角接触轴承在纯电动乘用车减速器上的设计与应用
文章来源: EDC电驱未来
发布时间:2020-04-29
今天介绍一种解决纯电动乘用车减速器在大载荷、高转速情况下轴承选用的方法。
现在的纯电动乘用车多采用单挡减速器,减速器结构一般是二级减速,三轴布置。最大输入转矩在70~350N·m,转速6 000~9 000r/min。随着国家对纯电动乘用车的续驶里程要求越来越高,各纯电动乘用车主机厂千方百计节能降噪,纯电动乘用车所用电动机的转速越来越高,功率越来越大。譬如某主机厂的5座SUV乘用车要求减速器的输入转矩达到400N·m,转速达到12 000r/min。
下面介绍一种解决纯电动乘用车减速器在大载荷、高转速情况下轴承选用的方法。
纯电动乘用车减速器设计输入参数
适用车型:SUV,5座;最大输入转矩:360N·m;最高转速:12 000r/min;传动比:9.140;电压范围:320~450V,额定375V;噪声性能:≤78dB;产品寿命:8年/100万km。
纯电动乘用车减速器的高速级轴承的设计
1.减速器传动比计算
采用两级减速,总传动比为9.138,采用T.D.Analysis软件,按轻量化的原则进行传动比分配。一级传动比为2.957,二级传动比为3.091。
2.齿轮参数和中心距计算
n22=16000/9.140=1751r/min
3)计算低速级大轮输入转矩:T22=360×9.140×1000=3290400N·mm
3)通过计算,确定高速级和低速级齿轮几何参数。两级减速齿轮中心距分别是:高速级中心距为95mm,低速级中心距为140mm。齿轮弯曲强度和疲劳强度满足设计要求。
3.轴承设计
2)输入轴轴承选择。选择轴承的输入条件:最高转速16 000r/min,最大轴向力7 752N;
如果将轴的最小轴径作为轴承的内径,按轴承承受的最高转速和最大轴向力,可以选择轴承型号为:角接触轴承7208;深沟球轴承6208。
4.轴承布局设计
(1)角接触轴承的安装方法背对背装配:可承受较大倾覆力矩,预紧调内圈——可用锁紧螺母预紧(见图2)。
面对面装配:承受较小倾覆力矩,预紧调外圈——可用调整垫片调整外圈预紧(见图3)。这种安装方式的轴承,供应商已经配对,一对轴承配好,一起包装,保证了一对轴承的精度,但仍需在装配时调整来保证轴向游隙。
(2)减速器输入轴轴承布局方案 本方案采用:1个深沟球轴承,2个角接触轴承,如图4所示的布置结构。角接触轴承采用面对面装配:外圈通过控制壳体孔深度尺寸公差,实现一定预紧,压板固定;内圈:轴上安装卡环固定。
5.轴承承载能力校核
(1)校核依据 采用MASTA传动系统分析软件,依据1022-2015减速器总成试验规范,工况依据输入峰值转矩300N·m,电动机峰值功率125W。轴承基本损伤率要求应满足表1要求。
1)基本损伤率校核载荷按照QC/T1022-2015试验规范。
4)计算损失率。通过采用MASTA传动系统分析软件进行建模计算,轴承损失率见表3。
5)轴承承载能力校核结论。将表3计算结果与表1要求比较可知:按1022-2015疲劳试验工况试验分析,该纯电动乘用车减速器高速级轴承满足承载能力要求。
纯电动乘用车减速器的高速级角接触轴承的装配
角接触球轴承在纯电动乘用车减速器的高速级输入轴上装配方式如图5所示。2个角接触轴承面对面安装,内圈端面相互并紧无间隙,内圈与输入轴过盈配合,外圈与壳体采用过渡配合。
压板用螺钉固定在壳体上,通过压板压紧角接触轴承外圈,压紧力200~250N。2个角接触轴承外圈端面间隙<0.013mm。
压紧力不能太大,太大则轴承滚珠变形,造成损伤;太小,则不能保证2个角接触轴承端面的间隙,轴承没有预紧力,不能正常运转。
表2 润滑相关参数
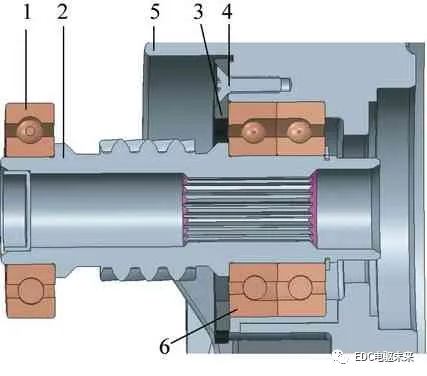
1—深沟球轴承 2—输入轴 3—压板4—螺钉 5—壳体 6—角接触轴承
结语
本文通过对一款纯电动乘用车减速器高速级轴承的设计和应用,提出了一种在纯电动乘用车减速器高速级采用角接触轴承来解决大载荷高转速难题的方案。
该方案克服了采用深沟球轴承不能解决的问题,同时,解决了角接触球轴承装配性能低,不适应批量快速装配的难题。降低了制造成本,满足了客户需求。
正在获取数据......