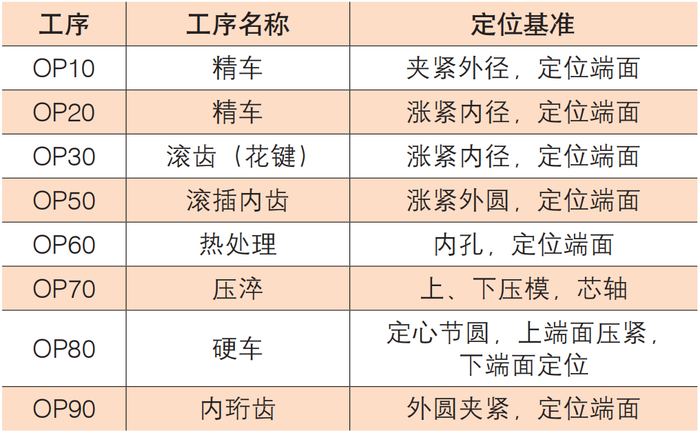
齿形精度等级6级:其中齿形误差fHα±8mm;齿向误差fHβ±8mm;齿形齿向鼓形公差要求±3mm,特殊修缘要求公差±4mm:齿向扭曲要求公差±10mm;齿形径向圆跳动Fr=50mm;齿形累计误差Fp=60mm;齿面粗糙度Rz=2.5mm;以上齿形齿向微观参数要求,齿面必须热后精加工才能满足要求。
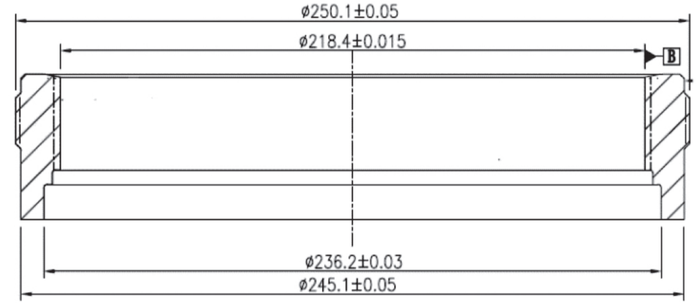
工件采用20MnCrS5或16MnCrS5材料,热处理工艺为:渗碳—回火—感应压淬—回火。热后要求:表面硬度:59HRCmin,芯部硬度:33~45HRC,有效硬化层深:0.3~0.7mm。
精车,即是用刀具从工件上切除多余材料,从而获得形状、尺寸精度及表面质量等合乎要求的零部件的加工过程。实现这一切削过程必须具备以下三个条件:①工件与刀具之间要有相对运动,即切削运动;②刀具材料必须具备一定的切削性能;③刀具必须具有适当的几何参数,即切削角度等。在此工序加工过程中,需要注意的是:因零部件在夹紧切削中为了抗切削力,需加载一定的夹紧力,并且夹紧力越大,零部件变形越大,如夹紧力选得不合适,端面圆跳动和圆度无法保证。
解决方案:建议在OP20工序选用端压卡盘,选取适当的夹紧压力,保证端面圆跳动≤0.02mm,圆度≤0.03mm。夹紧定位如图2所示。
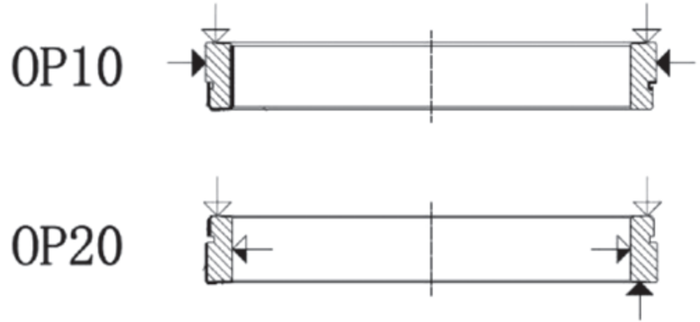
滚齿加工是滚切齿轮,属于展成法,可将其看作无啮合间隙的齿轮与齿条传动。当滚齿旋转一周时,相当于齿条在法向移动一个刀齿,滚刀的连续传动,犹如一根无限长的齿条在连续移动。当滚刀与滚齿坯间严格按照齿轮与齿条的传动比强制啮合传动时,滚刀刀齿在一系列位置上的包络线就形成了工件的渐开线齿形。随着滚刀的垂直进给,即可滚切出所需的渐开线齿廓。
传统的内齿加工有两种:插齿和拉削。但笔者对内齿加工都没有选这两种工艺,为了说明这个问题,首先来了解一下滚插工艺。
滚插工艺:滚插是齿轮的连续切削过程,该项技术结合了滚齿和插齿,通过连续展成轴向进给实现齿形加工。该工艺相较于传统的插齿工艺具有以下优势:①能实现连续切削,效率高40%~50%;②可实现干式切削代替湿式切削,节省了切削液成本及切削液的处理成本。
为什么不选择内拉齿工艺呢?因为齿圈薄壁件需要通过几轮热变形实验确定合适的压力角fHα,螺旋角fHβ及M值余量来固化工艺过程。在此过程中,直径大于200的拉刀要修磨运输显然不是一件很容易的事情。另外,生产周转需要储备一定量的刀具,那么拉刀的投资费用也会很高,灵活性和可操作性太差。如选用内滚插工艺,这些问题都可以迎刃而解。滚插示意如图3所示。解决方案:使用滚插工艺,刀具周期短,热变形调整灵活,效率高。
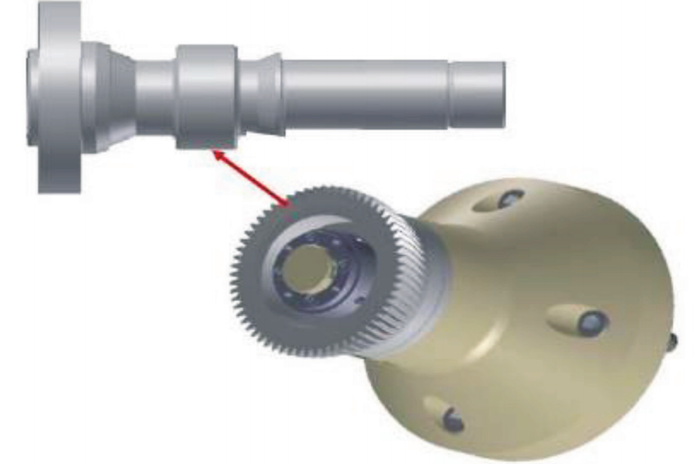
热处理是将钢在固态下加热到预定的温度,并在该温度下保持一段时间,然后以一定的速度冷却到室温的一种热加工工艺,其目的是改变钢的内部组织结构,以改善其材料性能。通过适当的热处理可以显著提高钢的力学性能,适当的热处理工艺可以消除铸、锻和焊等热加工工艺造成的各种缺陷,细化晶粒,消除偏析,降低内应力,使钢的组织和性能更加均匀,延长零部件的寿命。所以,热处理是零部件加工工艺过程中的重要工序。
齿圈在热处理中,加热到预定的温度,因为热胀冷缩,零部件在热处理后因为工件壁薄,热变形大,齿形参数,其中Fr和Fp达0.15mm以上,且不稳定,无法保证内珩齿毛坯质量要求。
解决方案:使用感应淬火压床工艺,可有效地控制变形量。感应压淬是通过感应加热到一定温度后,由上下夹具和芯轴控制零部件变形,其中感应加热是利用电磁感应的方法使被加热的材料的内部产生电流,依靠这些涡流的能量达到加热目的。感应加热系统的基本组成包括感应线圈、交流电源和工件。其中,感应压淬效率较高,适合量产工艺,占地面积小,能耗低,对变形修正能力高。感应压淬的主要参数见表2。

值得探究的是:使用感应压淬工艺过程中,材料20MnCrS5和16MnCrS5,需特别注意选择合适的淬透性材料,同时芯部硬度较难控制。
硬车与前面提到的精车的加工方式基本一样,其不同点如下:①零部件表面由热前状态变成了热处理后状态,表面硬度达到了59HRC以上;②夹具的夹紧定位应该定位在齿轮的节圆上面。
对于本文阐述的齿圈薄壁工件,在硬车工序较容易出现的问题是:①外圆圆度较难稳定控制,对夹具设计要求极高;②前期夹具方案确认时需特别注意夹具需具备抗零部件变形的夹具设计;③在硬质合金刀切削过程中,由于夹紧力和切削力等作用下,导致零部件夹紧变形时外圆圆度超差。
解决方案:首先应该严格地控制余量均匀性,单边余量应为0.18~0.22mm。余量太大,有效硬化层深无法保证,余量太小,吃刀量少,产生加工振纹,无法保证热后图样要求,所以夹具应使用定心和端压,且在夹紧时需先定心,后完成端压,设备需使用单独控制定心和端压,端压选用尽可能大的增加压紧接触面积,以便分散压紧力导致工件变形。
特别建议:定心使用可编程控制移动距离,端压压力实现可编程控制。硬车夹具如图4所示。
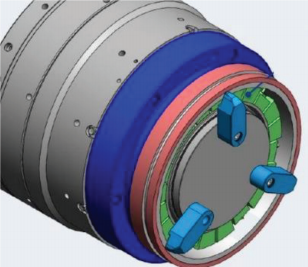
对于内珩齿和内啮合珩齿的相关认识,在目前国内相关文献的定义会产生一些误解,本文阐述的是内齿使用珩齿工艺加工,即为内珩齿。
无论是内珩齿加工(图5),还是外珩齿加工都是工件和砂轮在进行内啮合运动,但本文论述的内珩齿(Innerhoning)的被加工工件为内齿轮,它是在外齿强力珩齿的技术上发展而来。德国PREAWEMA率先投入国内市场使用。
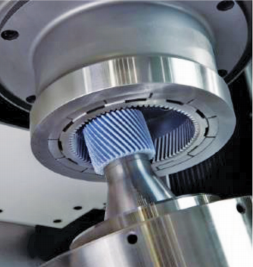
工艺难点主要有三个方面:①零部件夹紧变形,通过软件模拟分析,工件夹紧出现两种变形。解决方案:夹紧外圆实现至少12瓣涨套,可尽可能减小夹紧压力,同时实现零部件克服离心力。
②齿面粗糙度,解决方案:选用合适的砂轮颗粒度,并通过测试找到合适的珩磨参数。
③齿形齿向扭曲控制,解决方案:通过VSD(PREAWEMA专有技术)修整成型,并通过珩磨加工复杂运动方式实现扭曲控制,加工过程中仅需在设备HMI界面设置即可。
1)行星轮系中的齿圈(直径大于200mm)的加工,壁厚度仅约5mm,笔者给了加工工艺选型建议,并经过项目验证,可用于量产工艺。
2)齿圈加工过程中,笔者根据项目执行过程中的风险问题提出了规避措施,措施不是唯一的,供参考。
3)齿圈的热后加工工序尤为重要,其中在使用感应压淬工艺控制零部件变形的过程中,因感应压淬加热时间仅为47s,冷却时间为28s,尤其要注意芯部硬度,前期需与研发工程师确认清楚对强度和疲劳耐久的影响,最终确定设计芯部硬度要求。
4)齿面精加工,目前变速器外齿轮加工磨齿和珩齿的应用各有千秋,笔者建议的内珩齿有两个目的:①珩齿可控制扭曲加工,在不牺牲效率的情况下能稳定扭曲控制要求;②内磨齿设备,目前仅能加工≤200mm的工件,且磨齿实现控制扭曲加工,导致损失加工效率。
正在获取数据......